Electronic manufacturing services (EMS) provide end-to-end manufacturing solutions for electronic components and assemblies like printed circuit boards (PCBs). As products become more complex and technologically advanced, many companies are partnering with EMS providers that have the expertise and capabilities to manufacture innovative PCB designs reliably and at scale. This guide covers key considerations in selecting the right EMS PCB manufacturing partner for your needs.
Overview of EMS PCB Manufacturing Services
EMS companies offer a full suite of PCB manufacturing and assembly services, including:
- PCB fabrication – Producing bare PCBs from gerber files. Services include laminating, drilling, imaging, etching, testing.
- PCB assembly – Soldering and assembling components onto fabricated PCBs. Services include SMT assembly, thru-hole assembly, testing, inspection.
- New product introduction (NPI) – Supporting the design, prototyping, testing, and ramp-up to mass production.
- Supply chain management – Procurement and provisioning of required components and raw PCB materials.
- Logistics and fulfillment – Warehousing, inventory management, order fulfillment and shipping.
Partnering with an EMS provides benefits like:
- Cost savings – Economies of scale and specialization in PCB manufacturing leads to lower costs.
- Expertise and capabilities – Access to skills, engineering resources, specialized equipment for advanced PCB technologies.
- Speed – Faster time-to-market by leveraging capabilities and capacity on-demand.
- Flexibility – Ability to rapidly adjust to changing market conditions and customer requirements.
- Quality – Advanced quality control and reliability testing capabilities.
- Focus – In-house teams can focus on design and innovation rather than manufacturing.
Key Factors in Selecting an EMS PCB Manufacturer
Choosing the right EMS partner is crucial in getting quality boards delivered on time. Here are key factors to evaluate:
Technical Capabilities
- Services offered – Needed services like PCB fabrication, component assembly, testing, etc.
- Board complexities supported – HDI, flex/rigid flex, high layer counts, advanced packaging, etc.
- Component assembly technologies – Fine-pitch components, BGAs, 01005s, etc.
- Certifications – ISO, IATF 16949, AS9100, ITAR, etc.
- Equipment – Cutting-edge fabrication and assembly equipment.
- Engineering skills – Experienced engineers to support complex PCB designs.
- Quality processes – Robust quality control and management processes.
- Testing capabilities – Extensive component, electrical, functional testing options.
- Prototyping abilities – Quick-turn prototype PCB manufacturing.
- Manufacturing processes – Lean and efficient production systems.
Capacity and Scalability
- Production capacity – Volume capabilities aligned with current and future production needs.
- Scalability – Ability to rapidly scale up or down to meet changing demand.
- Multi-site capacities – Production redundancies across global facilities.
- Supply chain infrastructure – Established network of component suppliers.
Service and Support
- Design support – DFM analysis, design review and recommendations.
- NPI support – Smooth transition from design to mass production.
- Account management – Dedicated teams for program management and customer service.
- Communication – Timely responses and proactive project updates.
- Continuous improvement – Commitment to continuously enhance quality, costs and delivery.
Global Footprint and Logistics
- Manufacturing locations – Proximity to target markets for faster delivery.
- Facilities network – Ability to transition production across different sites if needed.
- Supply chain locations – Component inventory located close to production facilities.
- Customs expertise – Streamlined global trade compliance processes.
- Logistics capabilities – Solutions for delivery to multiple regions.
