Introduction
Printed circuit boards (PCBs) are essential components in nearly every electronic device, from computers and smartphones to industrial equipment and medical devices. As products become more complex, having a custom PCB designed and manufactured is often necessary to fit all the required components into a compact form factor. Choosing the right custom circuit board manufacturer is crucial for getting high-quality boards produced on time and on budget. This article provides guidance on selecting the best partner for your next PCB project.
What Makes a Good Custom Circuit Board Manufacturer?
Advanced Manufacturing Capabilities
Look for manufacturers that offer the latest fabrication technologies and equipment. The most advanced processes provide greater precision, miniaturization, and reliability. Key capabilities to consider include:
- Fine line/space PCBs (traces and gaps under 6 mil)
- High layer count boards (20+ layers)
- Blind and buried vias for interlayer connections
- Flex and rigid-flex PCBs
- HDI (High Density Interconnect) for dense component mounting
- Quick turnaround prototyping
Material and Testing Expertise
The best manufacturers have expertise in a wide range of PCB materials, finishes, and specifications. They can advise on the optimal materials and board stackup for your design requirements. Also look for extensive testing capabilities to ensure quality and reliability:
- Material analysis (resin content, glass transition temp, decomposition temp)
- Microsectioning to examine layer alignment and lamination
- Electrical testing for shorts, opens, impedance
- Environmental stress testing (temperature, humidity, vibration)
Design for Manufacturability
Experienced manufacturers will review your design files and provide DFM (Design for Manufacturability) feedback to avoid potential fabrication issues. This input can improve yield, reduce costs, and speed up delivery times.
Customer Service and Communication
From the initial quote through delivery, the manufacturer should provide excellent customer service. Look for quick response times and clear communication at every stage. They should submit engineering questions and provide timely manufacturing updates.
Top Factors in Choosing a PCB Manufacturer
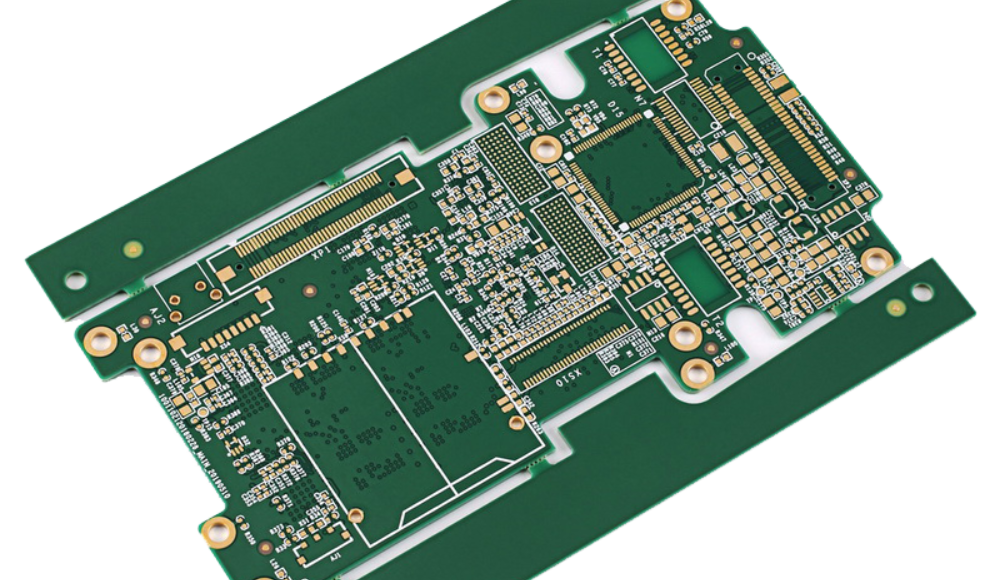
Capabilities Match Your Project
Review the manufacturer’s website and request product brochures to see their capabilities and specialties. Make sure they have experience with projects similar to yours and can meet your board specs, tolerances, and delivery requirements.
Quality and Reliability Record
Ask about the manufacturer’s quality certifications (ISO 9001, IPC, UL), internal quality processes, and historical yields. Reliable partners will have a proven track record of delivering high-quality boards. Request customer referrals.
