Introduction
Printed circuit boards (PCBs) are an essential component of most modern electronics. They provide the foundation on which integrated circuits and other electronic components are mounted and interconnected. With electronics playing a critical role in everything from consumer devices to advanced manufacturing, military systems, and infrastructure, domestic PCB production and supply chain security have become topics of increasing interest. This article will examine the current state of PCB manufacturing in the United States.
PCB Manufacturing Overview
A printed circuit board consists of a non-conductive substrate made from materials such as fiberglass or ceramics, upon which conductive pathways or “traces” are patterned from copper sheets laminated onto the substrate. PCBs can be single sided with traces on one side only, or double sided with traces on both sides. Multi-layer PCBs with traces sandwiched between layers are also common.
PCBs go through many stages of manufacturing:
- Design – The PCB layout is designed using CAD software, specifying trace locations, pad sizes for components, etc.
- Photolithography – The desired trace pattern is transferred to the copper cladding via a light-sensitive chemical resist and series of chemical processing steps.
- Etching – Exposed copper is etched away, leaving only the desired traces protected by the resist.
- Solder mask – A polymer coating is applied over the entire PCB surface for insulation and mechanical protection, with openings left for soldering pads.
- Silkscreen – Identifying markings, component legends, and other labels are printed on the solder mask.
- Surface finish – The exposed copper pads receive a surface coating such as HASL (solder), immersion gold, or ENIG to facilitate soldering and prevent oxidation.
- Testing and inspection – Bare boards are tested for manufacturing defects and functionality prior to population with components.
History of US PCB Production
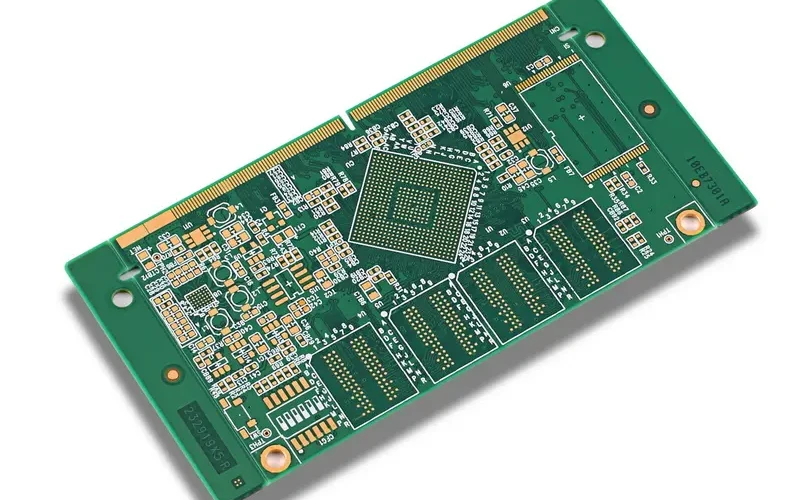
The American electronics industry pioneered PCB technology in the 1950s, with companies like HP, IBM, and Bell Labs among the first adopters. By 1970, there were over 500 PCB manufacturers in the US producing over $500 million in PCBs annually. The industry continued to grow steadily, with domestic production peaking in 1998 at $10.3 billion according to industry figures. Global competition began to intensify in the 1990s however, particularly from East Asia, eroding the US share of PCB production. By the early 2000s, lower labor costs, scale, and proximity to electronics supply chains made China the world’s predominant location for volume PCB manufacturing. Unable to compete on costs, many US PCB factories closed down.
Year | Estimated # of US PCB Manufacturers |
---|---|
1970 | Over 500 |
1998 | Around 800 |
2005 | Around 200 |
2015 | Around 125 |
Current State of US PCB Production
Despite the migration of high volume, low cost PCB work overseas, PCB manufacturing continues in the US today. The US PCB market was estimated at $3.2 billion in 2021. There are well over 100 domestic PCB manufacturers serving various niches where proximity, engineering collaboration, fast turnaround, or security considerations justify local production.
Rather than competing directly with offshore vendors on costs, most US PCB companies focus on:
- Prototyping – Quick-turn fabrication of new designs with close customer collaboration.
- Low to medium volume production – Typically for defense, medical, aerospace, industrial and niche commercial applications. Run sizes from tens to thousands of boards.
- Advanced technologies – HDI (high density interconnect) multilayer, flex/rigid flex, metal core PCBs, etc. that benefit from close engineering support.
Even the largest global electronics firms making millions of consumer devices source at least some of their PCB needs from US vendors for these reasons.
While automation and process improvements have made US factories more cost competitive, labor is still a larger component compared to overseas facilities. To survive, US PCB fabricators have had to specialize and stay on the leading edge of advanced manufacturing techniques.
