Introduction to Gerber X2
Gerber X2 is an extension of the standard Gerber format used for PCB design and manufacturing. It was developed by Ucamco, the company that maintains the Gerber format standard. Gerber X2 adds new features and enhancements to the existing Gerber format to improve the efficiency and accuracy of PCB Fabrication.
The standard Gerber format, while widely used and supported, has some limitations. It does not include all the necessary information for PCB fabrication in a single file. Extra data like the layer structure, drill sizes, finishes, and layout are typically provided in separate files or formats. This can lead to errors and miscommunication between PCB designers and manufacturers.
Gerber X2 aims to solve these issues by incorporating all the essential PCB fabrication data into the Gerber file itself. It uses a human-readable ASCII format that is easy to parse and understand. Gerber X2 files have the extension “.gbr” and can be opened with any text editor or Gerber viewer supporting the X2 format.
Key Features of Gerber X2
Attribute Data
One of the main features introduced in Gerber X2 is attribute data. Attributes allow embedding additional information directly into the Gerber file. There are two types of attributes in Gerber X2:
- File attributes
- Object attributes
File attributes provide metadata about the entire Gerber file, such as:
- The PCB design software used
- The part number or revision of the PCB
- The company or designer name
- The layer structure and order
- The file function (e.g., Top Copper, Solder Mask, etc.)
Object attributes are associated with specific graphics objects (pads, tracks, polygons, etc.) in the Gerber file. They can specify properties like:
- Pad functions (SMD, through-hole, fiducial, etc.)
- Drill sizes and types
- Component pin numbers
- Net names
- 3D model references
Attributes are enclosed in %
characters and have a key-value format. For example:
%TF.FileFunction,Copper,L1,Top*%
%TF.Part,Single*%
%TA.AperFunction,SMDPad,CuDef*%
Nested Step and Repeat
Gerber X2 introduces a new command for step and repeat operations called “SR”. It allows defining a group of objects and replicating them in a grid or array pattern. The SR command is more flexible than the standard Gerber step and repeat (SR/AR) as it supports nested step and repeat blocks.
Nested step and repeat means you can have an SR command inside another SR command. This is useful for defining complex array patterns or replicating hierarchical designs.
The syntax for the SR command is:
SRXxYy,Iix,Jjx;
<object or nested SR command>
<object or nested SR command>
...
Where:
– Xx
and Yy
specify the number of columns and rows in the array
– Iix
and Jjx
specify the distance between columns and rows
– x
is the unit (e.g., IN for inches or MM for millimeters)
Composite Apertures
Gerber X2 adds support for composite apertures, which are custom shapes defined as a combination of standard apertures. This allows creating complex pad shapes without the need for polygon fills or aperture macros.
A composite aperture is defined using the “AD” command followed by a series of primitive shape additions or subtractions. The primitives can be circles, rectangles, obround, or polygons.
For example, to define a rectangular pad with rounded corners:
%AMROUNDPAD*
1,1,$1,$2-$3/2-$5,$3/2+$5*
1,1,$1,0-$5,0+$5*
1,1,$1-$2+$3/2+$5,-$3/2-$5*
1,1,$1-$2+$5,0-$5*
$4=$1/8*
1,1,$4,-$2*
1,1,$4-$2+$3/2,$3/2*
1,1,$4-$2,$2*
1,1,$4-$2+$3/2,-$3/2*
%
%ADD100ROUNDPAD,0.050X0.100X0.075X0.025*%
This defines a composite aperture named “ROUNDPAD” with parameters for the pad size and corner radius. It can then be referenced in the Gerber file using the D100 aperture number.
Back Drilling
Gerber X2 introduces support for back drilling, a technique used to remove unused portions of through-holes to improve signal integrity in high-speed PCB designs. Back drilling information is specified using object attributes associated with the drill holes.
The BK
attribute specifies the back drilling parameters:
BK,<start depth>,<end depth>,<method>*
Where:
– start depth
and end depth
are the depths to start and stop drilling, relative to the top surface of the PCB
– method
is the type of back drilling (e.g., Constant
, Variable
)
For example:
%TA.DrillFunction,BackDrill*%
%TA.BK,0.0200,0.0500,Constant*%
X100Y200D03*
This specifies a back drilled hole at location (100, 200) with a start depth of 0.020″ and an end depth of 0.050″ using the constant depth method.
Embedded Components
Gerber X2 adds support for embedded components, which are components mounted inside the PCB substrate instead of on the surface. Embedded components can save space and improve performance in dense PCB designs.
Embedded component information is specified using object attributes associated with the component footprint in the Gerber file. The Embed
attribute indicates that the component is embedded, and the EmbedType
attribute specifies the type of embedding (e.g., Cav
for cavities, IntL
for internal layers).
