Introduction
Printed circuit boards (PCBs) made with ceramic substrates offer superior thermal and electrical performance compared to traditional FR4 boards. Ceramic PCBs can operate at higher temperatures, frequencies, and power levels without distortion. They also provide excellent heat dissipation and noise isolation.
For products requiring high reliability and precision, like aerospace systems, medical devices, and telecom infrastructure, ceramic PCBs are often the ideal solution. However, sourcing these boards can be challenging due to the specialized materials and manufacturing processes involved.
This guide will examine the key factors to consider when selecting a ceramic PCB manufacturer. We’ll look at capabilities, quality control standards, and technical expertise to help identify the right partner for your project.
Overview of Ceramic PCBs
Ceramic PCB substrates are made from inorganic, nonmetallic materials such as aluminum oxide or aluminum nitride. The ceramic formulation, known as the dielectric, has a high dielectric constant that allows efficient performance at high frequencies. Other properties like thermal conductivity and low thermal expansion also make ceramics suitable for high-power and high-temperature applications.
The most common ceramic PCB types are:
- Alumina (Al2O3) – Most widely used. Offers high strength and excellent electrical insulation. Used in RF, power, and high-temperature products.
- Aluminum nitride (AlN) – Very high thermal conductivity. Ideal for LEDs, power devices, and other heat-generating components.
- Glass ceramic – Combines properties of glass and ceramic materials. Low dielectric loss at high frequencies. Used in radar, communications, and avionics.
- LTCC (low-temperature co-fired ceramic) – Allows embedding passive components like resistors and capacitors within the PCB for miniaturization. Common in mobile and IoT products.
Benefits of Using a Ceramic PCB Manufacturer
While it is possible to produce ceramic PCBs in-house, the highly specialized nature of these boards makes outsourcing manufacturing attractive for many design teams. The key potential benefits of using a professional ceramic PCB manufacturer include:
Specialized Equipment and Staff – Ceramic PCB fabrication requires advanced processes like screen printing, lamination, co-firing, and laser cutting. High-quality ceramic materials can be challenging to source. This represents substantial capital investments that may not make sense for low-volume production. A dedicated manufacturer maintains the necessary equipment and expert staff.
Quality and Reliability – Reputable manufacturers have rigorous quality control standards tuned to the requirements of ceramic PCBs. This includes thorough incoming inspection of materials, process controls during fabrication, and 100% testing and inspection of finished boards. Their process expertise results in greater consistency and reliability.
Design Support – The manufacturer’s engineering team can provide valuable design review and recommendations to help customers avoid manufacturability issues. Their knowledge of ceramic PCB design rules and capabilities can optimize a design for performance and yield.
Prototyping Services – Developing a reliable fabrication process requires producing and evaluating multiple prototype revisions. Partnering with a manufacturer that offers low-volume prototyping can accelerate this process and reduce development costs.
Scalability – An established manufacturer has the infrastructure to scale up production efficiently. Once the fabrication process is proven out, they can manufacture pre-production builds and ramp up to higher volumes.
