What is Curtain Coating?
Curtain coating is a process where a continuous, free-falling curtain of liquid coating material is formed and deposited onto a moving substrate. The coating material is pumped through a slot die or a slide die, creating a stable, uniform curtain that falls onto the substrate below. As the substrate moves beneath the curtain, a thin, even layer of the coating material is applied to its surface.
Advantages of Curtain Coating
Curtain coating offers several advantages over other coating methods:
- High-speed coating: Curtain coating allows for high-speed substrate movement, enabling faster production rates compared to other coating techniques.
- Precise layer thickness control: The thickness of the applied layer can be precisely controlled by adjusting the flow rate of the coating material and the speed of the substrate.
- Multiple layer capability: Curtain coating can simultaneously apply multiple layers of different materials, reducing the need for multiple coating steps.
- Smooth and uniform coatings: The free-falling curtain ensures a smooth and uniform coating layer, minimizing defects and irregularities.
Low Pressure Impact (LPI) Applying Method
The Low Pressure Impact (LPI) applying method is a variant of curtain coating that focuses on reducing material loss while maintaining high coating speeds. In this method, the coating material is applied to the substrate at a lower pressure than traditional curtain coating, minimizing the impact force between the curtain and the substrate.
How LPI Works
- Low-pressure curtain formation: The coating material is pumped through a specially designed die that creates a low-pressure curtain. This is achieved by optimizing the geometry of the die and controlling the flow rate of the coating material.
- Reduced impact force: As the low-pressure curtain falls onto the moving substrate, the impact force between the curtain and the substrate is significantly reduced compared to traditional curtain coating. This reduction in impact force minimizes the splashing and bouncing of the coating material, leading to less material waste.
- Uniform coating application: Despite the lower impact force, the LPI method still ensures a uniform and smooth coating layer on the substrate. The precise control over the curtain formation and the substrate speed allows for consistent coating thickness and quality.
Benefits of LPI Applying Method
- Reduced material loss: The low-pressure impact minimizes the amount of coating material that splashes or bounces off the substrate, resulting in less material waste.
- High-speed coating: LPI applying method maintains the high-speed coating capabilities of traditional curtain coating, enabling faster production rates.
- Improved coating quality: The reduced impact force leads to fewer defects and irregularities in the applied coating layer, resulting in improved overall coating quality.
- Cost-effective: The combination of reduced material loss and high-speed coating makes the LPI applying method a cost-effective solution for various industries.
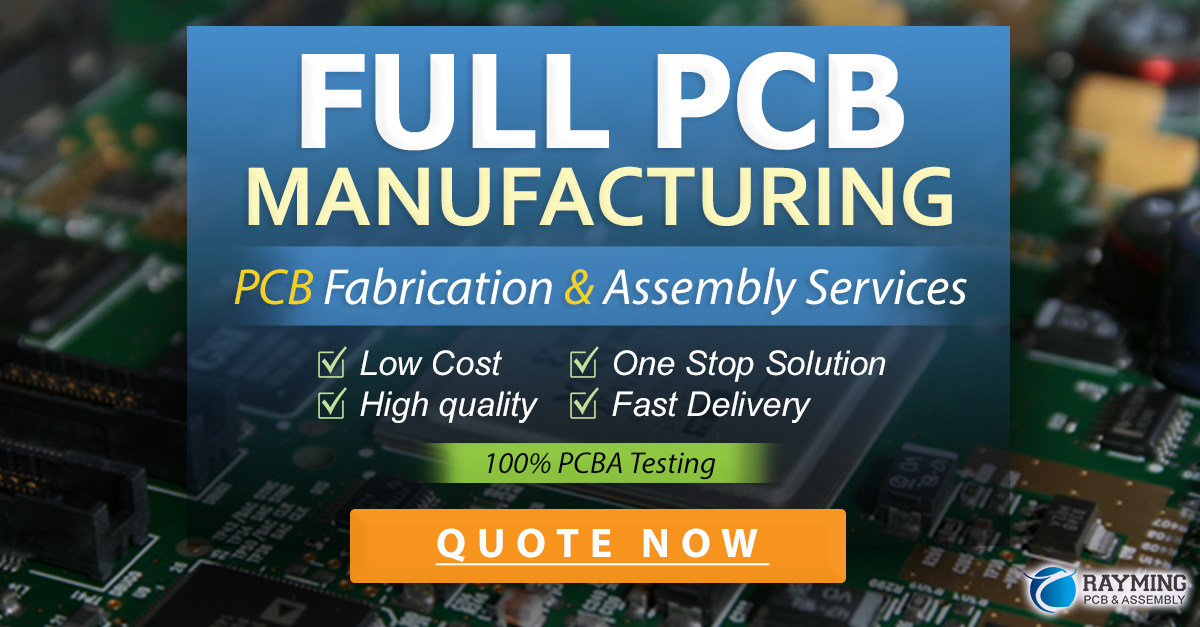
Applications of Curtain Coating with LPI Applying Method
Curtain coating with the LPI applying method finds applications in several industries, including:
- Photographic film and paper production
- Magnetic tape manufacturing
- Battery electrode coating
- Flexible electronic device fabrication
- Optical film coating
- Adhesive tape production
- Fuel cell membrane coating
In each of these applications, the LPI applying method enables high-speed, precise, and uniform coating while minimizing material waste, leading to improved production efficiency and cost savings.
