What is Soldermask and Why is Blue Soldermask Popular?
Soldermask, also known as solder resist or solder mask, is a thin lacquer-like layer of polymer applied to the copper traces of a printed circuit board (PCB). Its primary purpose is to prevent solder from bridging between conductors, thereby preventing short circuits. Soldermask also provides protection from oxidation and contamination, improving the durability and longevity of the PCB.
While green is the most common color for soldermask, blue soldermask has gained popularity in recent years due to its distinct appearance and improved visibility. The vibrant blue color makes it easier for technicians to distinguish between different components and traces on the PCB, reducing the likelihood of assembly errors.
Advantages of Blue Soldermask
Feature | Benefit |
---|---|
High Contrast | Easier to distinguish components and traces |
Improved Visibility | Reduces assembly errors |
Aesthetic Appeal | Visually striking and professional appearance |
Durability | Protects PCB from oxidation and contamination |
How Blue Soldermask Enhances PCB Assembly
The assembly process of printed circuit boards involves placing and soldering numerous tiny components onto the board. With the increasing complexity of modern electronics, PCBs often feature high-density layouts with closely spaced components and traces. In such cases, the use of blue soldermask can significantly enhance the assembly process by improving the visibility of the PCB features.
Improved Contrast and Visibility
Blue soldermask provides a high contrast background against the copper traces, component pads, and silkscreen markings on the PCB. This enhanced contrast makes it easier for assembly technicians to identify and place components accurately, even in low-light conditions or when working with small-scale PCBs.
The improved visibility offered by blue soldermask is particularly beneficial in the following scenarios:
- High-density PCB layouts
- Miniaturized components (e.g., 0201 resistors, BGA packages)
- Manual assembly processes
- Quality control and inspection
Reduced Assembly Errors
By enhancing the visibility of PCB features, blue soldermask helps minimize assembly errors such as:
- Component misplacement
- Incorrect component orientation
- Solder bridging
- Insufficient solder joints
Reducing these errors not only improves the overall quality of the assembled PCB but also saves time and resources by minimizing rework and debugging efforts.
Choosing the Right Soldermask Color
While blue soldermask offers several advantages, it may not be the best choice for every PCB design. When deciding on the soldermask color, consider the following factors:
Application Requirements
Some applications may have specific requirements for soldermask color. For example:
- Military and aerospace applications often require green soldermask to comply with industry standards
- Medical devices may prefer white soldermask for its clean and sterile appearance
- Consumer electronics may opt for black soldermask to create a sleek and modern look
Silkscreen Legibility
The soldermask color should provide sufficient contrast against the silkscreen markings on the PCB. If the silkscreen is white, blue soldermask offers excellent legibility. However, if the silkscreen is a different color, such as yellow or red, other soldermask colors may be more suitable.
Corporate Branding
In some cases, the choice of soldermask color may be influenced by corporate branding guidelines. Companies may prefer to use soldermask colors that align with their brand identity or product aesthetics.
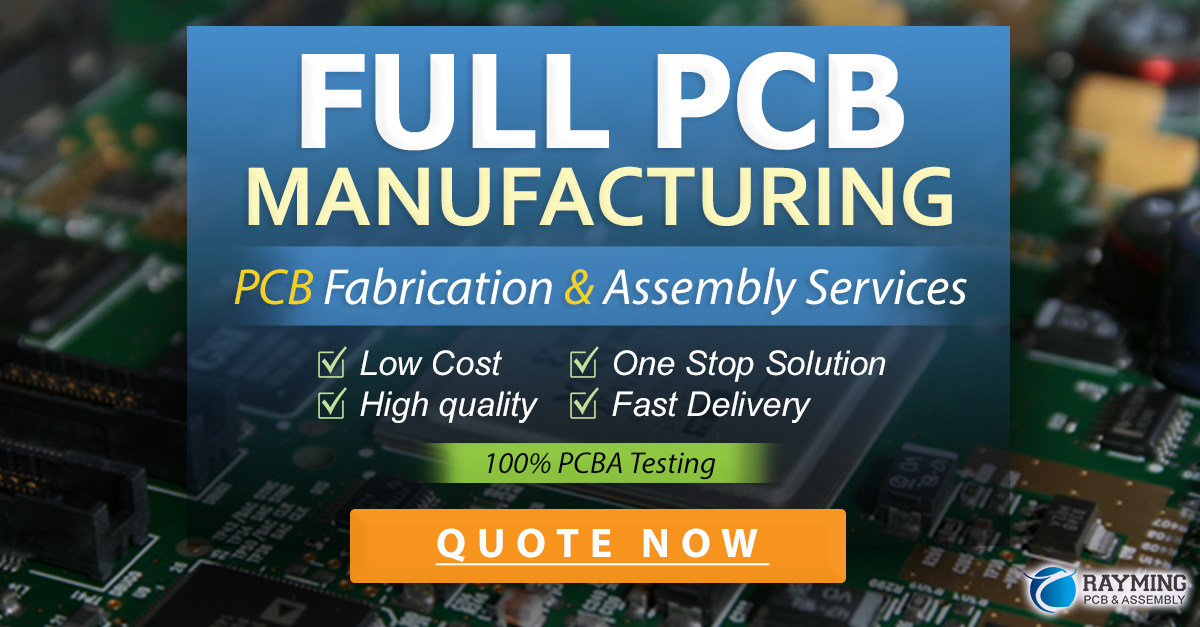
Soldermask Application Process
The application of soldermask involves several steps to ensure a uniform and reliable coating on the PCB surface. The process typically includes:
-
Surface Preparation: The PCB surface is cleaned to remove any contaminants or oxidation that may affect the adhesion of the soldermask.
