What are PCB Gold Fingers?
PCB Gold Fingers, also known as edge connector contacts or gold-plated edge connectors, are the gold-plated contact pads on the edge of a printed circuit board (PCB). These gold-plated contacts are designed to provide a reliable and durable connection between the PCB and a mating connector or socket. Gold fingers are commonly found on various types of PCBs, including computer memory modules, expansion cards, and other plug-in boards.
Advantages of Gold Fingers on PCBs
Gold fingers offer several advantages over other types of connector contacts:
- Excellent conductivity: Gold is an excellent conductor of electricity, which ensures a low-resistance connection between the PCB and the mating connector.
- Corrosion resistance: Gold is highly resistant to corrosion and oxidation, which helps maintain a reliable connection over time, even in harsh environments.
- Durability: Gold-plated contacts are more durable than other materials, such as tin or nickel, and can withstand repeated insertions and removals without significant wear.
- Compatibility: Gold fingers are compatible with a wide range of mating connectors, making them a versatile choice for various applications.
Manufacturing Process of PCB Gold Fingers
The manufacturing process of PCB gold fingers involves several steps to ensure high-quality and reliable contacts:
1. PCB Fabrication
The first step is to fabricate the PCB itself. This involves designing the circuit layout, selecting the appropriate substrate material (such as FR-4), and creating the copper traces and pads on the board. The edge of the PCB where the gold fingers will be located is typically left exposed, without any solder mask or other coatings.
2. Nickel Plating
Before applying the gold plating, a layer of nickel is typically deposited on the exposed copper contacts. Nickel serves as a barrier layer between the copper and the gold, preventing the formation of intermetallic compounds that can weaken the connection over time. The nickel layer also provides a smooth and uniform surface for the gold plating to adhere to.
3. Gold Plating
The final step is to apply the gold plating to the nickel-plated contacts. This is typically done using an electroplating process, where the PCB is immersed in a gold plating solution and an electric current is applied. The thickness of the gold plating can vary depending on the application and the desired durability, but it is typically in the range of 0.05 to 0.5 micrometers (μm).
Gold Finger Plating Thickness
The thickness of the gold plating on PCB gold fingers is an important consideration, as it affects the durability and reliability of the connection. The following table provides a comparison of common gold plating thicknesses and their applications:
Gold Plating Thickness (μm) | Application |
---|---|
0.05 – 0.1 | Low-cost, short-life applications |
0.2 – 0.3 | General-purpose, moderate-life applications |
0.5 – 1.0 | High-reliability, long-life applications |
1.0 – 2.0 | Extreme-durability, high-insertion applications |
Designing PCBs with Gold Fingers
When designing a PCB with gold fingers, there are several factors to consider to ensure a reliable and durable connection:
1. Contact Pitch and Width
The pitch and width of the gold finger contacts should be designed to match the mating connector. Common pitches include 1.27 mm (0.05 inch) and 2.54 mm (0.1 inch). The width of the contacts should be sufficient to provide a good contact area while allowing for proper spacing between adjacent contacts.
2. Contact Length and Chamfer
The length of the gold finger contacts should be designed to provide sufficient contact area with the mating connector. A typical length is around 5-10 mm. The end of the contacts should also be chamfered (beveled) to facilitate insertion into the mating connector and prevent damage to the contacts.
3. Solder Mask and Coverlay
The solder mask and coverlay on the PCB should be designed to expose the gold finger contacts while protecting the rest of the PCB. The solder mask should have a clean and sharp edge along the gold fingers to prevent solder bridging or contamination. A coverlay may be used to provide additional protection and insulation for the PCB.
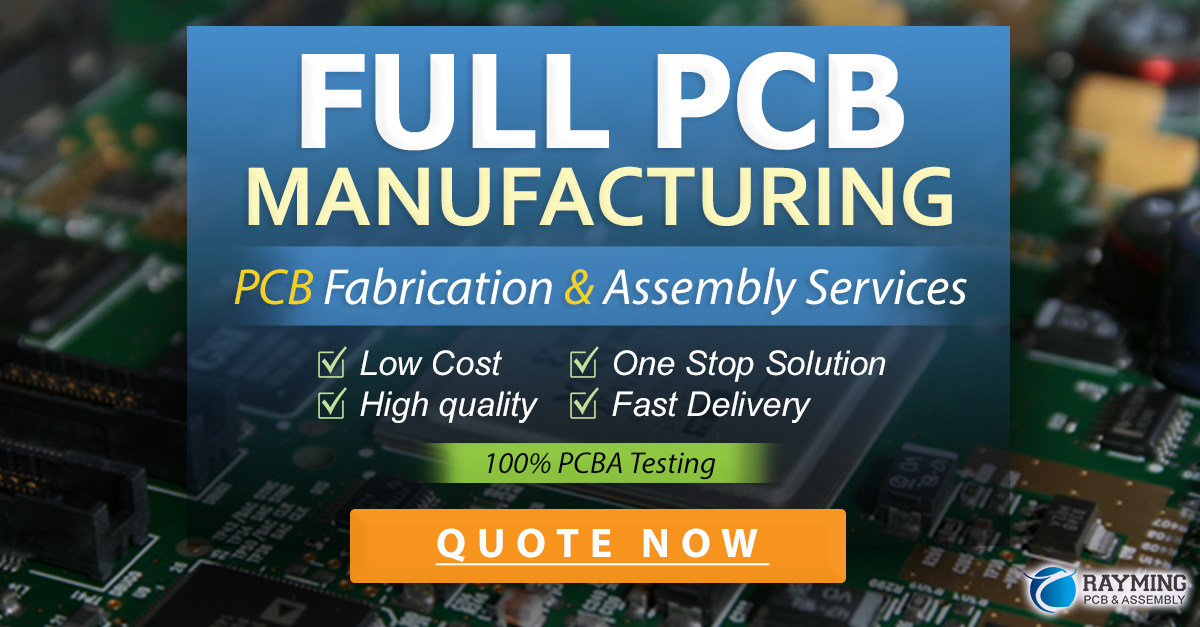
Testing and Quality Control
To ensure the reliability and durability of PCB gold fingers, several testing and quality control measures are typically employed:
1. Visual Inspection
Visual inspection is the first step in quality control, where the gold fingers are examined under magnification for any defects, such as scratches, pits, or contamination. The plating thickness and uniformity are also checked visually.