For example:
%TA.ComponentFunction,Resistor*%
%TA.Embed*%
%TA.EmbedType,Cav*%
D10*
X1000Y2000D03*
This specifies an embedded resistor footprint at location (1000, 2000) using a cavity embedding type.
Advantages of Gerber X2
Single File Format
One of the main advantages of Gerber X2 is that it consolidates all the necessary PCB fabrication data into a single file format. This eliminates the need for separate files for drill data, netlist, component placement, and other manufacturing information.
Having a single file format simplifies data exchange between PCB designers and manufacturers. It reduces the chances of errors or omissions in the fabrication data and ensures that all the required information is conveyed accurately.
Human-Readable Format
Gerber X2 uses a human-readable ASCII format that is easy to understand and parse. The commands and attributes in a Gerber X2 file are self-explanatory and can be read by anyone with basic knowledge of the format.
This makes it easier to debug and troubleshoot issues in the PCB design data. It also allows for manual editing or modification of the Gerber file if needed.
Improved Design Verification
The additional information provided by attributes in Gerber X2 enables better design verification and analysis. PCB Manufacturers can use the attribute data to check for design rule violations, manufacturability issues, and other potential problems before starting production.
For example, the pad function and drill size attributes can be used to verify that the PCB design matches the intended bill of materials (BOM) and component specifications. The layer structure and stack-up attributes can be used to ensure that the PCB Stackup is correct and meets the required specifications.
Streamlined Manufacturing Process
By providing more comprehensive and accurate PCB fabrication data, Gerber X2 streamlines the manufacturing process and reduces the need for manual intervention or clarification. The single file format and standardized attributes make it easier for PCB manufacturers to extract the necessary information and set up their fabrication systems.
This can lead to faster turnaround times, fewer manufacturing defects, and lower production costs. It also reduces the likelihood of delays or errors due to miscommunication or incomplete data.
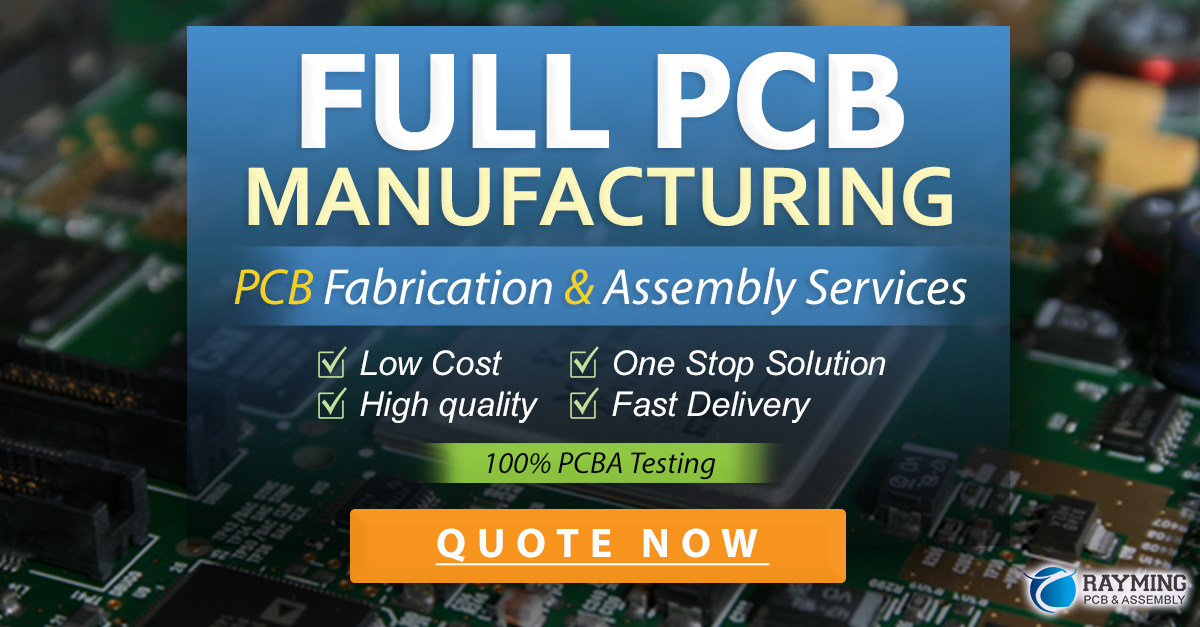
Adoption and Support
Since its introduction in 2014, Gerber X2 has been gaining adoption and support from PCB design software vendors and manufacturers. Many popular PCB design tools, such as Altium Designer, Cadence Allegro, and Zuken CR-8000, now support exporting Gerber X2 files.
