Introduction to PCB Cleanliness
Printed Circuit Boards (PCBs) are the backbone of modern electronic devices. They provide the necessary connections and support for various components to function together as a system. However, the cleanliness of a PCB can have a significant impact on its performance and reliability. Dirt, debris, and contamination on a PCB can lead to a range of issues, from minor signal disturbances to complete system failure.
In this article, we will explore the importance of PCB cleanliness, the types of contamination that can affect PCBs, and the methods used to ensure PCBs are clean and functioning optimally.
The Importance of PCB Cleanliness
Ensuring Proper Functionality
One of the primary reasons for maintaining PCB cleanliness is to ensure proper functionality of the electronic device. Contamination on a PCB can interfere with the electrical signals passing through the board, leading to signal distortion, noise, or even complete signal failure. This can cause the device to malfunction or perform poorly, resulting in a suboptimal user experience.
Preventing Short Circuits and Electrical Failures
Dirt, dust, and other debris on a PCB can also cause short circuits and electrical failures. When contaminants bridge the gap between two or more electrical contacts, it can create an unintended pathway for current to flow, leading to a short circuit. Short circuits can damage components, cause overheating, and even lead to complete system failure.
Enhancing Reliability and Longevity
A clean PCB is more likely to function reliably over its intended lifespan. Contamination can cause corrosion, which weakens the electrical connections and leads to premature failure of components. By keeping PCBs clean, manufacturers can enhance the reliability and longevity of their products, reducing the need for repairs or replacements.
Meeting Industry Standards and Regulations
Many industries have specific standards and regulations regarding PCB cleanliness. For example, the medical and aerospace industries require high levels of cleanliness to ensure the safety and reliability of their devices. Failure to meet these standards can result in non-compliance, leading to costly penalties or even product recalls.
Types of PCB Contamination
Flux Residues
Flux is a chemical used during the soldering process to remove oxides from metal surfaces and promote the formation of a strong solder joint. However, if the flux is not properly cleaned after soldering, it can leave residues on the PCB. These residues can be conductive, leading to short circuits or signal disturbances.
Dust and Debris
Dust and debris can accumulate on a PCB during the manufacturing process or through exposure to the environment. These contaminants can interfere with electrical signals and cause short circuits, especially if they are conductive.
Moisture and Humidity
Moisture and humidity can also affect PCB performance. If a PCB is exposed to high levels of moisture, it can lead to corrosion of the metal traces and components. This can weaken the electrical connections and cause failures over time.
Chemical Contamination
Chemical contamination can occur when a PCB is exposed to various substances, such as cleaning agents, oils, or even fingerprints. These contaminants can react with the materials on the PCB, causing corrosion or degradation of the electrical properties.
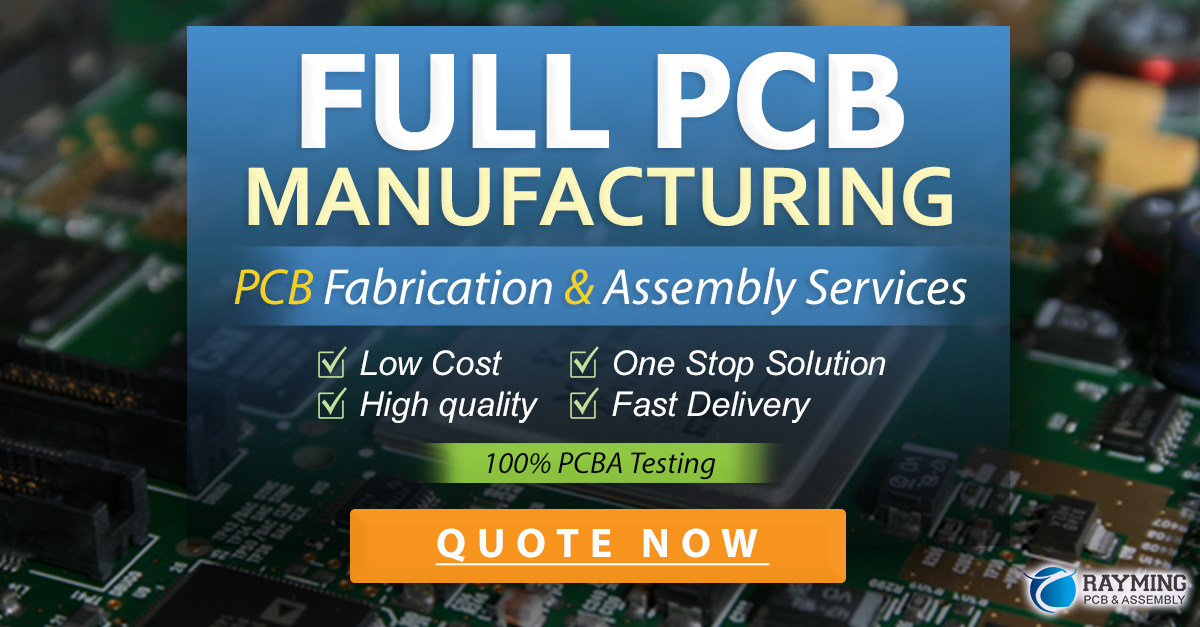
Methods for Ensuring PCB Cleanliness
Cleaning During Manufacturing
One of the most effective ways to ensure PCB cleanliness is to implement cleaning processes during the manufacturing stage. This can involve using specialized cleaning agents and equipment to remove flux residues, dust, and other contaminants from the PCB surface. Common cleaning methods include:
- Aqueous cleaning: Uses water-based solutions to remove contaminants
- Solvent cleaning: Uses chemical solvents to dissolve and remove contaminants
- Plasma cleaning: Uses ionized gas to react with and remove contaminants
Cleaning Method | Advantages | Disadvantages |
---|---|---|
Aqueous Cleaning | – Environmentally friendly – Safe for most PCB materials – Effective for removing flux residues |
– May not be suitable for water-sensitive components – Requires thorough drying to prevent moisture-related issues |
Solvent Cleaning | – Effective for removing a wide range of contaminants – Fast evaporation minimizes drying time |
– Some solvents may be hazardous or environmentally harmful – Can damage certain PCB materials if not carefully selected |
Plasma Cleaning | – Highly effective for removing organic contaminants – Dry process eliminates moisture-related issues |
– Requires specialized equipment – May not be suitable for all PCB materials |
Protective Coatings and Enclosures
