Introduction to Buried Vias
A via is a conductive hole that connects different layers in a printed circuit board (PCB). Vias provide vertical interconnections and enable traces to change layers and connect components and pads on different layers.
A buried via is a special type of via that is completely internal to the PCB board. Unlike typical through-hole vias that extend through all layers, buried vias are embedded between layers in the PCB stackup. They connect internal layers without being visible or accessible from the outer surfaces of the board.
Benefits of Using Buried Vias
Buried vias offer several advantages compared to through-hole vias:
- Save space on outer layers – No need for antipads on outer layers since buried vias have no openings. This saves space for routing traces.
- Improve signal integrity – Signals have a continuous reference plane connection through the buried via. This helps maintain a controlled impedance.
- Reduce EMI and noise – No stub is created so there is less unintended resonance. Keeping signals inside the board also reduces emissions.
- Enhance manufacturability – Buried vias are drilled before lamination so there are no concerns withaccuracy when drilling small via holes. Plating is also more reliable.
- Simplify probe testing – No need to probe through conformal coating or avoid buried vias during debugging. probecan make reliable contact with pad on outer layer.
- Achieve higher densities – Smaller vias, finer lines and spaces, and more routing channels are possible.
Where Buried Vias are Used
Here are some common applications where buried vias provide major advantages in PCB design:
1. High Speed Designs
In high speed digital, RF, and microwave circuits, buried vias maintain a continuous reference plane. This allows signals to propagate with controlled impedance through the via transition. A buried via avoids stub resonance effects and unintended emissions.
2. Mixed Signal Circuits
For sensitive analog and mixed signal designs, it is critical to isolate digital and analog signals. Buried vias encapsulate signals inside the board stackup which helps reduce crosstalk between circuits.
3. HDI Boards
In HDI (high density interconnect) boards with many layers (>10) and microvias (<0.15mm diameter), buried vias help connect between sub-layers where multiple very small vias would be needed otherwise.
4. Complex Power Buses
Buried vias can create dedicated power planes and efficient power bus routing between layers without using outer layer space.
5. EMI Shielding
Sensitive circuits can be shielded by using buried vias to create vertical isolating barriers between sections of a board. Buried via fences stop noise coupling.
Design Guidelines for Buried Vias
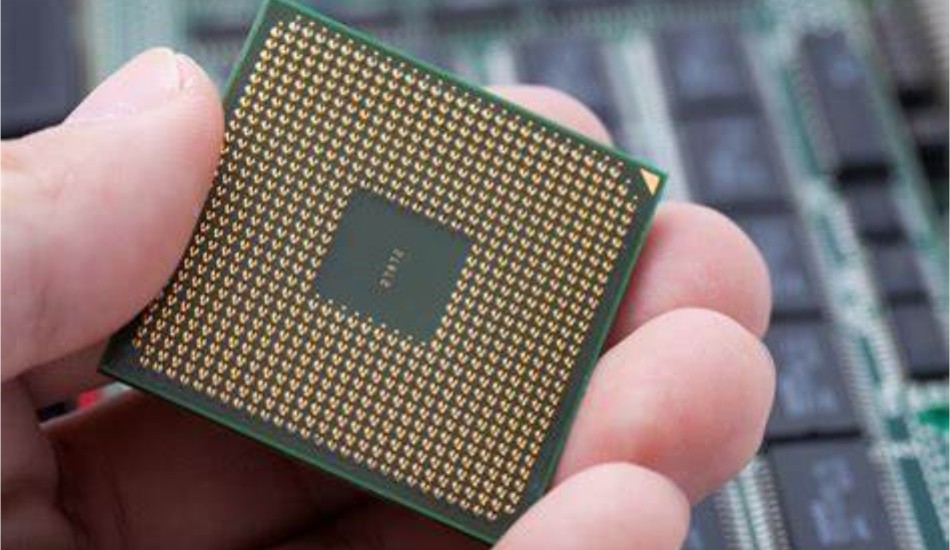
Here are some key considerations when working with buried vias in your PCB layout:
Layer Transitions
Plan layer transitions carefully around buried vias. Ensure reference planes are uninterrupted to maintain controlled impedance. Avoid plane gaps near vias.
Anti-pad Size
Use larger anti-pads than for through hole vias for better solder mask adhesion. Recommended to be 1.2 times via diameter or greater.
Minimum Annular Ring
Annular ring should be ≥ 0.15mm for reliable plating. Thin rings < 0.1mm can cause cracking.
Via-in-Pad
For vias in pads, make sure annular ring extends fully beyond pad to avoid openings.
Spacing and Density
Maintain at least 2X the via diameter spacing between buried vias for reliable plating. Higher densities increase risk.
Registration
For small vias, have ≥ 0.15mm tolerance between layers for registration to avoid openings from misalignment.
Thermal Relief Pads
Use thermal relief connections for buried vias connecting to large power pads to avoid delamination from heat.
Fill and Capping
Plugged, filled or capped buried vias can help reduce outgassing and enhance reliability.
Manufacturing Buried Vias
Fabricating boards with buried vias requires advanced PCB manufacturing capabilities. Here are some key aspects of buried via production:
Layer Stack Planning
The board layer stackup must be planned from the start to include all the buried via barrel layers where needed. High layer count designs are required.
Blind Via Drilling
Buried vias are laser drilled into each core layer using a blind via process before they are laminated together. Accuracy is critical.
Plated Through Holes
Buried vias act as plated through holes between the layers they interconnect. Reliable copper plating of the via holes is essential.
Layer Alignment and Registration
Layers must be precisely aligned during lamination to ensure the buried via holes in each layer are stacked correctly.
