Printed circuit boards (PCBs) are an essential component of most modern electronic devices. Determining the cost to manufacture PCBs can be tricky because many factors influence the overall price. This article will examine the key considerations when estimating PCB fabrication costs and provide a detailed breakdown of common expenses.
What is a PCB?
A PCB is a thin board made of fiberglass or other insulating materials. Conductive pathways or “traces” are etched from copper sheets and laminated onto the board. Electronic components are then soldered onto the PCB to create a functional circuit.
PCBs provide mechanical support and electrical connections between components. They are more reliable and compact than hand-wired circuits. PCBs enabled the miniaturization of electronics and are ubiquitous in all types of devices today.
Key factors affecting PCB cost
Several key factors determine the cost of manufacturing PCBs:
Board size
In general, larger boards are more expensive to produce than smaller boards. This is because more raw materials are required. Standard PCB sizes range from around 50 x 50 mm up to 610 x 460 mm.
Layer count
Most PCBs consist of a double-sided or multilayer board. Double-sided has copper traces on both sides. Multilayer boards stack several double-sided boards with insulating dielectric material between each layer.
More layers allow for increased component density and complex circuit routing. But each additional layer adds to material and fabrication costs.
Materials
The substrate material (usually FR-4 fiberglass) and copper thickness affect cost. Standard 1.6 mm thick FR-4 and 1 oz copper traces are inexpensive. Thicker boards with more copper or exotic materials like Teflon or ceramic cost more.
Quantity
Economies of scale apply to PCB production. Manufacturing a large production run yields a much lower per-unit cost compared to a small prototype batch.
Lead time
Rushing PCB fabrication to get boards sooner involves premium fees. Standard lead times range from 2-10 days, with rush orders completed in 1-3 days for extra cost.
Complexity
Boards with dense component layouts or very fine trace spacings require more production time and charge higher prices. Specialized production equipment is needed for electroplated gold traces or multilayer boards over 6 layers.
Solder mask and silkscreen
Applying solder mask (for oxidation protection) and silkscreen labelling adds cost compared to basic bare boards. Additional finishing steps like edge plating or conformal coating also increase cost.
PCB fabrication process overview
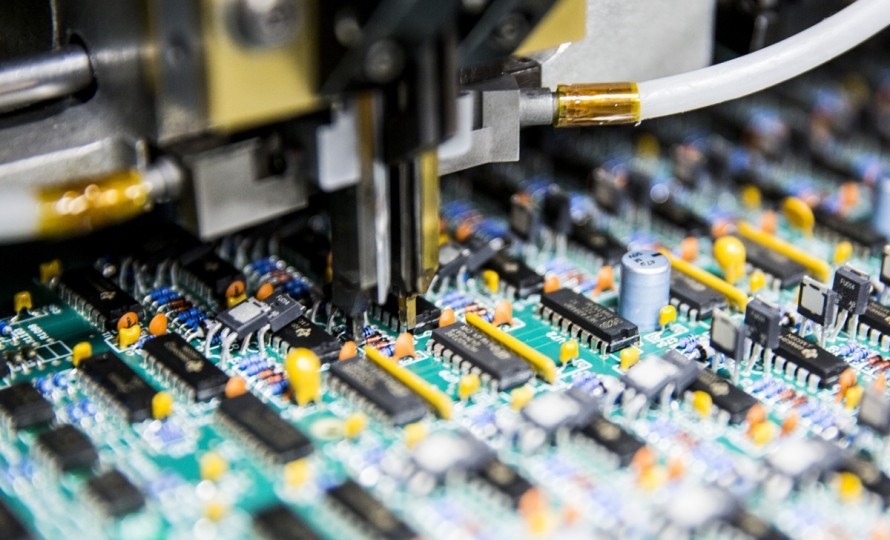
Understanding the PCB manufacturing process helps explain the costs involved:
Design
The board layout is designed in CAD software. This generates Gerber files used for board fabrication and stencil/assembly files.
Fabrication
Boards start as blank copper-clad laminate sheets. An etching process removes unwanted copper, leaving only the desired conductive traces. Layers are aligned, stacked, and laminated together. Drill holes are added for component leads.
Assembly
Solder paste is screen-printed onto the board through a stencil. Components are precisely placed using pick-and-place machines. The boards pass through a reflow oven to melt the solder and attach components.
Testing
Finished boards are electrically tested for shorts, opens, and functioning. Automated Optical Inspection (AOI) checks for defects. Boards are reworked or discarded if any issues are found.
Finishing
Additional finishing steps are completed as needed, such as solder mask application, silkscreen printing, edge plating, or conformal coating.
Cost breakdown
Here is a detailed breakdown of typical costs for a medium complexity 4-layer PCB with standard features:
Material costs
- Raw PCB substrate (FR-4): $5
- Copper foils: $0.50
- Soldermask: $0.30
- Silkscreen: $0.20
Fabrication processes
- Imaging and etching: $1.50
- Drilling: $0.40
- Lamination: $1.20
- Testing: $0.30
Equipment depreciation
- $0.80
Labor
- $1.20
Overhead
- Plant costs, utilities: $0.90
Profit margin
- ~30%: $2.70
Total cost per board
$15
As you can see, material costs account for a relatively small portion of the overall expenses. Most of the cost comes from the specialized equipment and labor required to manufacture PCBs. The fabrication process itself adds significant costs. And a healthy profit margin is built in.