2. Continuity and Resistance Testing
Electrical continuity and resistance testing are performed to ensure that the gold finger contacts are properly connected to the PCB traces and that there are no open or short circuits. The resistance of the contacts should be within the specified range for the application.
3. Durability Testing
Durability testing involves subjecting the gold fingers to repeated insertion and removal cycles to simulate the expected use conditions. The number of cycles can vary depending on the application, but it is typically in the range of 500 to 5000 cycles. After the durability testing, the gold fingers are inspected for any signs of wear or damage.
4. Environmental Testing
Environmental testing may be performed to ensure that the gold fingers can withstand the expected operating conditions, such as temperature, humidity, and vibration. This can include thermal cycling, humidity exposure, and vibration testing.
Applications of PCB Gold Fingers
PCB gold fingers are used in a wide range of applications where reliable and durable connections are required. Some common applications include:
1. Computer Memory Modules
Gold fingers are used on computer memory modules, such as DIMMs (Dual Inline Memory Modules) and SIMMs (Single Inline Memory Modules), to provide a connection between the module and the motherboard. The gold fingers on the module mate with the corresponding socket on the motherboard, allowing for easy installation and removal.
2. Expansion Cards
Expansion cards, such as graphics cards, sound cards, and network cards, use gold fingers to connect to the motherboard via a PCI (Peripheral Component Interconnect) or PCIe (PCI Express) slot. The gold fingers provide a high-speed, low-latency connection between the card and the motherboard.
3. Plug-in Boards
Various types of plug-in boards, such as sensor boards, communication boards, and power supply boards, use gold fingers to connect to a backplane or motherboard. The gold fingers provide a reliable and durable connection that can withstand repeated insertions and removals.
4. Industrial and Automotive Applications
PCB gold fingers are also used in industrial and automotive applications where reliable connections are critical. This can include control modules, sensor interfaces, and communication modules. The gold plating provides excellent corrosion resistance and durability in harsh environments.
Frequently Asked Questions (FAQ)
-
Q: What is the difference between gold fingers and edge connectors?
A: Gold fingers and edge connectors refer to the same thing – the gold-plated contact pads on the edge of a PCB that provide a connection to a mating connector or socket. -
Q: Why is gold used for PCB edge connectors?
A: Gold is used for PCB edge connectors because of its excellent conductivity, corrosion resistance, and durability. Gold-plated contacts provide a reliable and low-resistance connection that can withstand repeated insertions and removals. -
Q: What is the typical thickness of gold plating on PCB fingers?
A: The typical thickness of gold plating on PCB fingers ranges from 0.05 to 0.5 micrometers (μm), depending on the application and desired durability. Thicker gold plating is used for high-reliability and long-life applications. -
Q: Can gold fingers be repaired if damaged?
A: In most cases, damaged gold fingers cannot be easily repaired. If the damage is severe, such as deep scratches or worn-off plating, the PCB may need to be replaced. Minor damage, such as surface contamination, may be cleaned using specialized cleaning solutions. -
Q: Are there any alternatives to gold for PCB edge connectors?
A: While gold is the most common material for PCB edge connectors, other materials, such as palladium-nickel alloys, can be used in some applications. However, these alternatives may not provide the same level of conductivity, corrosion resistance, and durability as gold.
Conclusion
PCB gold fingers are a critical component in many electronic devices, providing a reliable and durable connection between PCBs and mating connectors. The gold plating on the edge connector contacts ensures excellent conductivity, corrosion resistance, and durability, making them suitable for a wide range of applications, from computer memory modules to industrial control systems.
When designing PCBs with gold fingers, it is important to consider factors such as contact pitch, width, length, and chamfer, as well as the thickness of the gold plating. Proper testing and quality control measures, including visual inspection, continuity and resistance testing, durability testing, and environmental testing, are essential to ensure the reliability and longevity of the gold finger connections.
As technology continues to advance, the demand for reliable and high-performance edge connector solutions will only increase. PCB gold fingers are likely to remain a key component in meeting these demands, providing a proven and effective solution for connecting PCBs in a wide range of applications.
Leave a Reply