Another way to maintain PCB cleanliness is to apply protective coatings or use enclosures to shield the board from contaminants. Conformal coatings, such as acrylic, silicone, or polyurethane, can be applied to the PCB surface to create a barrier against moisture, dust, and other environmental factors. Enclosures, such as sealed boxes or cases, can also be used to protect the PCB from external contamination.
Proper Handling and Storage
Proper handling and storage of PCBs can also help maintain their cleanliness. This includes:
- Using clean, lint-free gloves when handling PCBs to avoid transferring oils and contaminants from the skin
- Storing PCBs in clean, dry environments with controlled temperature and humidity levels
- Avoiding exposure to dust, debris, and other potential contaminants during storage and transportation
Regular Inspection and Maintenance
Regular inspection and maintenance of PCBs can help identify and address cleanliness issues before they cause significant problems. This can involve:
- Visual inspection of the PCB surface for signs of contamination, corrosion, or damage
- Cleaning the PCB using appropriate methods and materials when necessary
- Monitoring the performance of the device to detect any signal disturbances or malfunctions that may be related to PCB contamination
Case Studies
Case Study 1: Medical Device Manufacturer
A medical device manufacturer was experiencing intermittent failures in one of their products. Upon investigation, it was discovered that the failures were caused by flux residues on the PCBs, which were creating short circuits. The manufacturer implemented an aqueous cleaning process during the manufacturing stage and saw a significant reduction in failure rates.
Case Study 2: Aerospace Component Supplier
An aerospace component supplier was required to meet strict cleanliness standards for their PCBs. To achieve this, they used a combination of solvent cleaning and plasma cleaning processes to remove contaminants from the PCBs. They also implemented strict handling and storage protocols to prevent contamination during the manufacturing process. As a result, they were able to consistently produce PCBs that met the required cleanliness standards.
FAQ
-
Q: How can I tell if my PCB is contaminated?
A: Visual inspection is often the first step in identifying PCB contamination. Look for signs of residue, corrosion, or discoloration on the PCB surface. If you suspect contamination, you can also use analytical methods, such as ionic contamination testing or surface insulation resistance (SIR) testing, to quantify the level of contamination. -
Q: Can I clean my PCB using household cleaning products?
A: It is not recommended to use household cleaning products on PCBs, as they may contain chemicals that can damage the board or leave residues. Always use cleaning agents and methods that are specifically designed for use on PCBs. -
Q: How often should I clean my PCBs?
A: The frequency of cleaning depends on the environment in which the PCB is used and the level of contamination it is exposed to. In general, it is a good practice to clean PCBs during the manufacturing process and then periodically inspect and clean them as needed during their operational life. -
Q: Can PCB contamination cause permanent damage to my device?
A: Yes, in some cases, PCB contamination can cause permanent damage to components or the board itself. For example, corrosion caused by moisture or chemical contamination can degrade the electrical connections and lead to premature failure of the device. -
Q: What should I do if I suspect my PCB is contaminated?
A: If you suspect your PCB is contaminated, the first step is to identify the type and extent of the contamination. You can then select an appropriate cleaning method based on the type of contamination and the materials used in the PCB. If you are unsure how to proceed, it is best to consult with a professional or the manufacturer of the device for guidance.
Conclusion
PCB cleanliness is a critical factor in ensuring the proper functionality, reliability, and longevity of electronic devices. Contamination on a PCB can lead to signal disturbances, short circuits, and even complete system failure. By understanding the types of contamination that can affect PCBs and implementing appropriate cleaning and maintenance methods, manufacturers can produce high-quality, reliable products that meet industry standards and customer expectations.
Regular inspection, cleaning, and maintenance of PCBs throughout their operational life can also help identify and address cleanliness issues before they cause significant problems. By prioritizing PCB cleanliness, manufacturers can improve the performance and lifespan of their products, reduce maintenance and repair costs, and enhance customer satisfaction.
Leave a Reply