Key Capabilities to Look for in a Ceramic PCB Manufacturer
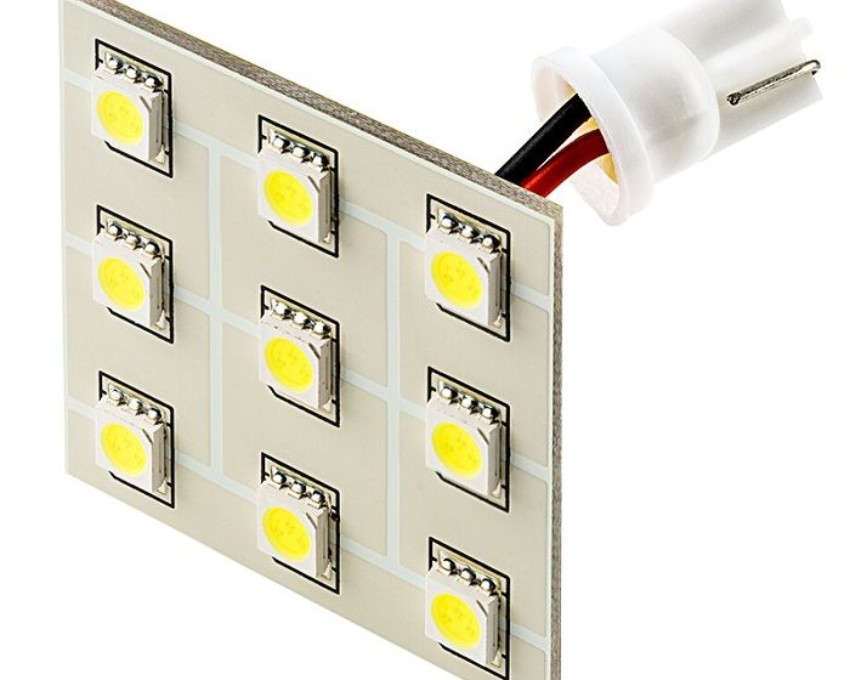
Choosing the right ceramic PCB manufacturer is critical for a successful product development and production ramp. Here are some key capabilities and qualifications to evaluate:
Substrate Options – At minimum, look for alumina and aluminum nitride. Variants like glass ceramic and LTCC provide additional flexibility. Having a range of dielectric materials ensures the manufacturer can support different application requirements.
Circuit Line Resolution – Fine lines and spaces under 5 mils allow for complex circuitry on ceramic boards. The manufacturer’s capabilities here determine the achievable routing density.
Number of Layers – Stacked ceramic PCBs with multiple internal layers are often required for complex designs. Look for capability to produce high layer counts of 10 or more layers.
Miniaturization – Many ceramic circuits push the boundaries of miniaturization. See if a manufacturer has experience with very small components, fine features, and advanced packaging techniques.
In-House vs Outsourced Steps – While some process steps may be outsourced, key steps like lamination, firing, and metallization should be done in-house to ensure quality control. Ask about their supply chain.
Secondary Operations – Routinely applied operations like vias, conformal coating, and precision machining should be available. These allow further optimization of the PCB performance and assembly.
Quality Certifications – Leading manufacturers comply with ISO 9001 or similar international quality standards. This demonstrates their commitment to consistency and process control.
Domestic vs Offshore Production – Both have pros and cons. Domestic facilities offer tighter supply chain control while offshore leverages labor efficiencies. Choose what fits your priorities.
The Importance of an Experienced Engineering Team
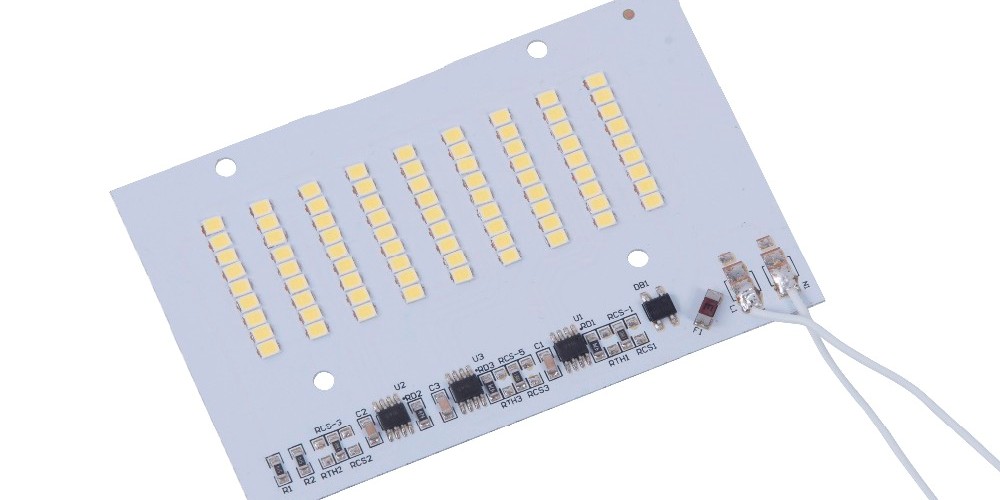
Beyond production capabilities, the engineering expertise at a ceramic PCB manufacturer is crucial for facilitating design reviews and assessing manufacturability. Key areas of experience to seek out include:
Ceramic Materials Knowledge – The engineers should have in-depth knowledge of ceramic substrate properties and behaviors. This allows them to recommend the most suitable dielectric material for an application based on technical requirements and design goals.
