Introduction
High density interconnect (HDI) printed circuit boards (PCBs) have become increasingly popular in recent years due to the growing demand for smaller and more powerful electronic devices. HDI PCBs allow for tighter component spacing, more layers, finer lines and spaces, and buried and blind vias compared to conventional PCBs. While the most common HDI boards utilize traditional rigid FR-4 and polyimide materials, a variety of non-conventional materials are also being used to fabricate HDI boards with enhanced properties. This article will examine some of the non-traditional materials being used for HDI PCBs and the benefits they can provide.
Flexible HDI Boards
One growing application for non-conventional HDI boards is in flexible PCBs. Flexible circuits allow for dynamic flexing, bending, folding, and twisting which enables designs and form factors not possible with rigid boards. Some of the materials used for flexible HDI boards include:
Polyimide Films
Polyimide films like Kapton provide an excellent flexible dielectric material for HDI boards. Polyimide has high thermal stability and chemical resistance while maintaining good mechanical toughness and flexibility. Flexible polyimide HDI boards are well-suited for dynamic flexing applications like wearable devices.
LCP Films
Liquid crystal polymer (LCP) films have emerged as another option for flexible HDI boards. LCP has very low moisture absorption and excellent chemical resistance. It also has a low coefficient of thermal expansion (CTE), allowing it to match well with common copper conductors. LCP enables finer lines and spaces versus polyimide films.
Rigid-Flex HDI Boards
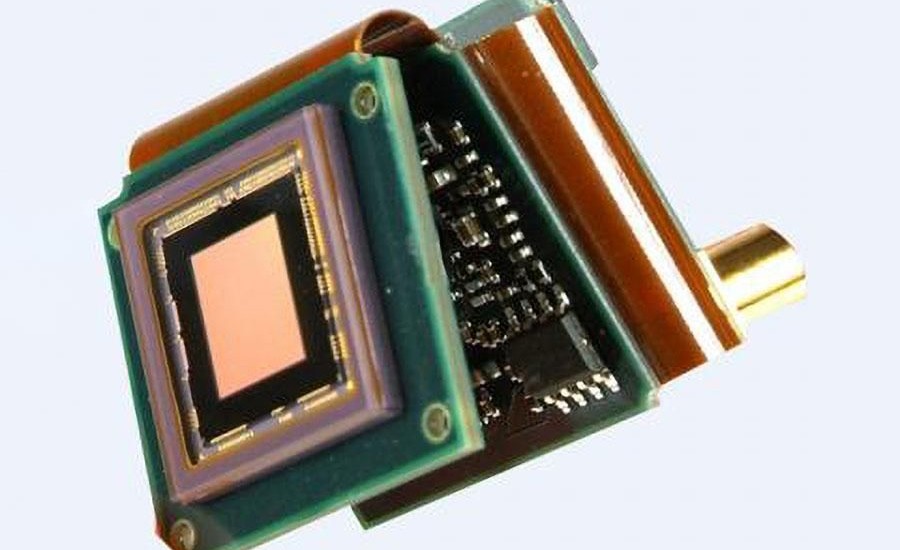
Rigid-flex PCBs incorporate both rigid and flexible substrates into a single circuit board. They allow integration of high component density rigid sections with dynamic flexible sections in one interconnected design. Some rigid-flex materials combinations include:
FR-4 and Polyimide
A common rigid-flex HDI board material set is FR-4 for the rigid sections and polyimide for the flex sections. FR-4 provides affordability and manufacturability for the rigid portions, while the polyimide flex areas enable bending and folding in compact mechanisms.
Ceramic and Polyimide
For more demanding applications, ceramic substrates like aluminum oxide or aluminum nitride can replace the FR-4 in rigid-flex boards. The ceramic rigid sections offer higher thermal conductivity and dimensional stability while the polyimide flex sections still accommodate dynamic bending.
LCP and LCP
All LCP rigid-flex boards are also feasible. This configuration provides excellent stability and chemical resistance across both rigid and flex areas of the HDI board.
Metal Core HDI Boards
Metal core PCBs contain a thick metal layer (usually aluminum or copper) to provide enhanced thermal conductivity and mechanical rigidity. The metal core layer allows routing of heat through the board and into chassis or heat sinks. This helps dissipate heat from high power components. Metal core HDI technology can accommodate finer lines and spaces than conventional metal core PCBs. Common material sets include:
Aluminum core with prepreg dielectric
Aluminum provides an economical metal core option. Aluminum core HDI boards manage thermal and mechanical demands at lower costs than some other metal core options.
Copper core with polyimide dielectric
Copper core HDI boards offer even better thermal conductivity than aluminum versions. This further aids heat dissipation in high power circuits. The polyimide dielectric provides high temperature and chemical stability.
Copper core with ceramic dielectric
For extreme environments, a copper core with ceramic dielectric like aluminum nitride or silicon nitrate can be used. The ceramic dielectric allows operation at over 300°C. This supports demanding applications like downhole drilling.
