Introduction
Printed circuit boards (PCBs) have become an essential component in electronics and technology products. Traditionally made from rigid fiberglass, PCBs are increasingly utilizing metal core materials like aluminum for advanced applications.
Aluminum PCBs provide several advantages over standard glass fiber PCBs:
- Excellent thermal conductivity
- Lightweight and thin profile
- Ideal for high power and high frequency designs
- More durable and rigid
This guide will explore aluminum PCB manufacturing in detail – from properties and benefits to leading manufacturers capable of producing these boards. We’ll also answer common questions about aluminum PCB sourcing and applications.
Benefits of Aluminum PCBs
Aluminum is an ideal material for PCB substrates due to the following inherent properties:
Thermal Management
Aluminum has excellent thermal conductivity, allowing it to dissipate heat efficiently from high power components and designs. This helps prevent overheating and component failure.
Lightweight
Aluminum is a lightweight metal, resulting in thinner and lighter PCBs compared to traditional glass fabric boards. This enables more compact product designs.
High Frequency Performance
The metal construction provides superior high frequency performance critical for RF microwave and other applications up to 77GHz.
Rigid and Durable
Aluminum is physically strong and rigid, providing excellent mechanical support for PCBs in demanding environments. The PCBs resist warping and fracturing better.
Cost Effective
Once designed and tooled, aluminum PCBs can be very cost effective compared to exotic substrate materials for specialized applications.
For these reasons, aluminum PCBs are being increasingly used for powerful LED lighting, electric vehicle systems, industrial equipment, and consumer electronics.
Aluminum PCB Manufacturing Process
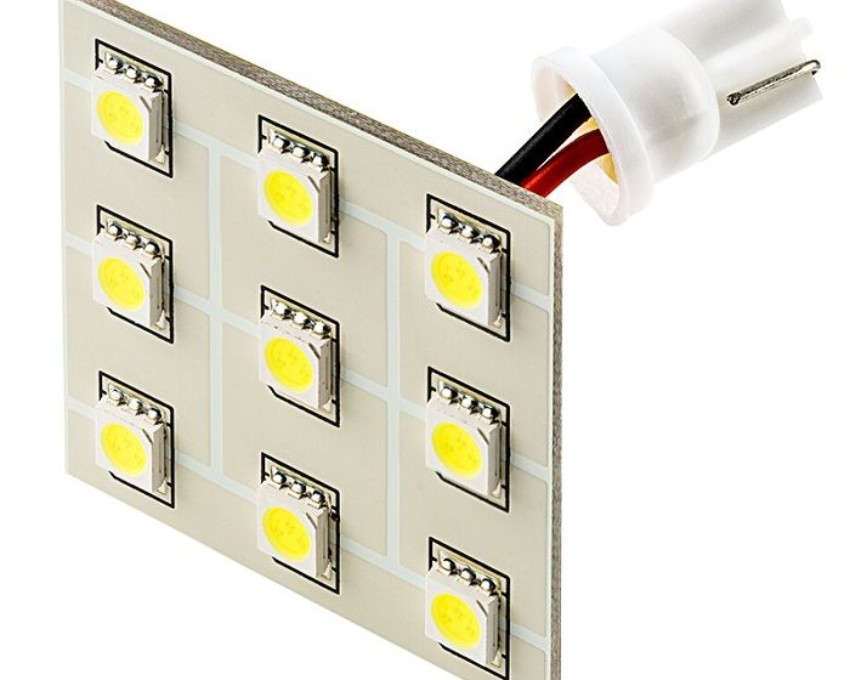
Aluminum PCBs follow a fabrication process similar to conventional glass epoxy PCBs, with some additional steps:
Base Material
The raw aluminum for PCB substrates is available in various alloy grades and thicknesses. Popular options include 6061 and 5052 alloys. The thickness depends on rigidity and weight requirements but is typically 0.8mm to 3mm.
Surface Treatment
The aluminum surface needs treatments and preparations to improve adhesion with laminated copper layers. Common surface finishes used are chromate conversion coating and abrasive blasting.
Lamination
Layers of copper foil are laminated to the aluminum core using adhesive films and high pressure rollers. Proper adhesion prevents delamination during use.
Imaging and Etching
The PCB design pattern is imaged on the copper layers using photoresists and then chemically etched to form the conductive traces.
Hole Drilling
Holes are drilled through the board using CNC machines for installing electronic components. The holes are then plated with copper.
Solder Mask and Silkscreen
A solder mask layer insulates the copper traces. Silkscreen provides markings like component designators.
Testing and Certification
Finished boards are electrically and mechanically tested. IPC certifications validate quality standards.
Panelization
Boards are laid out on large panels for mass production. The panels are then separated into individual PCBs.
With expertise in working with metals, experienced aluminum PCB manufacturers follow optimized fabrication techniques.
Leading Aluminum PCB Manufacturers
Many PCB manufacturers globally now offer aluminum PCB services to meet growing demand:
Advanced Circuits
Based in Colorado, Advanced Circuits is a leading North American PCB producer with over 25 years of experience. They manufacture a wide range of aluminum PCBs.
Bay Area Circuits
Bay Area Circuits, located in California, provides quick turn aluminum PCB prototypes and production. They also produce metal core FR4 boards.
Epec
Epec has specialized in aluminum PCBs for over 30 years. Their expertise covers thermal clad, plated through hole, and multilayer aluminum boards.
Sunstone Circuits
Sunstone offers aluminum PCBs in various base metal thicknesses. They also provide an aluminum solder mask finish.
Taiyo Industrial
Taiyo is a Japanese manufacturer skilled in multilayer aluminum boards for high power LEDs and power electronics.