-
Soldermask Application: The liquid soldermask is applied to the PCB surface using various methods, such as screen printing, spraying, or curtain coating. The method chosen depends on the PCB design, soldermask properties, and production volume.
-
Pre-drying: The coated PCB is pre-dried to remove the solvents from the soldermask and prevent any bubbling or blistering during the curing process.
-
Exposure: The soldermask is exposed to UV light through a photomask or direct imaging process. This step selectively polymerizes the soldermask in the desired areas, making it resistant to the subsequent developing process.
-
Developing: The unexposed areas of the soldermask are removed using a developing solution, revealing the copper pads and traces that will be soldered.
-
Curing: The PCB is heated to fully cure the soldermask, ensuring its durability and adhesion to the PCB surface.
Soldermask Thickness and Coverage
The thickness of the soldermask layer typically ranges from 0.8 to 1.2 mils (20 to 30 μm). A thicker soldermask provides better insulation and protection but may affect the fine-pitch soldering of small components. The soldermask coverage should be uniform across the PCB surface, with no pinholes, bubbles, or voids that may compromise its protective properties.
Choosing a High-Quality Blue Soldermask
When selecting a blue soldermask for your PCB, consider the following factors to ensure the best performance and reliability:
-
Material Properties: Choose a soldermask material that offers excellent adhesion, chemical resistance, and thermal stability. The material should also have good flow and leveling characteristics to ensure a smooth and uniform coating.
-
Color Consistency: Ensure that the blue soldermask has consistent color across different production batches. Inconsistent color may affect the visual appearance and make it difficult to distinguish between different PCB versions.
-
Compatibility: Verify that the blue soldermask is compatible with the PCB substrate material, copper foil type, and surface finish. Incompatible materials may lead to poor adhesion or delamination of the soldermask.
-
Manufacturer Reputation: Select a reputable PCB manufacturer with experience in applying blue soldermask. A reliable manufacturer will have strict quality control processes to ensure the consistency and reliability of the soldermask application.
Frequently Asked Questions (FAQ)
1. Can blue soldermask be used for all PCB applications?
While blue soldermask offers several advantages, it may not be suitable for all applications. Some industries, such as military and aerospace, may have specific requirements for soldermask color. Always consider the application requirements, silkscreen legibility, and corporate branding when choosing a soldermask color.
2. Is blue soldermask more expensive than other colors?
The cost of blue soldermask is generally similar to other standard soldermask colors, such as green or red. However, the exact pricing may vary depending on the PCB manufacturer, material supplier, and order quantity.
3. Does blue soldermask affect the electrical properties of the PCB?
The color of the soldermask does not directly affect the electrical properties of the PCB. However, the soldermask material and thickness can influence the insulation resistance, dielectric strength, and impedance control of the PCB traces.
4. Can blue soldermask be used with different surface finishes?
Yes, blue soldermask is compatible with various surface finishes, such as HASL, ENIG, and OSP. However, it is essential to verify the compatibility of the specific soldermask material with the chosen surface finish to ensure proper adhesion and performance.
5. How does blue soldermask compare to other high-visibility colors, such as white or yellow?
Blue soldermask offers a good balance between visibility and aesthetics. While white and yellow soldermasks provide high contrast, they may not be as visually appealing or may not align with corporate branding requirements. Additionally, white soldermask may show dirt and stains more easily, requiring more frequent cleaning.
Conclusion
Blue soldermask has gained popularity in the PCB industry due to its ability to enhance the visibility of PCB features, reducing assembly errors and improving the overall quality of the assembled board. By providing high contrast against copper traces and components, blue soldermask makes it easier for technicians to distinguish between different elements on the PCB, even in high-density layouts or miniaturized designs.
When considering blue soldermask for your PCB, evaluate the application requirements, silkscreen legibility, and corporate branding guidelines to ensure it is the best choice for your project. Choose a high-quality blue soldermask material from a reputable PCB manufacturer to guarantee consistent color, excellent adhesion, and reliable performance.
As PCB designs continue to push the boundaries of miniaturization and complexity, the use of blue soldermask will likely become increasingly popular, offering a visually striking and functional solution for improved PCB assembly and quality control.
Leave a Reply