Why is Copper Distribution Important?
Copper distribution on a panel is critical for several reasons:
-
Electrical Conductivity: Copper is an excellent conductor of electricity, making it ideal for creating conductive paths on PCBs. Even distribution ensures that electrical signals can travel efficiently and reliably throughout the panel.
-
Heat Dissipation: Copper also has good thermal conductivity properties, which helps in dissipating heat generated by electronic components. Proper copper distribution aids in the efficient transfer of heat away from sensitive components, preventing overheating and potential damage.
-
Signal Integrity: Uneven copper distribution can lead to variations in electrical impedance, which can cause signal reflections, distortions, and crosstalk. By maintaining a consistent copper distribution, signal integrity is preserved, resulting in better overall performance.
-
Manufacturability: Even copper distribution is crucial for the successful manufacturing of PCBs. It ensures that the etching process, which removes unwanted copper to create the desired circuit patterns, is performed accurately and consistently across the panel.
Factors Affecting Copper Distribution
Several factors can influence the distribution of copper on a panel:
-
Panel Material: The type of substrate material used for the panel, such as FR-4, polyimide, or ceramic, can affect copper adhesion and distribution. Different materials have varying surface properties and thermal expansion coefficients, which can impact the uniformity of copper distribution.
-
Copper Thickness: The thickness of the copper layer can also play a role in distribution. Thicker copper layers may be more prone to uneven distribution due to variations in plating or lamination processes. Thin copper layers, on the other hand, may be more susceptible to defects and irregularities.
-
Manufacturing Process: The manufacturing process employed, such as electroplating, lamination, or sputtering, can significantly influence copper distribution. Each process has its own set of parameters and variables that need to be carefully controlled to achieve uniform distribution.
-
Panel Size and Geometry: The size and shape of the panel can affect copper distribution. Larger panels may be more challenging to maintain even distribution across the entire surface, while panels with complex geometries or irregular shapes can introduce additional challenges in achieving uniform distribution.
Methods for Achieving Optimal Copper Distribution
To ensure optimal copper distribution on a panel, several methods can be employed:
-
Electroplating: Electroplating is a common method for depositing copper onto a panel. By carefully controlling the plating parameters, such as current density, solution composition, and agitation, uniform copper distribution can be achieved. Techniques like pulse plating or reverse pulse plating can further enhance the uniformity of the copper layer.
-
Lamination: Lamination involves bonding copper foils to the substrate material under high pressure and temperature. Proper lamination process control, including maintaining consistent pressure, temperature, and dwell time, is essential for achieving even copper distribution. The use of high-quality copper foils with minimal thickness variations can also contribute to better distribution.
-
Surface Preparation: Adequate surface preparation of the substrate material prior to copper deposition is crucial. Cleaning, roughening, and chemical treatment of the surface can improve copper adhesion and promote uniform distribution. Techniques like plasma treatment or chemical etching can enhance the surface properties for better copper distribution.
-
Process Optimization: Optimizing the manufacturing process parameters is key to achieving optimal copper distribution. This involves fine-tuning variables such as plating current density, solution composition, temperature, and agitation rates. Design of Experiments (DOE) and statistical process control (SPC) techniques can be employed to identify the optimal process window for achieving uniform copper distribution.
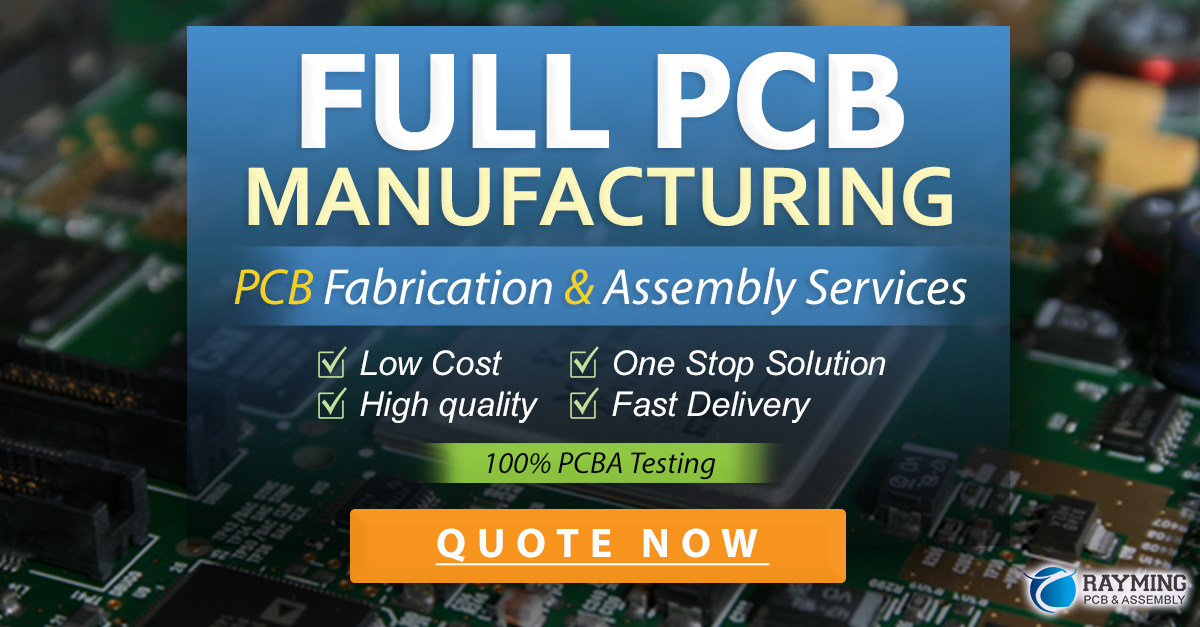
Quality Control Measures
To ensure that the copper distribution on a panel meets the desired specifications, several quality control measures can be implemented:
-
Visual Inspection: Visual inspection is a basic yet effective method for detecting obvious copper distribution issues. Trained operators can identify defects such as voids, blisters, or uneven coverage using magnification tools or automated optical inspection (AOI) systems.
