Introduction to AlN and Alumina Substrate Ceramic PCBs
Aluminum Nitride (AlN) and Alumina (Al2O3) are two widely used ceramic materials in the manufacturing of high-performance printed circuit boards (PCBs). These materials offer unique properties that make them suitable for applications demanding high thermal conductivity, electrical insulation, and mechanical stability. In this article, we will explore the characteristics of AlN and Alumina substrate ceramic PCBs and discuss the advantages of one-stop manufacturing solutions.
Properties of AlN and Alumina Substrates
AlN and Alumina substrates exhibit distinct properties that set them apart from traditional PCB materials. Let’s take a closer look at each material:
Aluminum Nitride (AlN)
- High thermal conductivity (150-180 W/mK)
- Excellent electrical insulation
- Low coefficient of thermal expansion (CTE)
- High mechanical strength and stability
- Good dielectric properties
Alumina (Al2O3)
- High electrical insulation
- High mechanical strength and hardness
- Excellent thermal stability
- Good thermal conductivity (20-30 W/mK)
- Low dielectric loss
Property | AlN | Alumina |
---|---|---|
Thermal Conductivity | 150-180 W/mK | 20-30 W/mK |
Electrical Insulation | Excellent | High |
CTE | Low | Moderate |
Mechanical Strength | High | High |
Dielectric Properties | Good | Low loss |
Applications of AlN and Alumina Substrate Ceramic PCBs
AlN and Alumina substrate ceramic PCBs find applications in various industries where high performance and reliability are critical. Some common applications include:
- Power Electronics
- High-power LED lighting
- Solar inverters
- Motor drives
-
Electric vehicle charging stations
-
RF and Microwave Devices
- Radar systems
- Satellite communications
- 5G wireless infrastructure
-
Aerospace and defense electronics
-
Medical Devices
- Implantable devices
- Diagnostic imaging equipment
-
Surgical instruments
-
Industrial Automation
- Sensors and actuators
- Process control systems
- Robotics and machine vision
Advantages of One-Stop Manufacturing for AlN and Alumina Substrate Ceramic PCBs
One-stop manufacturing refers to a comprehensive solution where all aspects of PCB Fabrication, from design to final assembly, are handled by a single provider. This approach offers several advantages for AlN and Alumina substrate ceramic PCBs:
1. Streamlined Process
With one-stop manufacturing, the entire PCB fabrication process is streamlined, eliminating the need for multiple vendors and reducing lead times. This enables faster time-to-market and improved efficiency.
2. Quality Control
Having a single provider responsible for the entire manufacturing process ensures better quality control. Consistent standards and processes can be maintained throughout the fabrication stages, minimizing the risk of defects and ensuring higher reliability.
3. Customization and Flexibility
One-stop manufacturing allows for greater customization and flexibility in PCB design and manufacturing. Customers can work closely with the manufacturer to optimize the PCB layout, material selection, and assembly processes to meet specific application requirements.
4. Cost-Effectiveness
By consolidating the manufacturing process under one roof, one-stop manufacturing can lead to cost savings. Reduced logistics costs, bulk material purchasing, and optimized production processes contribute to overall cost-effectiveness.
AlN-Alumina-PCB Manufacturing Process
The manufacturing process for AlN and Alumina substrate ceramic PCBs involves several key steps:
1. Substrate Preparation
The AlN or Alumina substrate is cleaned and prepared for the subsequent manufacturing processes. This may include surface grinding, polishing, and cleaning to ensure a smooth and contamination-free surface.
2. Circuit Patterning
The desired circuit pattern is created on the substrate using various techniques such as screen printing, photolithography, or direct bonding. Conductive materials like copper or gold are deposited to form the conductive traces.
3. Via Formation
Vias are created to establish electrical connections between different layers of the PCB. Laser drilling or mechanical drilling techniques are employed to create precise via holes in the substrate.
4. Metallization
The vias and circuit patterns are metallized using techniques like electroless plating or sputtering. This ensures reliable electrical connectivity and enhances the conductivity of the traces.
5. Insulation and Protection
Insulation layers, such as dielectric coatings or solder masks, are applied to protect the circuitry and provide electrical isolation. These layers also serve to prevent short circuits and improve the PCB’s durability.
6. Assembly and Packaging
The manufactured PCB undergoes assembly, where electronic components are mounted onto the board using techniques like surface mount technology (SMT) or through-hole mounting. Finally, the assembLED PCB is packaged and tested for functionality and reliability.