Competitive Pricing
Get quotes from multiple manufacturers. Be wary of prices that seem too low, as quality may suffer. Consider total cost (NREs, tooling, etc), not just unit price. The best value balances cost with consistent quality output.
Professional Engagement
Interview reps from each manufacturer before selecting your partner. Gauge their responsiveness, knowledge, and customer focus. The ideal partner will provide expert guidance during design reviews and resolving production issues.
Production Capacity
Ask about production lead times and capacity commitments. Choose a manufacturer that can deliver on schedule without long backlogs. Confirm they have capacity for your required order quantities, both now and in future growth projections.
Secure IT Infrastructure
For many products, protecting customer data and IP is critical. Ask about the measures in place to ensure manufacturing data security. Look for restricted employee access, data encryption, and compliance with regulations like ITAR.
Getting Started: Design Review and Documentation
Once you’ve selected a manufacturer, the next step is design review and documentation to finalize the PCB fabrication details.
Submit Gerber Files
Provide the Gerber files for all required PCB layers so the manufacturer can review your design. Confirm which file extensions and formats are acceptable.
Share Critical Specifications
Supply all critical board specifications needed for fabrication. This includes layer count, board thickness, dielectric materials, copper weights, finished hole sizes, tolerances, and more.
Define Testing Requirements
Specify which tests you require (e.g. flying probe, AOI, ICT, functional testing). This ensures all boards are adequately tested before shipment.
Request DFM Feedback
Ask for DFM analysis of your design to identify any recommended improvements for manufacturability and reliability. Implement any critical feedback.
Complete Documentation
Fill out all required engineering and manufacturing forms. This may include QMS forms, application forms, and detailed fabrication drawings. Follow templates if provided.
Optimizing Designs for Production
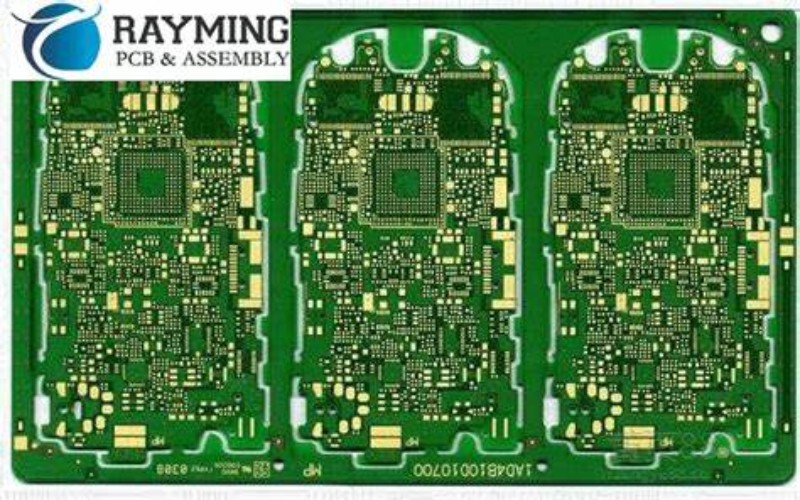
There are many design techniques PCB designers can use to optimize manufacturability, yield, and end product reliability. Here are some key considerations when preparing a design for volume production.
Allow Sufficient Tolerances
Leave adequate tolerances on trace widths, annular rings, hole sizes, spacing, etc. Tighter tolerances drive down yields and raise costs. Discuss appropriate tolerances with your manufacturer.
Minimize Board Warpage
Warpage can cause assembly and test issues. Use techniques like symmetric layer stacking, modal analysis, and warp mitigation lines to minimize warpage.
Enable Testability
Include test points, vias, and other design-for-test structures. This facilitates in-circuit testing and helps debug the boards if issues arise.
Control Impedances
Tune trace widths, dielectric materials, and ground planes to achieve target impedance on critical traces (match lengths, minimize stubs). Consult the PCB manufacturer on how to model and meet impedance requirements.
Address Thermal Issues
Identify components needing heat sinks or thermal vias. Optimizing cooling avoids temperature related failures. Thermal modeling helps predict necessary heat dissipation.