Evaluating Specific EMS Companies
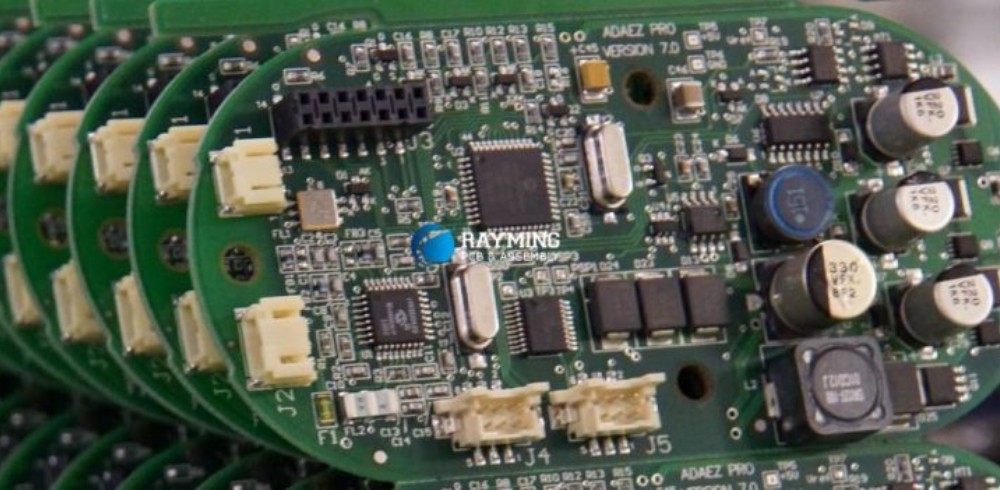
With thousands of EMS providers globally, it helps to create a shortlist of leading candidates to evaluate further. Here is an overview of top EMS companies to consider for PCB manufacturing:
Jabil
- One of the largest global EMS companies
- 270+ facilities in over 30 countries
- Broad range of assembly technologies and PCB capabilities
- Expertise in regulated industries like aerospace, automotive, healthcare
- $29.3B in revenue, 200,000+ employees (2021)
Flex
- Top 5 global EMS provider
- 100+ sites in over 30 countries
- Strengths in consumer, automotive, healthcare, aerospace/defense
- Flexible multi-site production and supply chain
- $26.0B revenue, 167,000 employees (2021)
Sanmina
- Leading EMS focused on high-mix, low-to-mid volume programs
- 80+ manufacturing sites globally
- Advanced engineering and new product introduction services
- Focused quality programs like zero defect and cycle time reduction
- $6.7B revenue, ~25,000 employees (2021)
Benchmark Electronics
- Top 10 EMS company worldwide
- Strengths in prototype builds, new product introduction
- 8 world-wide technical centers to support complex designs
- Robust IT infrastructure for supply chain management
- $2.7B revenue, ~10,000 employees (2021)
Plexus
- Services networking/telecom, healthcare, defense/security, industrials
- 19 manufacturing facilities across America, Europe, and Asia
- Miniaturization and flexible PCB capabilities
- Value-engineering and aftermarket services
- $3.6B revenue, ~16,000 employees (2021)
EMS Company | Locations | Revenue | Employees |
---|---|---|---|
Jabil | 270+ facilities, 30+ countries | $29.3B | 200,000+ |
Flex | 100+ sites, 30+ countries | $26.0B | 167,000 |
Sanmina | 80+ manufacturing sites globally | $6.7B | ~25,000 |
Benchmark Electronics | Facilities worldwide | $2.7B | ~10,000 |
Plexus | 19 manufacturing facilities globally | $3.6B | ~16,000 |
Table 1: Comparison of major global EMS companies
This is just a sampling of major EMS providers that offer strong PCB and electronic assembly capabilities. Beyond evaluating companies individually, you also need to look at specific programs and teams to find the best fit. Interacting with account managers and facility tours can provide more insights on competencies, expertise, and cultural alignment.
Key Questions to Ask Prospective EMS Partners
To further assess EMS providers under consideration, here are some key questions to ask:
Technical Capabilities
- What PCB and component assembly technologies do you specialize in? What complexities can you support?
- What new innovations in fabrication and assembly are you investing in?
- How will you support our specific technical PCB requirements for this product?
- Can you meet our quality requirements and achieve the yields we expect?
Capacity and Scalability
- What is your current capacity and availability? How flexible is your production scheduling?
- How quickly can you scale production up or down to match demand swings?
- Do you have redundant manufacturing sites and suppliers to mitigate risks?
Quality Processes
- What quality certifications do your facilities maintain? What is your process and track record?
- How will you verify quality at every stage – components, fabrication, assembly, testing?
- How will you ensure repeatability and consistency across production runs?
Supply Chain Capabilities
- How will you secure all the required components for production, including long-lead items?
- Where do you source components from? Are there local suppliers near your facilities?
- How do you deal with component shortages or obsolescence? Do you have alternate sources?
Cost Factors
- What are your rates for services like PCB fabrication, component assembly, etc?
- How do you optimize costs via supply chain, quality, logistics, and efficiencies?
- What is your process for cost reduction over the product lifecycle?
Program Management
- Who will be the dedicated program management team and key contacts for our account?
- How will you support new product introduction and the transition to mass production?
- How do you communicate with customers and provide production updates or issue resolution?
Thoroughly vetting prospective EMS partners on these aspects will ensure you select the right match for your specific PCB manufacturing needs and build a successful long-term relationship.