Design Rule Expertise – With the ability to identify potential issues early in the design cycle, engineers can provide feedback to improve manufacturability. Tight collaboration optimizes the design.
Prototyping Skills – The ability to build and analyze prototype boards quickly reveals opportunities for performance improvements and fabrication process refinements.
Failure Analysis Capabilities – Engineers can methodically diagnose the root cause when prototyping issues arise. This prevents repeating mistakes.
Assembly Process Experience – Understanding compatible assembly techniques, component attachments, thermal profiles, and other factors ensures a robust PCB design.
Continuous Improvement Mindset – Following industry advances and investigating new materials means the manufacturer can evolve capabilities over time and offer fresh solutions.
Questions to Ask Potential Ceramic PCB Manufacturers
Once you have narrowed down the list of candidate manufacturers, be sure to ask probing questions before selecting your partner:
- What ceramic materials do you have in-house processing for? What are the properties and typical applications for each?
- Can you share examples of complex ceramic PCBs you have produced, with details on line widths, layer counts, and other parameters?
- How is your ceramic fabrication equipment optimized for quality control and repeatability?
- How will your engineers collaborate with our team during design review and prototyping?
- What testing and inspection processes do you use to ensure quality? Are there any certifications that apply?
- What lead times can you commit to for prototyping and production runs? How do you ensure on-time delivery?
- Are there any unique technical challenges presented by our application? How would you overcome them?
- What support is available if our product requirements change mid-project? How quickly can new iterations be turned around?
- Do you have references from customers with similar needs to ours that we could speak to?
Getting candid answers to questions like these will provide the confidence that you are choosing the right ceramic PCB manufacturing partner.
Conclusion
Ceramic PCB technology enables exceptional performance for products serving high-value industries. While fabrication has higher costs and barriers to entry, partnering with an experienced ceramic PCB manufacturer makes adopting this technology much more feasible.
With their specialized equipment, quality systems, engineering expertise, and scalability, the right manufacturer will become an invaluable extension of your team. Do your due diligence to select a manufacturing partner that can deliver on quality, reliability, and responsiveness. The upfront effort to qualify manufacturers will pay off with smooth, successful execution of your ceramic PCB project.
Frequently Asked Questions
Here are some common questions about choosing a ceramic PCB manufacturer:
Q: How much more expensive are ceramic PCBs compared to standard FR4 boards?
A: Ceramic PCBs are typically 3-5x more expensive than FR4 boards. The specialized ceramic materials and fabrication processes involved contribute to the higher costs. However, for applications requiring exceptional thermal or electrical performance, the benefits justify the additional expense.
Q: What size ceramic PCBs can a manufacturer produce?
A: With commercial equipment, PCB sizes up to 18″ x 24″ can be produced, though precision and yield may drop off at the higher end. Miniaturized boards under 1″ x 1″ can also be challenging depending on line width/spacing capabilities. Discuss required board sizes with your manufacturer.
Q: Can passive components be embedded within a ceramic PCB?
A: Yes, LTCC (low temperature co-fired ceramic) technology allows passive components like resistors and capacitors to be screen printed and co-fired within the PCB layers. This enables further miniaturization.
Q: How long does it take to produce a prototype ceramic PCB batch?
A: With an optimized process, experienced manufacturers can deliver prototype boards in 1-2 weeks. However, for a new design, expect several prototype iterations over 2-3 months to develop the fabrication process.
Q: What types of testing are performed to ensure quality?
A: Standard tests include network analysis, dielectric breakdown voltage, insulation resistance, and visual/microscopic inspection. Environmental stress screening such as thermal shock and vibration can also be applied.
Leave a Reply