NCAB Group
Global PCB producer NCAB offers aluminum PCBs starting at low volumes, supporting prototyping needs.
Ventec
Known for their tec-thermal board materials, Ventec provides cost-effective aluminum core PCB solutions.
This list highlights some reliable manufacturers capable of producing aluminum PCBs, from prototypes to volume production. Working with an experienced partner is key to getting high quality aluminum boards.
Aluminum vs FR4 PCBs
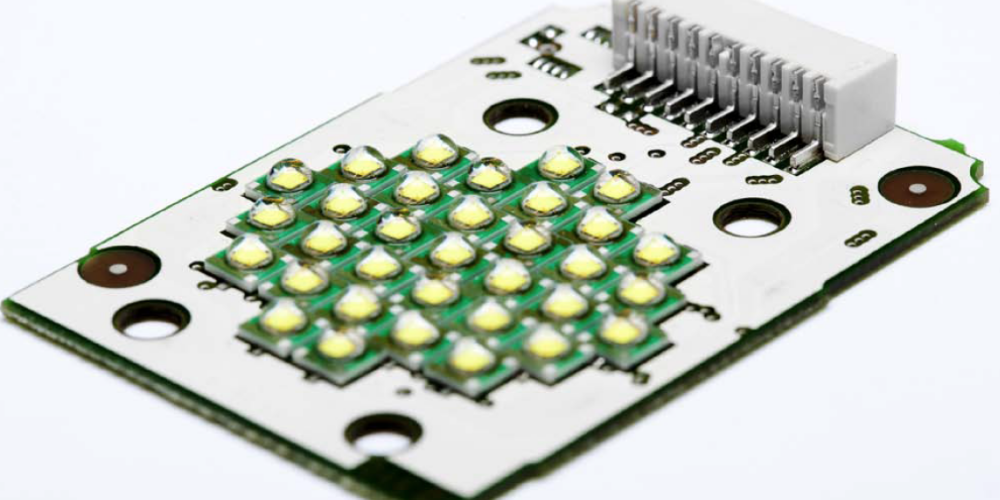
Aluminum PCBs have pros and cons compared to standard FR4 fiberglass boards:
Aluminum PCB Advantages
- Better thermal conductivity and heat dissipation
- Lightweight and thinner profile possible
- More rigid and durable
- Excellent high frequency characteristics
FR4 PCB Advantages
- Generally lower cost
- Easier to solder components
- Established and well proven technology
- Supports very fine trace geometries
Aluminum PCBs are preferred when thermal and mechanical performance along with high frequencies are critical. They can justify the higher cost with long term reliability and capabilities. FR4 remains ideal for more cost sensitive, lower performance applications.
Aluminum PCB Design Considerations
Designing aluminum PCBs requires some considerations:
- Thermal management must be modeled to avoid hotspots
- Careful floorplanning to account for thermal expansion
- Warpage control for cooling after lamination
- Minimizing CTE mismatch between components and aluminum PCB
- Allowing for thermal vias and ground plane layers
- Specifying suitable surface finishes and soldermasks
- Defining proper layout rules and tolerances
Working closely with the board manufacturer during design validation can avoid manufacturability issues and ensure the PCBs function as intended in the end product.
Aluminum PCB Applications
With their performance benefits, aluminum PCBs are well suited for:
Power Electronics
Aluminum PCBs are ideal for power converters, inverters, motor drives, solar inverters, and similar demanding applications.
LED Lighting
High brightness LED designs need aluminum PCB’s excellent thermal dissipation to manage heat levels.
Automotive Electronics
Aluminum’s durability and reliability meets automotive electronics requirements while minimizing weight.
Aerospace and Military
Aluminum’s lightweight properties are beneficial in aircraft and military systems when size and weight are critical.
Consumer Electronics
Advanced gaming systems, computers, and devices can run more powerful processors cooled by aluminum PCBs.
RF and Microwave Circuits
Aluminum provides precise impedance control and stability for high frequency RF PCBs.
With continued technology innovations, we can expect more adoption of aluminum PCBs across industries where high performance and reliability are vital.
Aluminum PCBs – Frequently Asked Questions
Are aluminum PCBs more expensive than FR4 PCBs?
Yes, aluminum PCBs are generally more expensive due to the metal material and more complex fabrication process. However, they justify the cost in long term reliability gains in demanding applications.
Can components be soldered onto aluminum PCBs?
Soldering is possible with the right techniques, but requires more controlled heating than FR4 boards. It may need pre-heating or specific solder masks.not delaminate during use.
What are the limitations of aluminum PCBs?
Limitations include higher cost, more complex fabrication, restricted resistor types, difficulty soldering, and lower trace densities. Thermal design and CTE matching with components also needs consideration.
What are the different types of aluminum PCBs?
Common types are single sided, double sided, multilayer, aluminum on FR4, thick aluminum base, thin aluminum substrates, and aluminum coated copper boards.
How are aluminum PCBs tested?
They undergo electrical testing, bare board testing, solderability testing, environmental stress screening, thermal stress testing, and qualification testing to IPC standards.
Conclusion
Aluminum PCB technology enables lightweight and reliable solutions for thermal management, high frequency, and ruggedness needs demanded by advanced electronics.
With their expertise in metal PCB fabrication, choosing an experienced aluminum PCB manufacturer is crucial to harnessing the benefits of aluminum boards over traditional FR4 PCBs.
By understanding aluminum PCB capabilities, construction, design considerations, leading manufacturers, and applications, engineers can effectively leverage aluminum PCB technology to achieve product performance goals.
Leave a Reply