Factors Affecting Curtain Coating Performance
Several factors influence the performance of curtain coating with the LPI applying method:
- Coating material properties: The viscosity, surface tension, and density of the coating material play a crucial role in the formation and stability of the curtain, as well as the quality of the applied coating layer.
- Die design: The geometry of the die, including the slot width, lip design, and flow channel shape, affects the curtain formation and the uniformity of the coating layer.
- Substrate properties: The surface energy, roughness, and wettability of the substrate influence the interaction between the coating material and the substrate, impacting the adhesion and uniformity of the applied layer.
- Process parameters: The flow rate of the coating material, the speed of the substrate, and the distance between the die and the substrate are critical process parameters that need to be optimized for each specific application.
Challenges and Solutions in Curtain Coating with LPI Applying Method
Despite its numerous advantages, curtain coating with the LPI applying method also presents some challenges:
- Curtain stability: Maintaining a stable curtain is essential for uniform coating. Factors such as air entrainment, surface waves, and edge effects can disrupt the curtain stability. Solutions include optimizing the die design, using flow modifiers, and implementing edge guides.
- Coating defects: Defects such as air bubbles, streaks, and non-uniform thickness can occur during the coating process. These issues can be addressed by proper material preparation, filtration, and process parameter optimization.
- Substrate handling: Ensuring proper substrate handling, including tension control and alignment, is crucial for achieving consistent coating quality. Implementing precise web handling systems and tension control mechanisms can help overcome this challenge.
Recent Advancements in Curtain Coating with LPI Applying Method
Continuous research and development efforts have led to several advancements in curtain coating with the LPI applying method:
- Multi-layer LPI coating: The development of multi-layer LPI coating systems allows for the simultaneous application of multiple layers with different materials, further enhancing production efficiency.
- Electrostatic assisted LPI coating: The incorporation of electrostatic forces in the LPI applying method helps improve the coating uniformity and reduces material waste by controlling the interaction between the coating material and the substrate.
- Ultrasonic-assisted LPI coating: The use of ultrasonic vibrations in the LPI applying method has been shown to enhance the curtain stability and reduce coating defects, resulting in improved coating quality.
Future Prospects of Curtain Coating with LPI Applying Method
As industries continue to demand higher production efficiency, better coating quality, and reduced material waste, curtain coating with the LPI applying method is expected to gain further prominence. Some of the future prospects include:
- Expansion into new application areas: The versatility of curtain coating with the LPI applying method makes it suitable for a wide range of industries, and it is expected to find new applications in emerging fields such as flexible electronics, advanced battery technologies, and sustainable packaging.
- Integration with other coating techniques: Combining curtain coating with the LPI applying method with other coating techniques, such as slot die coating or gravure coating, can lead to the development of hybrid coating systems that offer the benefits of multiple methods.
- Automation and process control: The increasing adoption of automation and advanced process control systems in curtain coating with the LPI applying method will further enhance the consistency, reliability, and efficiency of the coating process.
Frequently Asked Questions (FAQ)
-
What is the main difference between traditional curtain coating and the LPI applying method?
The main difference lies in the impact force between the coating curtain and the substrate. In the LPI applying method, the impact force is significantly reduced, leading to less material waste and improved coating quality. -
Can the LPI applying method be used for coating multiple layers simultaneously?
Yes, recent advancements in multi-layer LPI coating systems allow for the simultaneous application of multiple layers with different materials. -
What are the key factors that affect the performance of curtain coating with the LPI applying method?
The key factors include coating material properties, die design, substrate properties, and process parameters such as flow rate, substrate speed, and die-to-substrate distance. -
How does the LPI applying method help reduce material waste?
The low-pressure impact in the LPI applying method minimizes the amount of coating material that splashes or bounces off the substrate, resulting in less material waste compared to traditional curtain coating. -
What are some of the emerging applications for curtain coating with the LPI applying method?
Some of the emerging applications include flexible electronics, advanced battery technologies, and sustainable packaging, where the high-speed, precision, and low-waste characteristics of the LPI applying method are particularly beneficial.
Conclusion
Curtain coating with the Low Pressure Impact (LPI) applying method is a powerful technique that combines the benefits of high-speed coating, precise layer thickness control, and reduced material waste. By minimizing the impact force between the coating curtain and the substrate, the LPI applying method ensures uniform, high-quality coatings while significantly reducing material loss. As industries continue to prioritize efficiency, quality, and sustainability, curtain coating with the LPI applying method is poised to play an increasingly important role in various application areas. With ongoing research and development efforts focused on further enhancing its capabilities and expanding its use cases, this innovative coating technique is set to shape the future of coating processes across multiple sectors.
Leave a Reply