Trends in EMS PCB Manufacturing
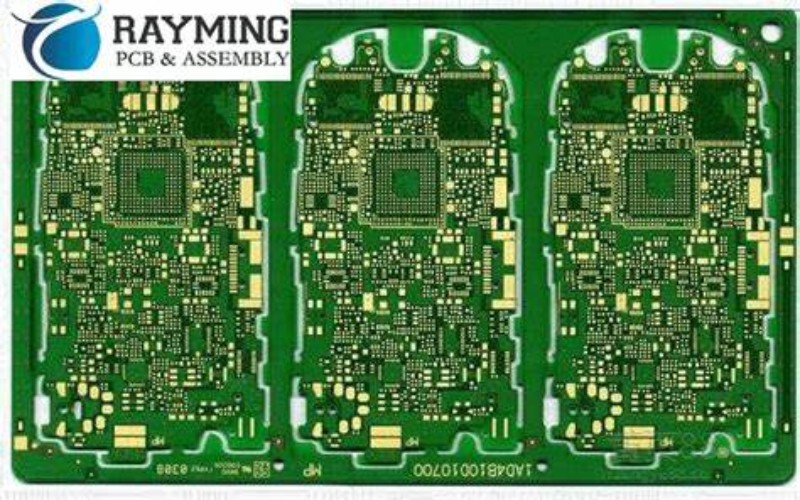
The EMS industry continues to evolve to meet the needs of customers producing advanced electronic devices and assemblies. Some key trends shaping PCB manufacturing services today include:
Miniaturization – Producing smaller, lighter, and more compact PCB designs with higher component densities and packaging innovations like wafer-level packaging.
Heterogenous integration – Integration of multiple technologies like silicon, organic substrates, and embedded components in a single package.
High-frequency PCBs – Boards supporting high-frequency applications in 5G, radar, imaging, navigation, and communications.
Additive manufacturing – Use of 3D printing to produce complex PCBs with benefits like fewer layers and embedded components.
Advanced testing – More extensive testing like X-ray inspection and automated optical inspection (AOI) to ensure quality and reliability.
Smart factories – Leveraging IIoT, automation, and data analytics to enable intelligent manufacturing, predictive maintenance, and production control.
Sustainable solutions – Solutions to improve energy efficiency, reduce waste, utilize recycled/biodegradable materials, and ensure ethical sourcing.
Keeping up with the latest PCB manufacturing innovations allows EMS providers to offer differentiated capabilities and solutions tailored to emerging customer needs.
Conclusion
As PCBs and electronic assemblies grow more complex, partnering with a competent and reliable EMS provider is key to getting them manufactured right the first time. Carefully evaluating technical capabilities, capacity, quality systems, supply chain infrastructure, costs, program management approach, and long-term roadmap of prospective EMS companies is crucial in finding the ideal match. Establishing a close collaboration with an EMS partner equipped to meet current and future needs will enable bringing quality products to market faster.
Frequently Asked Questions
Q: What are the typical steps in the EMS PCB manufacturing process?
A: The major steps in EMS PCB manufacturing usually include:
- Sourcing components required for assembly
- Fabricating the bare PCB from the gerber file
- Solder paste screening and pick-and-place assembly
- Reflow/through-hole component soldering
- In-circuit and functional testing
- Conformal coating, potting, enclosures if needed
- Final integrated assembly testing
- Packaging and shipping
Q: Should I use the same EMS provider for prototyping and mass production?
A: Using the same EMS provider can help smooth the transition from prototyping to mass production. However, some companies offer specialized prototyping services and capabilities that may not be cost effective for high volume production. Evaluate both using a single partner vs. switching for optimal results.
Q: How can I reduce costs when working with an EMS?
A: Strategies like design for manufacturing (DFM), component engineering, aggregated purchasing, test optimization, quality improvements, and volume discounts can help reduce EMS costs over time. Work closely with your EMS partner on cost-focused programs.
Q: What are flex and rigid-flex PCBs?
A: Flex PCBs use flexible base materials that can bend and flex. Rigid-flex combines both rigid and flexible materials in one design. They enable lighter, thinner and more dynamic PCB constructions. Not all EMS companies offer these specialized capabilities.
Q: How are EMS providers incorporating sustainability practices?
A: Leading EMS companies are reducing energy and water usage in facilities, minimizing waste, using recycled/biodegradable materials, and ensuring ethical component sourcing and labor practices. Ask partners about their sustainability programs.
Leave a Reply