-
Thickness Measurement: Measuring the copper thickness at various points on the panel can provide insights into the uniformity of distribution. Techniques like X-ray fluorescence (XRF) or beta backscatter can be used to non-destructively measure copper thickness across the panel.
-
Electrical Testing: Electrical testing methods, such as resistance measurements or impedance testing, can reveal variations in copper distribution. By measuring the electrical properties at different locations on the panel, any significant deviations can be identified and addressed.
-
Cross-Sectional Analysis: Cross-sectional analysis involves cutting a small section of the panel and examining it under a microscope. This destructive method allows for a detailed examination of the copper distribution, including layer thickness, adhesion, and any internal defects.
-
Statistical Process Control (SPC): Implementing SPC techniques can help monitor and control the copper distribution process over time. By collecting and analyzing data on key process parameters and quality metrics, any deviations or trends can be identified and corrective actions can be taken to maintain consistent copper distribution.
Frequently Asked Questions (FAQ)
-
What is the ideal copper thickness for a PCB panel?
The ideal copper thickness depends on the specific application and design requirements of the PCB. Common copper thicknesses range from 0.5 oz/ft² (18 µm) to 2 oz/ft² (70 µm), with 1 oz/ft² (35 µm) being a widely used standard. Thicker copper layers are used for high-current or high-power applications, while thinner layers are suitable for general-purpose PCBs. -
Can uneven copper distribution cause signal integrity issues?
Yes, uneven copper distribution can lead to signal integrity problems. Variations in copper thickness or distribution can cause impedance mismatches, leading to signal reflections, distortions, and crosstalk. These issues can degrade the performance of high-speed or high-frequency circuits, resulting in reduced signal quality and potential malfunctions. -
How can copper distribution be improved in the manufacturing process?
Copper distribution can be improved by optimizing the manufacturing process parameters. This includes carefully controlling the plating current density, solution composition, temperature, and agitation rates during electroplating. Proper surface preparation of the substrate, such as cleaning and roughening, can also enhance copper adhesion and distribution. Implementing statistical process control (SPC) techniques and regularly monitoring key process variables can help maintain consistent copper distribution over time. -
What are the challenges in achieving uniform copper distribution on large panels?
Achieving uniform copper distribution on large panels can be challenging due to several factors. Larger panels may experience variations in plating or lamination conditions across the surface, leading to uneven distribution. Maintaining consistent temperature, pressure, and chemical concentrations over a larger area can be more difficult. Additionally, handling and transportation of large panels can introduce stresses or deformations that affect copper distribution. Careful process control, specialized equipment, and proper handling procedures are essential for maintaining uniform distribution on large panels. -
How can copper distribution issues be detected and addressed?
Copper distribution issues can be detected through various quality control measures. Visual inspection using magnification tools or automated optical inspection (AOI) systems can identify surface defects or uneven coverage. Thickness measurements using techniques like X-ray fluorescence (XRF) or beta backscatter can reveal variations in copper thickness across the panel. Electrical testing methods, such as resistance measurements or impedance testing, can indicate any significant deviations in copper distribution. Cross-sectional analysis can provide a detailed examination of the internal copper distribution. If issues are detected, corrective actions, such as adjusting process parameters or implementing additional process controls, can be taken to address the problem and improve copper distribution uniformity.
Conclusion
Copper distribution on a panel is a critical factor in the manufacturing of electronic devices and PCBs. Even distribution of copper ensures proper electrical conductivity, heat dissipation, signal integrity, and manufacturability. Several factors, including panel material, copper thickness, manufacturing process, and panel size and geometry, can affect copper distribution. To achieve optimal distribution, methods such as electroplating, lamination, surface preparation, and process optimization can be employed. Quality control measures, including visual inspection, thickness measurement, electrical testing, cross-sectional analysis, and statistical process control, are essential for ensuring consistent and reliable copper distribution. By understanding the importance of copper distribution, implementing appropriate manufacturing techniques, and maintaining strict quality control, manufacturers can produce high-quality panels that meet the demanding requirements of modern electronic devices.
Copper Thickness | Typical Applications |
---|---|
0.5 oz/ft² (18 µm) | Low-power, high-density PCBs |
1 oz/ft² (35 µm) | General-purpose PCBs |
2 oz/ft² (70 µm) | High-current, high-power PCBs |
Table 1: Common copper thicknesses and their typical applications.
Quality Control Method | Purpose |
---|---|
Visual Inspection | Detect surface defects and uneven coverage |
Thickness Measurement | Measure copper thickness variations across the panel |
Electrical Testing | Identify deviations in electrical properties due to copper distribution |
Cross-Sectional Analysis | Examine internal copper distribution and layer characteristics |
Statistical Process Control | Monitor and control copper distribution process over time |
Table 2: Quality control methods for copper distribution on a panel.
By adhering to best practices in copper distribution and implementing robust quality control measures, manufacturers can ensure the production of reliable and high-performance electronic devices that meet the ever-increasing demands of the industry.
Leave a Reply