Ceramic HDI Boards
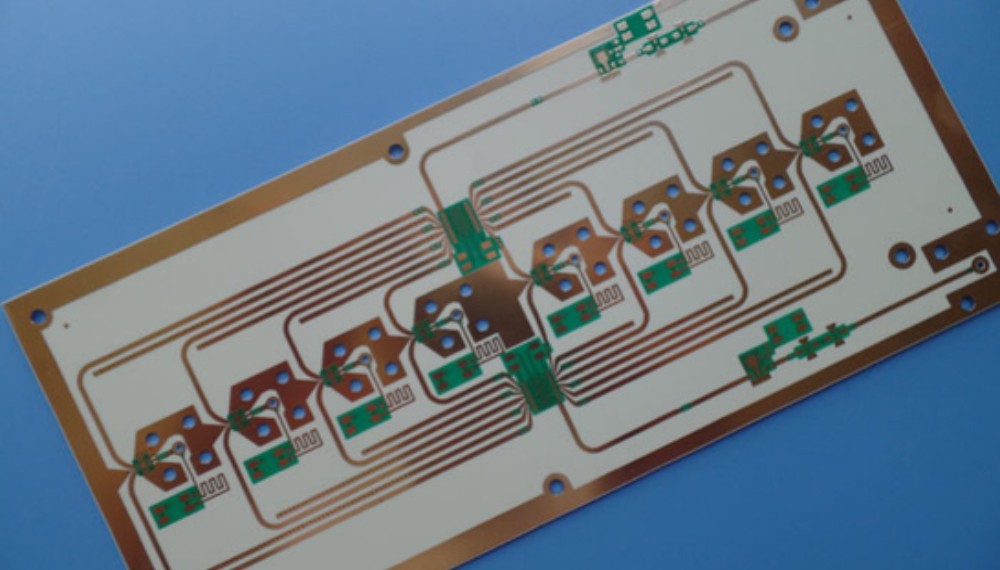
Ceramic materials like aluminum oxide and aluminum nitride can also be used to fabricate ceramic HDI boards without any metal core layer. The ceramic substrate provides electrical insulation even at very high temperatures and excellent thermal conductivity to dissipate localized heat generation. Ceramic HDI boards are well-suited to extreme environment electronics.
Glass Reinforced HDI Boards
Fiberglass reinforced plastic laminates, traditionally used in conventional PCBs, are also being adapted for HDI boards. The fiberglass cloth reinforcement increases mechanical strength and dimensional stability. It also improves thermal conductivity relative to standard FR-4 laminate. These attributes help support finer lines and spaces in higher layer count designs. Some glass reinforced options for HDI include:
FR-4 with extra fiberglass
High glass transition temperature (Tg) FR-4 prepregs with additional fiberglass content to increase thermal conductivity and strength. This cost-effective option improves certain attributes relative to standard FR-4.
BT (Bismaleimide Triazine) resin
BT resin systems have higher Tg than FR-4 for improved thermal and mechanical performance. BT prepregs reinforced with extra fiberglass provide a robust HDI board solution.
Thermoset polyimide prepregs
Fiberglass reinforced thermoset polyimide prepregs offer the highest thermal capability and dimensional stability of the glass reinforced options. This supports advanced HDI layer counts and densities.
Summary of Key Benefits
To summarize, some of the key potential benefits of utilizing non-conventional materials for HDI PCBs include:
Material Type | Key Benefits |
---|---|
Flexible (polyimide, LCP films) | – Dynamic/repeated flexing and bending<br>- Tight bend radii<br>-Wearable and compact mechanisms |
Rigid-Flex | – Integration of high density rigid and flexible in one board<br>-Complex compact folding/mechanisms |
Metal Core | -Enhanced thermal conductivity<br>-Heat dissipation from high power components |
Ceramic | -High temperature operation (>300°C)<br>-Excellent electrical insulation <br>-Thermal management |
Glass Reinforced | -Improved thermal conductivity vs. FR-4<br>-Increased strength and rigidity<br>-Dimensional stability |
Conclusion
There is growing interest in utilizing non-traditional materials beyond standard FR-4 to construct HDI printed circuit boards. These material technologies offer enhanced properties like flexibility, thermal conductivity, and high temperature operation that support HDI board integration into demanding new applications. As HDI manufacturing processes continue improving, adoption of novel materials for non-conventional HDI boards will further increase. This will support ongoing miniaturization and innovation in next generation electronics.
Frequently Asked Questions
Q: What are some key advantages of flexible HDI boards versus rigid boards?
A: Flexible HDI boards provide capabilities like dynamic flexing, tight bend radii, and conformability to non-flat surfaces that are impossible with rigid boards. This enables unique applications in wearable devices, compact mechanisms, robotics, and other areas.
Q: When are rigid-flex HDI boards preferred over boards that are all rigid or all flex?
A: Rigid-flex HDI boards are ideal when a design requires the integration of dense, high component area rigid sections with dynamic flexing sections in a single integrated assembly. This allows for more compact and complex products.
Q: For metal core HDI boards, why are copper cores generally better than aluminum cores?
A: Copper has approximately double the thermal conductivity of aluminum, making it superior for heat dissipation in high power circuits. This allows copper core HDI boards to manage localized hot spots more effectively.
Q: What are some examples of extreme environment applications where ceramic HDI boards are used?
A: Ceramic HDI boards are well-suited for downhole drilling electronics, aerospace engines, space satellite systems, high temperature process monitoring, and other very demanding high temperature or caustic chemical environments.
Q: When are glass reinforced HDI boards a good choice versus standard FR-4 HDI boards?
A: Glass reinforced HDI boards provide higher thermal conductivity, strength, and dimensional stability compared to FR-4. They are a good choice when these attributes enable higher densities and layer counts than possible with FR-4.
Leave a Reply