PCB manufacturers are also increasingly supporting Gerber X2 as an input format. The standardized attributes and single file format make it easier for them to parse and process the fabrication data.
However, the adoption of Gerber X2 is still an ongoing process, and not all PCB design tools and manufacturers support it yet. The standard Gerber format (RS-274X) is still widely used and supported, and many designers and manufacturers are comfortable with their existing workflows.
To encourage adoption, Ucamco provides free tools and resources for working with Gerber X2, including:
- A Gerber X2 specification document and quick reference guide
- A free Gerber X2 viewer and analyzer called “GerberLogix”
- Sample Gerber X2 files and tutorials
- A Gerber X2 conformance test suite for validating Gerber X2 output from PCB design software
As more designers and manufacturers see the benefits of Gerber X2 and adopt it into their workflows, it is expected to become the preferred format for PCB fabrication data exchange.
Conclusion
Gerber X2 is a significant advancement in the world of PCB design and manufacturing. By extending the standard Gerber format with powerful new features and attributes, it enables more efficient, accurate, and streamlined PCB fabrication.
The single file format, human-readable syntax, and comprehensive attribute data make Gerber X2 a powerful tool for conveying PCB design intent and ensuring manufacturability. It benefits both PCB designers and manufacturers by reducing errors, improving communication, and streamlining the production process.
As adoption and support for Gerber X2 continue to grow, it has the potential to become the de facto standard for PCB fabrication data exchange. By embracing Gerber X2, the PCB industry can move towards a more robust, reliable, and efficient future.
Frequently Asked Questions (FAQ)
What is the difference between Gerber X2 and the standard Gerber format?
Gerber X2 is an extension of the standard Gerber format (RS-274X) that adds new features and attributes for conveying PCB fabrication data. While the standard Gerber format uses separate files for different layers and fabrication data (e.g., drill files, netlist), Gerber X2 consolidates all the necessary information into a single file format. Gerber X2 also introduces powerful new features like nested step and repeat, back drilling, and embedded components.
Is Gerber X2 backward compatible with the standard Gerber format?
Yes, Gerber X2 is designed to be backward compatible with the standard Gerber format. A Gerber X2 file can contain both standard Gerber commands (e.g., D-codes, aperture macros) and new X2 attributes and commands. This allows existing Gerber viewers and tools to open and interpret Gerber X2 files, even if they don’t support all the new X2 features.
What software tools support Gerber X2?
Many popular PCB design software packages now support exporting Gerber X2 files, including:
– Altium Designer
– Cadence Allegro
– Zuken CR-8000
– KiCad
– Eagle
In addition, there are several free and commercial Gerber X2 viewers and analysis tools available, such as:
– GerberLogix (free viewer from Ucamco)
– ViewMate (commercial viewer from Pentalogix)
– GC-Prevue (commercial viewer from GraphiCode)
– CAM350 (commercial viewer from DownStream Technologies)
How can I learn more about Gerber X2?
To learn more about Gerber X2, you can refer to the official Gerber X2 specification and documentation provided by Ucamco, the company that maintains the Gerber format. They offer a comprehensive specification document, quick reference guide, tutorials, and sample files on their website (www.ucamco.com/gerber-x2).
You can also find articles, tutorials, and discussions about Gerber X2 on various PCB design forums and blogs. The PCB design community is actively exploring and adopting Gerber X2, and there are many resources available to help you get started.
What are the benefits of using Gerber X2 for PCB manufacturing?
Using Gerber X2 for PCB manufacturing offers several benefits, including:
-
Simplified data exchange: By consolidating all the necessary fabrication data into a single file format, Gerber X2 simplifies data exchange between PCB designers and manufacturers. This reduces the chances of errors or omissions in the fabrication data.
-
Improved design verification: The additional information provided by attributes in Gerber X2 enables better design verification and analysis. PCB manufacturers can use the attribute data to check for design rule violations, manufacturability issues, and other potential problems before starting production.
-
Streamlined manufacturing process: Gerber X2 provides more comprehensive and accurate PCB fabrication data, which streamlines the manufacturing process and reduces the need for manual intervention or clarification. This can lead to faster turnaround times, fewer manufacturing defects, and lower production costs.
-
Human-readable format: Gerber X2 uses a human-readable ASCII format that is easy to understand and parse. This makes it easier to debug and troubleshoot issues in the PCB design data and allows for manual editing or modification of the Gerber file if needed.
-
Future-proofing: As the PCB industry continues to evolve and new manufacturing technologies emerge, Gerber X2 provides a flexible and extensible format for conveying design intent and fabrication data. By adopting Gerber X2, PCB designers and manufacturers can future-proof their workflows and be better prepared for new challenges and opportunities.
Leave a Reply