Follow IPC Standards
Design to IPC standards for quality, reliability, and ease of manufacturing. IPC-2221 and IPC-2222 cover important PCB design and fabrication details.
Key Production Preparation Steps
Proper planning and coordination with your manufacturer ensures a smooth PCB production process. Follow these best practices before your board run.
Finalize All Documentation
Double check that all necessary order forms, drawings, test specs, data sheets, and BOMs have been submitted and reviewed for accuracy. This prevents delays or errors.
Procure Long Lead Items
Confirm delivery times for any components or materials with long procurement lead times. Order early to avoid shortages delaying PCB production.
Establish Testing Approach
Determine how boards will be tested – which tests performed at what production stages. This ensures thorough validation while minimizing test costs.
Define Quality Requirements
Specify your quality standards and expectations. Statistical sampling plans, acceptable defect levels, critical dimensions, and remedies for out-of-spec boards should be established.
Create Data Security Plan
If your project involves confidential data, work with your manufacturer to implement a comprehensive data security plan that addresses all vulnerabilities.
Schedule Production
Book production time in advance to secure the desired slot. Confirm the schedule with all stakeholders and understand the cancellation policy if dates need to shift.
Key Factors in PCB Quality and Reliability
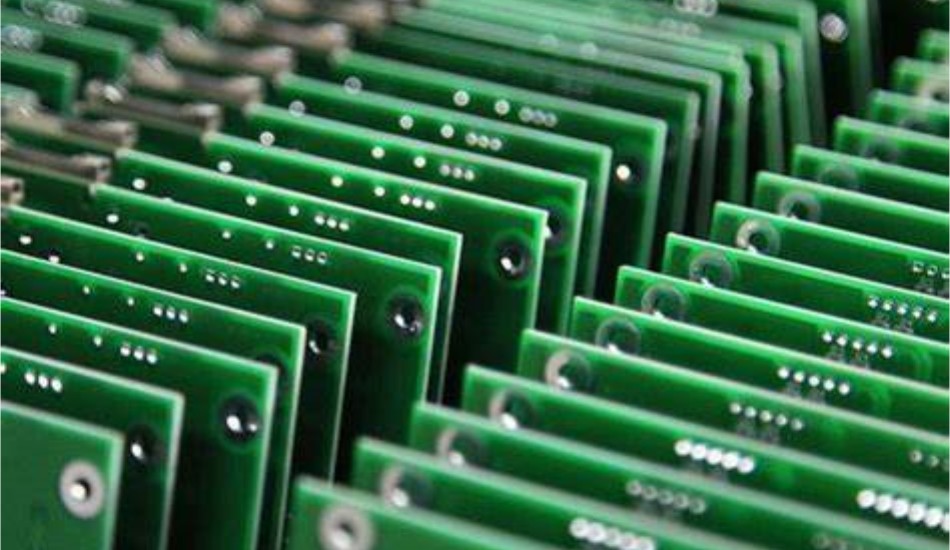
Many technical factors impact the quality, performance, and longevity of custom printed circuit boards. Here are some of the most important considerations.
Base Material Selection
The resin system, glass style, and base copper material determine fundamental PCB properties like Tg, thermal performance, moisture absorption, CTE, etc.
Lamination Process
The pressure, temperature, and time applied during multilayer lamination must be optimized to achieve minimal voids, secure layer-to-layer adhesion, and prevent resin starvation.
Plating Quality
The copper plating process must deposit a uniform, void-free copper layer with good bond strength to the base laminate. Plating issues can lead to poor reliability.
Etch Control
Closely controlling the etch process produces the intended conductor geometries and prevents excessive undercut. Automated optical inspection helps catch etch defects.
Registration
Precise layer-to-layer registration/alignment ensures pads and holes are positioned correctly for assembly. Typical registration tolerance is under 5 mils.
Surface Finishes
Lead-free assembly requires solder mask defined (SMD) pads with an organic solderability preservative (OSP) or immersion silver finish.
Via Integrity
Well-formed, properly filled vias are essential for interlayer connectivity.Voiding, resin starvation, or poor plating adhesion in vias can cause reliability issues.
