Understanding Polygon Pours and Rigid Flex PCBs
Polygon pours, also known as copper fills or copper pours, are commonly used in PCB Design to provide a low-impedance ground or power plane, reduce electromagnetic interference (EMI), and improve thermal performance. In Altium Designer, polygon pours are easily created and can be customized to suit various design requirements.
Rigid flex PCBs are a type of printed circuit board that combines rigid and flexible substrates, allowing for three-dimensional assembly and improved reliability in applications that require motion or folding. Designing rigid flex PCBs comes with its own set of challenges, one of which is maintaining the integrity of polygon pours across the split lines between rigid and flexible sections.
What are Split Lines in Rigid Flex PCBs?
Split lines, also referred to as transition zones or bend lines, are the boundaries between the rigid and flexible portions of a rigid flex PCB. These lines are essential for defining the mechanical properties of the board and ensuring proper functionality in the intended application.
When designing a rigid flex PCB in Altium Designer, it is crucial to properly define the split lines and ensure that all components, traces, and polygon pours are correctly positioned and connected across these boundaries.
Common Issues with Polygon Pours on Rigid Flex Split Lines
Polygon Pour Breaks
One of the most common problems encountered when working with polygon pours on rigid flex PCBs is the occurrence of breaks or discontinuities along the split lines. These breaks can lead to several issues, including:
- Reduced EMI shielding effectiveness
- Increased impedance and signal integrity problems
- Compromised thermal performance
- Potential reliability issues due to inconsistent Copper Distribution
Polygon pour breaks can occur for various reasons, such as:
- Improperly defined split lines
- Incorrect layer stack-up configuration
- Incompatible design rules for rigid and flex sections
- Insufficient clearance between polygon pours and split lines
Inconsistent Copper Distribution
Another issue that may arise when using polygon pours on rigid flex PCBs is inconsistent copper distribution across the split lines. This can happen when the polygon pour settings are not optimized for the specific requirements of the rigid and flexible sections, leading to an imbalance in copper coverage.
Inconsistent copper distribution can cause several problems, including:
- Uneven current distribution and potential hotspots
- Mechanical stress and strain at the split lines due to different thermal expansion rates
- Reduced flexibility and increased risk of cracking or delamination in the flexible sections
Best Practices for Designing Polygon Pours on Rigid Flex PCBs
To minimize the occurrence of polygon pour breaks and ensure consistent copper distribution on rigid flex PCBs, follow these best practices:
1. Clearly Define Split Lines
When creating the outline for your rigid flex PCB in Altium Designer, make sure to clearly define the split lines between the rigid and flexible sections. Use the appropriate layer types and line widths to differentiate between the various regions of the board.
2. Optimize Layer Stack-up
Design your layer stack-up with the specific requirements of rigid flex PCBs in mind. Consider the following factors:
- Material properties and thicknesses for rigid and flexible substrates
- Copper weight and distribution across layers
- Adhesive and coverlay materials and thicknesses
- Symmetry and balance of the stack-up
3. Create Specific Design Rules
Develop a set of design rules tailored for the rigid and flexible sections of your PCB. These rules should cover aspects such as:
- Minimum trace width and spacing
- Via size and placement
- Copper pour clearance and minimum width
- Component placement and orientation
By creating specific design rules for each section, you can ensure that your polygon pours are optimized for the unique requirements of rigid flex PCBs.
4. Use Teardrops and Reinforcement
To enhance the mechanical strength and reliability of your rigid flex PCB, incorporate teardrops at the junction of traces and pads, especially near the split lines. Teardrops help distribute stress and prevent cracks from forming in the copper.
Additionally, consider adding reinforcement, such as stiffeners or support structures, to the flexible sections near the split lines. This can help minimize mechanical stress and ensure a smooth transition between the rigid and flexible regions.
5. Perform Thorough DFM Checks
Before finalizing your design, conduct thorough Design for Manufacturability (DFM) checks to identify and resolve any potential issues with your polygon pours and split lines. Altium Designer offers a range of DFM Tools and reports that can help you optimize your design and ensure compatibility with manufacturing processes.