Surface Finish
An immersion silver, ENIG or other finish should be used to protect buried vias from oxidation between layers after drilling.
Fill and Plugging
Filling vias with epoxy or using plated plugged vias enhances reliability by preventing barrel cracking.
Via Reliability Testing
Extensive sectioning, microsectioning and voiding analysis should be done to qualify buried via processes.
Impact of Buried Vias on Routing
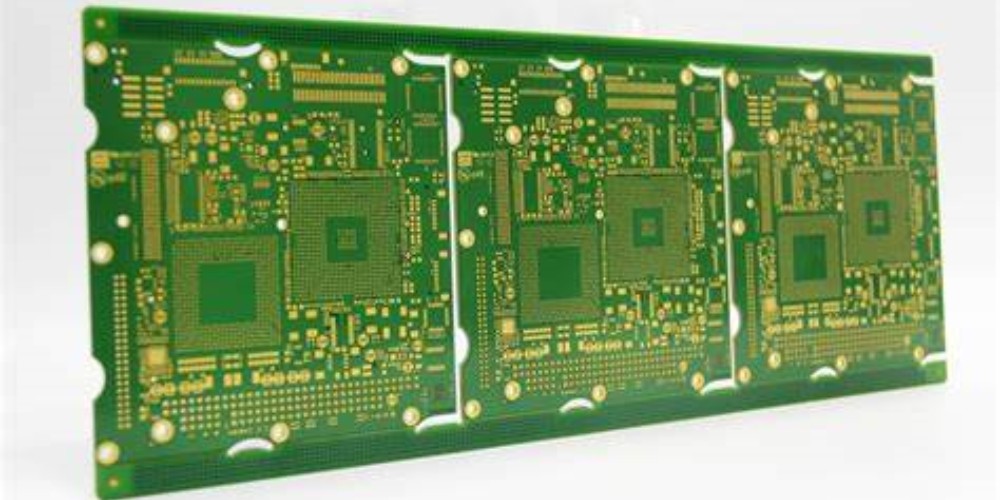
Using buried vias in a design requires adapting routing strategies:
- Plan all layer transitions around buried vias in advance during schematic capture.
- Ensure reference planes are uninterrupted. Avoid stubs.
- Watch for acid traps where chemicals can be trapped inside buried vias after plating.
- Create clearance rules for minimum spacing between buried vias.
- Set larger anti-pads sizes for buried vias vs through vias.
- Adjust design rules for thicker boards that can warp and create separation between buried via barrels.
- Plan for higher layer counts required to incorporate buried via connections.
- Use blind and buried vias strategically to optimize routing density.
Modeling and Simulating Buried Vias
Modern PCB design tools allow buried vias to be accurately modeled and simulated:
Via Physics
The via barrel shape, diameter, hole wall angle, and soldermask expansion can all be configured.
Layer Transitions
The precise layer transition can be modeled, showing reference planes routing through smoothly.
Lumped Element Models
Equivalent lumped circuit elements can model characteristics like inductance, capacitance and resistance.
Parameter Extraction
Measurements and calibration data can extract parameters to precisely match buried via performance.
EM Simulation
Full wave 3D electromagnetic simulation can predict buried via behavior and performance.
Signal Integrity
Signal waveform response through buried via transitions can be simulated to ensure quality.
Power Integrity
Power supply noise and decoupling effectiveness through buried vias is simulated.
Comparison of Blind, Buried and Through-Hole Vias
Via Type | Description | Key Attributes |
---|---|---|
Blind Via | Connects only between adjacent layers | – Requires fewer layers <br> – Lower cost process |
Buried Via | Connects between internal layers | – Limited pad/trace space <br> – No stub for controlled impedance <br> – Contained entirely inside board |
Through-Hole Via | Goes through entire board | – Lowest cost process <br> – Requires pads/antipads on each layer <br> – Can create stubs |
When to Avoid Buried Vias
Despite their advantages, there are some scenarios where buried vias should be avoided:
- Extremely high density designs – Plating reliability concerns
- Low layer count boards – Added costs may not justify use
- Large grid array packages – Difficult to route out internally
- Flexible or dynamic bend circuits – Can crack due to movement
- Low volume/prototype boards – Through hole vias cheaper
- RF boards above 5GHz – Performance consistency harder to control
- Thermally challenging designs – Expansion differences can cause reliability risks
- Test and debugging – Troubleshooting is more difficult
Conclusion
With advances in PCB technology, buried vias have become an essential tool in a designers toolbox. When used appropriately, buried vias enable improved routing density, signal integrity, and manufacturability. However, designers must also account for the impedance, thermal, and reliability impacts of incorporating buried vias in their boards. Following the guidance outlined here will allow you to effectively leverage buried vias while avoiding the pitfalls.
FAQ
What is the key benefit of a buried via?
The main advantage of buried vias is that they encapsulate signals inside the PCB stackup. This contains noise and eliminates stubs that affect signal quality.
Can I place components on top of buried vias?
It is generally not recommended to place surface mount pads and components directly over buried vias. The lack of air gap can make soldering unreliable. Clearance is needed.
How small can buried via diameters be made?
With advanced PCB processes, buried via diameters can be as small as 0.15mm (6mil). However, below 0.2mm reliability concerns increase substantially.
Do buried vias affect the thermal performance of PCBs?
Buried vias can lead to localized hot spots if they conduct heat away from power planes or components. Thermal modeling should account for buried vias.
How many extra layers do buried vias require?
It depends on the design, but typically buried vias require at least 4-6 additional board layers compared to a design using only through hole vias.
Leave a Reply