Cleanliness
PCBs must be kept clean during all manufacturing steps. Contamination can lead to electrical leakage or assembly problems. Regular cleaning and inspection help ensure cleanliness.
Choosing a Domestic vs. Overseas Manufacturer
There are many factors to weigh when deciding between a domestic PCB manufacturer based in your country vs. going overseas. Here is an overview of the key considerations.
Lead Time
For quick-turn prototyping needs, a local manufacturer generally provides faster delivery without lengthy shipping times. Large production runs can be more cost effective overseas.
Communication
Domestic manufacturers make communication easier with no language barriers or time zone differences. This aids collaboration during design reviews and resolving production issues.
Travel for Audits
Visiting a manufacturer’s facilities for an on-site audit is easier domestically. Audits help ensure quality processes and give confidence in the partner.
Shipping/Logistics
Transporting PCBs long distances can increase costs and risks of damage or customs delays. Local supply eases logistics.
ITAR/IP Concerns
If the product has strict data security requirements or export control restrictions, a domestic manufacturer may be preferable.
Pricing
For the same capabilities, offshore pricing is often lower, especially at higher quantities. But total cost difference may be smaller than straight unit price.
Consistent Quality
Reputable domestic manufacturers often have tighter process controls ensuring consistent quality. Defect rates may be higher with some offshore options.
Supply Chain Disruptions
Recent events have shown offshore supply chains are more susceptible to delays from pandemics, politics, or natural disasters.
There is no universal best option – choose based on specific priorities for capabilities, quality, lead time, IP protection, and budget.
Key Questions to Ask Prospective Manufacturers
Thoroughly vet potential PCB manufacturers during the selection process. Below are some of the most important questions to ask.
- What are your capabilities and capacity for our board size, layer count, tolerances, and order volume?
- Which specific PCB materials, finishes, and fabrication processes do you have expertise with?
- Can you provide examples of past customer projects similar to ours that you have manufactured successfully?
- How will you ensure quality and repeatability across our entire production run?
- What design for manufacturability feedback do you have based on our Gerber files?
- What testing capabilities do you have in-house? How are boards tested during fabrication?
- How do you validate the materials and processes used meet the required specifications?
- What data security and IT controls do you have in place? How is our IP protected?
- What support is available during design reviews, fabrication, and if production issues occur?
- What are the standard warranty terms? What happens when boards are found defective?
- Can you provide customer references we can contact to learn about their experience?
Taking the time to thoroughly evaluate prospective PCB manufacturers will pay dividends with a smoother production process and higher quality boards.
Conclusion
Choosing the right partner is critical when outsourcing custom PCB manufacturing. This guide reviewed the key capabilities and qualifications to look for in a manufacturer. Getting expert design feedback, optimizing for manufacturability, establishing robust quality processes, and maintaining close collaboration during production will lead to the best results. With the right partner, your next circuit board project will meet requirements the first time and deliver reliable, high performing products to your customers.
Frequently Asked Questions
What are the typical steps in the PCB manufacturing process?
Major steps include: design/documentation, prototyping, pre-production engineering, fabrication, assembly, testing, inspection, shipment, and field support. Each step involves extensive collaboration between the customer and manufacturer.
Should every PCB design go through a prototyping phase before full production?
Prototyping is highly recommended. It allows you to validate the design, evaluate manufacturability, downstream assembly, performance and make modifications before committing to a full production run. Prototyping reduces risks and prevents costly mistakes.
What types of inspection and testing are performed during PCB production?
Typical testing includes: automated optical inspection (AOI) for defects, in-circuit testing (ICT) for electrical faults, flying probe testing, x-ray inspection of vias/holes, impedance testing, and functional testing of assembled boards.
How long does a typical PCB production run take after completing design?
For small quantities of simple boards, production can be as fast as 2-3 days. Complex, high-reliability boards in large quantities typically take 3-4 weeks from completed design to shipment.
What design data does a PCB manufacturer need for fabrication?
They need all the Gerber files specifying PCB layers, bill of materials, board specs, documentation of any special requirements, assembly drawings, and approval of the manufacturing drawings they generate.
Leave a Reply