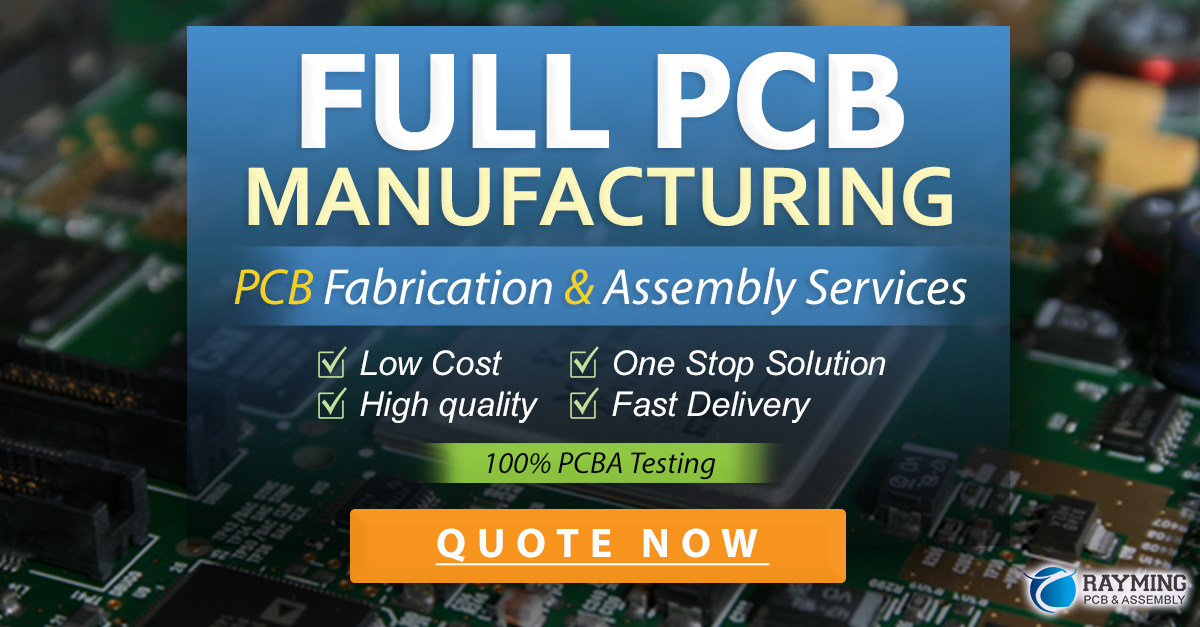
Troubleshooting Polygon Pour Breaks on Rigid Flex Split Lines
If you encounter polygon pour breaks or inconsistent copper distribution on your rigid flex PCB, follow these troubleshooting steps:
-
Review your split line definitions and ensure they are correctly positioned and assigned to the appropriate layers.
-
Check your layer stack-up and verify that the materials, thicknesses, and copper weights are suitable for rigid flex PCBs.
-
Examine your design rules and confirm that they are optimized for the specific requirements of the rigid and flexible sections.
-
Inspect your polygon pour settings, including clearance, minimum width, and thermal relief settings, and adjust them as needed.
-
Analyze your component placement and routing near the split lines, and make adjustments to minimize mechanical stress and improve copper distribution.
-
Run DFM checks and address any flagged issues or violations.
By following these troubleshooting steps and implementing the best practices outlined earlier, you can minimize the occurrence of polygon pour breaks and ensure a more reliable and manufacturable rigid flex PCB design.
Frequently Asked Questions (FAQ)
1. What causes polygon pour breaks on rigid flex split lines?
Polygon pour breaks on rigid flex split lines can occur due to various reasons, such as improperly defined split lines, incorrect layer stack-up configuration, incompatible design rules for rigid and flex sections, or insufficient clearance between polygon pours and split lines.
2. How can I prevent inconsistent copper distribution on my rigid flex PCB?
To prevent inconsistent copper distribution on your rigid flex PCB, optimize your layer stack-up for the specific requirements of rigid and flexible sections, create design rules tailored for each region, and use teardrops and reinforcement near the split lines.
3. What DFM checks should I perform to identify issues with polygon pours on rigid flex PCBs?
When performing DFM checks on rigid flex PCBs, focus on aspects such as split line definitions, layer stack-up compatibility, design rule compliance, polygon pour settings, and component placement and routing near the split lines.
4. Can I use the same design rules for both rigid and flexible sections of my PCB?
No, it is recommended to create specific design rules for the rigid and flexible sections of your PCB to ensure that your polygon pours and other design elements are optimized for the unique requirements of each region.
5. How can I reinforce the flexible sections near the split lines to improve reliability?
To reinforce the flexible sections near the split lines, consider adding stiffeners or support structures to minimize mechanical stress and ensure a smooth transition between the rigid and flexible regions. Additionally, use teardrops at the junction of traces and pads to distribute stress and prevent cracks from forming in the copper.
Conclusion
Designing polygon pours on rigid flex PCBs can be challenging, particularly when it comes to maintaining copper integrity and consistency across split lines. By understanding the common issues, such as polygon pour breaks and inconsistent copper distribution, and implementing best practices for design and troubleshooting, you can create more reliable and manufacturable rigid flex PCBs.
Remember to clearly define split lines, optimize your layer stack-up, create specific design rules, use teardrops and reinforcement, and perform thorough DFM checks to minimize the occurrence of polygon pour breaks and ensure the best possible performance of your rigid flex PCB design in Altium Designer.
Best Practice | Benefit |
---|---|
Clearly define split lines | Ensures proper differentiation between rigid and flexible sections |
Optimize layer stack-up | Accommodates the specific requirements of rigid flex PCBs |
Create specific design rules | Optimizes polygon pours for the unique needs of each section |
Use teardrops and reinforcement | Enhances mechanical strength and reliability near split lines |
Perform thorough DFM checks | Identifies and resolves potential issues before manufacturing |
By adhering to these guidelines and continuously refining your design process, you can overcome the challenges associated with polygon pours on rigid flex split lines and create high-quality, reliable PCBs that meet the demands of your application.
Leave a Reply