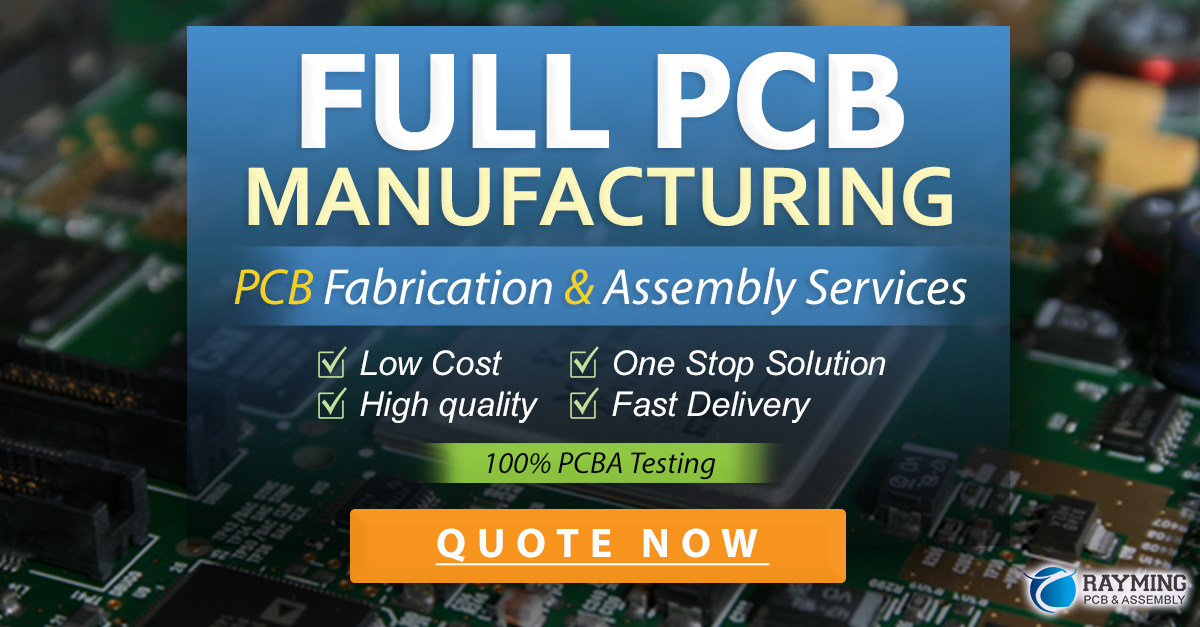
Challenges and Considerations in AlN and Alumina Substrate Ceramic PCB Manufacturing
While AlN and Alumina substrate ceramic PCBs offer numerous benefits, there are certain challenges and considerations to keep in mind during the manufacturing process:
1. Material Handling
AlN and Alumina substrates are brittle and require careful handling to prevent damage during manufacturing. Proper equipment and trained personnel are essential to ensure the substrates are processed without cracks or defects.
2. Thermal Management
AlN and Alumina substrates have different thermal expansion coefficients compared to other PCB materials. Careful design considerations are necessary to mitigate thermal stress and ensure reliable performance under varying temperature conditions.
3. Metallization Adhesion
Achieving strong adhesion between the metallization layers and the ceramic substrate is crucial for long-term reliability. Proper surface preparation and selection of compatible metallization materials are essential to ensure good adhesion.
4. Via Formation
Creating vias in ceramic substrates can be challenging due to their hardness and brittleness. Advanced techniques like laser drilling or specialized mechanical drilling processes are employed to achieve precise and reliable via formation.
Conclusion
AlN and Alumina substrate ceramic PCBs offer unique properties that make them ideal for high-performance applications demanding excellent thermal management, electrical insulation, and mechanical stability. One-stop manufacturing solutions provide a streamlined and efficient approach to fabricating these specialized PCBs, ensuring quality control, customization, and cost-effectiveness.
By understanding the properties, applications, and manufacturing processes of AlN and Alumina substrate ceramic PCBs, designers and engineers can make informed decisions when selecting the appropriate material and manufacturing approach for their specific requirements. With the right expertise and capabilities, one-stop manufacturing providers can deliver high-quality AlN and Alumina substrate ceramic PCBs that meet the demanding needs of various industries.
Frequently Asked Questions (FAQ)
1. What are the main differences between AlN and Alumina substrate ceramic PCBs?
AlN substrates have higher thermal conductivity compared to Alumina, making them suitable for applications requiring superior heat dissipation. Alumina substrates, on the other hand, offer excellent electrical insulation and mechanical strength. The choice between AlN and Alumina depends on the specific requirements of the application.
2. Can AlN and Alumina substrate ceramic PCBs be used for high-frequency applications?
Yes, both AlN and Alumina substrate ceramic PCBs are well-suited for high-frequency applications due to their low dielectric loss and good dielectric properties. They are commonly used in RF and microwave devices, satellite communications, and wireless infrastructure.
3. How does one-stop manufacturing benefit the production of AlN and Alumina substrate ceramic PCBs?
One-stop manufacturing streamlines the entire PCB fabrication process, reducing lead times and improving efficiency. It ensures better quality control, allows for greater customization and flexibility, and can lead to cost savings by consolidating the manufacturing process under one roof.
4. What are the challenges in drilling vias in AlN and Alumina substrates?
AlN and Alumina substrates are hard and brittle, making via formation challenging. Advanced techniques like laser drilling or specialized mechanical drilling processes are required to achieve precise and reliable via formation without damaging the substrate.
5. How can thermal stress be mitigated in AlN and Alumina substrate ceramic PCBs?
Thermal stress can be mitigated through careful design considerations, such as selecting appropriate materials for different layers, optimizing the layout to minimize thermal mismatches, and incorporating stress-relieving features. Proper thermal management techniques, like using heat spreaders or thermal vias, can also help dissipate heat effectively and reduce thermal stress.
Leave a Reply