Advanced Manufacturing Improving US Competitiveness
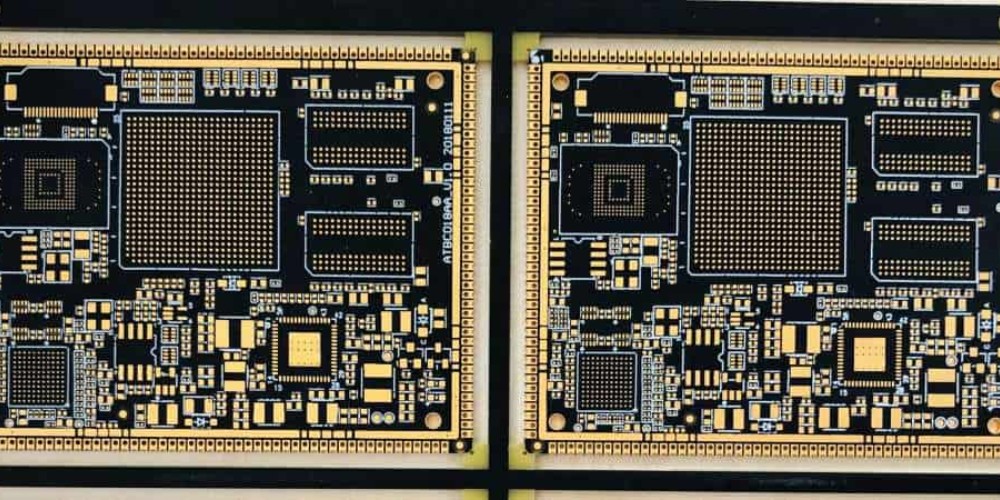
Several technological trends are making it more viable for US companies to manufacture PCBs domestically:
HDI PCBs – Continued miniaturization and complexity of electronics drives demand for multilayer boards with very fine features, tight tolerances, and high component densities. This plays to the strengths of American companies focused on advanced processes.
Direct imaging – Laser direct imaging eliminates the need for phototools used in traditional photolithography. It streamlines prototyping, enables fast design revisions, and reduces costs. Most US PCB shops now use direct imaging.
Automation – Increased use of automation in drilling, routing, optical inspection, testing, and other production steps offsets higher US wage rates.
Cycle time reduction – US factories are focused on agile processes with flexible equipment to provide fast delivery of small batches. This offsets offshore cost advantages at higher volumes.
Supply chain security – For defense and other sensitive electronics, sourcing PCBs domestically reduces risks of counterfeits or tampering. Supply chain transparency provides peace of mind.
These advanced manufacturing techniques allow US PCB companies to be competitive for shorter runs where their expertise in engineering support and rapid fabrication outperforms offshore vendors geared toward high volume.
Outlook for US PCB Production
After declines in the 1990s and 2000s, the tide seems to be turning for PCB manufacturing in America:
- Industry associations project modest growth in US PCB output over the next 5 years as domestic production retains market share.
- Several new US facilities have opened recently, including fabrication plants in Ohio, Oregon, and Arizona.
- Reshoring incentives from government agencies and large OEMs are encouraging domestic sourcing.
- Investments continue in R&D and new equipment to drive further productivity gains.
While the US is unlikely to recapture the huge PCB production volumes of past decades, local specialized manufacturing seems poised to thrive serving the needs of American design innovation.
Frequently Asked Questions
What are the main reasons PCB production moved overseas?
Lower labor costs along with massive economies of scale were the key drivers that shifted high volume PCB production to Asia starting in the 1990s. Domestic US factories could not compete on costs for commodity boards. Proximity to electronics supply chains also favored Asian manufacturing hubs.
Does the military still make PCBs in the US?
Yes, there are several PCB companies in the US focused on defense and aerospace applications where security is critical. ITAR regulations also restrict certain technologies from being exported. Keeping sensitive PCB production domestic reduces risks related to counterfeits or tampering.
Are hobbyist PCBs manufactured in the US?
A few US companies cater to hobbyists by offering small quantity PCB fabrication. However, most hobby PCB production has moved offshore. Labor intensive processes for low volumes are more viable with lower Asian labor rates. Hobby boards do not require the advanced processes or engineering support used in professional US PCB shops.
How can I find American made PCBs?
Industry associations like the IPC maintain directories of US PCB manufacturers. You can search for fabricators based on capabilities and locations. Key things to look for are facilities with the latest direct imaging equipment and a focus on advanced technologies, quick-turn prototyping, and medium volume production.
Is domestic PCB production likely to increase?
Trends point toward a stabilization or even slight growth in US PCB output. Improved productivity from automation, accelerated processes, and advanced manufacturing techniques help US factories be more cost competitive. Supply chain security and reshoring incentives also support American production for defense, medical, aerospace, and other select applications.
Leave a Reply