Cost optimization tips
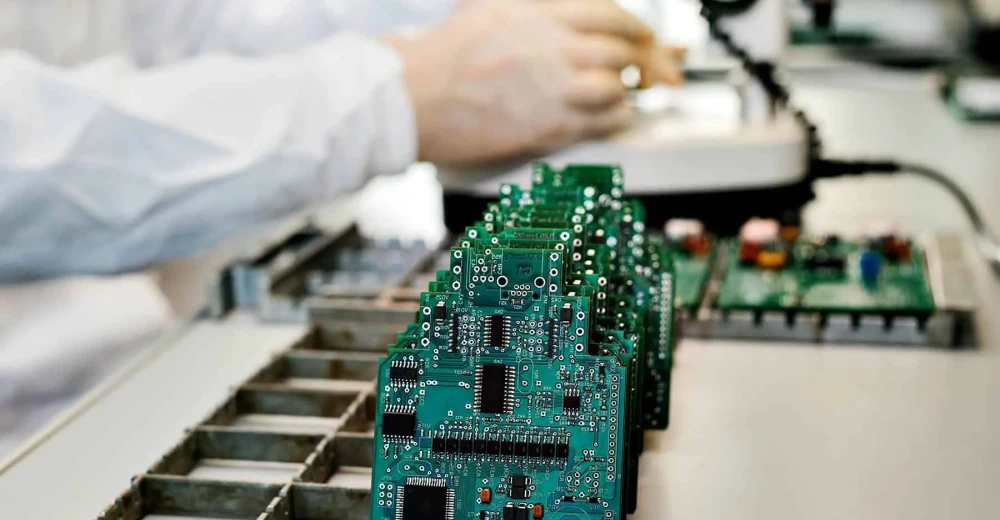
Here are some ways to optimize PCB costs:
- Order larger quantities – Increase volume to lower per unit costs through economies of scale.
- Consolidate designs – Combine multiple boards into a single panel to maximize surface area.
- Standardize materials – Use common FR-4 and 1oz copper to avoid premiums.
- Simplify layouts – Reduce layer count if possible. Avoid dense routing and tiny components.
- Choose standard sizes – Custom board shapes incur added fees.
- Use panelization – Manufacture multiple boards on a large panel for efficiency.
- Lengthen lead times – Allow longer fabrication times for better pricing.
- Minimize special processes – Extras like heavy copper, blind/buried vias, or flex PCBs add cost.
- Compare vendors – Shop around for competitive quotes, taking experience and quality into account.
Typical low-volume prototype costs
Here are approximate price ranges for small quantity PCB prototype orders, which are more expensive per board than production volumes:
Board Type | Size | Quantity | Cost per board |
---|---|---|---|
2-layer PCB | 100 x 100 mm | 10 boards | $5 – $15 |
4-layer PCB | 150 x 100 mm | 10 boards | $60 – $100 |
6-layer HDI PCB | 200 x 150 mm | 5 boards | $250 – $500 |
Medium and high volume production costs
For medium to high production runs in the hundreds or thousands of boards, cost per unit drops dramatically:
Board Type | Size | Quantity | Cost per board |
---|---|---|---|
2-layer PCB | 100 x 100 mm | 1,000 boards | $2 – $4 |
4-layer PCB | 200 x 150 mm | 1,000 boards | $8 – $15 |
6-layer HDI PCB | 250 x 200 mm | 1,000 boards | $30 – $60 |
So producing 1,000 boards yields about 5-10 times cost savings compared to small prototype orders. Very high volumes in the tens of thousands can drop PCB costs below $1.
Other helpful cost estimators
There are some useful online calculators that can estimate PCB costs based on various parameters:
These can provide ballpark quotes for comparison. Getting quotes directly from manufacturers is recommended for more precise costing.
Conclusion
Determining PCB fabrication costs involves considering many factors like size, layer count, order volume, and manufacturing processes required. While prototyping small batches is expensive per board, increasing volume yields much lower costs. Careful design optimization and shopping around can help reduce expenses. For critical electronic products, quality should be balanced with cost savings.
Frequently Asked Questions
What are the main factors that affect PCB cost?
The main factors affecting PCB cost are:
- Board size – larger boards use more materials
- Layer count – more layers increases fabrication complexity
- Order volume – high volumes benefit from economies of scale
- Lead times – rush orders have premium fees
- Design complexity – dense boards require more production effort
- Special processes – additional steps like solder mask or gold traces add cost
Does board size or layer count impact cost more?
Generally layer count has a much greater impact on cost than board size, because additional layers significantly increase fabrication complexity and material costs. The base PCB substrate is relatively inexpensive, while each extra layer adds more materials, processing, and labor expenses.
How much does it cost to make 10 2-layer PCB boards?
For a small 2-layer board of around 100 x 100 mm, fabricating 10 prototype boards would typically cost between $5 – $15 per board. So total cost for 10 boards would be $50 – $150, depending on the PCB manufacturer used.
What are some ways to reduce PCB costs?
Ways to reduce PCB costs include:
- Ordering larger quantities for volume discounts
- Consolidating multiple board designs into a panel
- Simplifying layouts by reducing layers if possible
- Standardizing materials and sizes
- Allowing longer fabrication lead times
- Comparing quotes from multiple vendors
Is it cheaper to get PCB assembly done in China?
Often yes, having PCBs assembled and components sourced in China can be significantly cheaper than assembly in other regions. However, extended shipping lead times often offset this advantage. Communication barriers and component quality issues also need to be considered carefully.
Leave a Reply