Understanding blind holes and through holes
When working with metal parts that require holes to be drilled or machined, there are two main types of holes – blind holes and through holes. The key difference between these two hole types comes down to how far they extend through the thickness of the metal.
Blind holes – A blind hole is a hole that extends only partially through a piece of metal. It does not go all the way through the full thickness of the metal. Blind holes stop at a certain depth and are closed at the bottom.
Through holes – A through hole is a hole that passes fully through the entire thickness of a piece of metal, creating openings on both sides. Through holes are open at both ends allowing complete passage through the metal.
So in summary:
- A blind hole does NOT go all the way through the metal. It only goes part way through.
- A through hole DOES go completely through from one side to the other.
Knowing the difference between these two hole types is important when machining or drilling metal parts so that the correct hole type can be created depending on requirements.
Why use a blind hole versus a through hole?
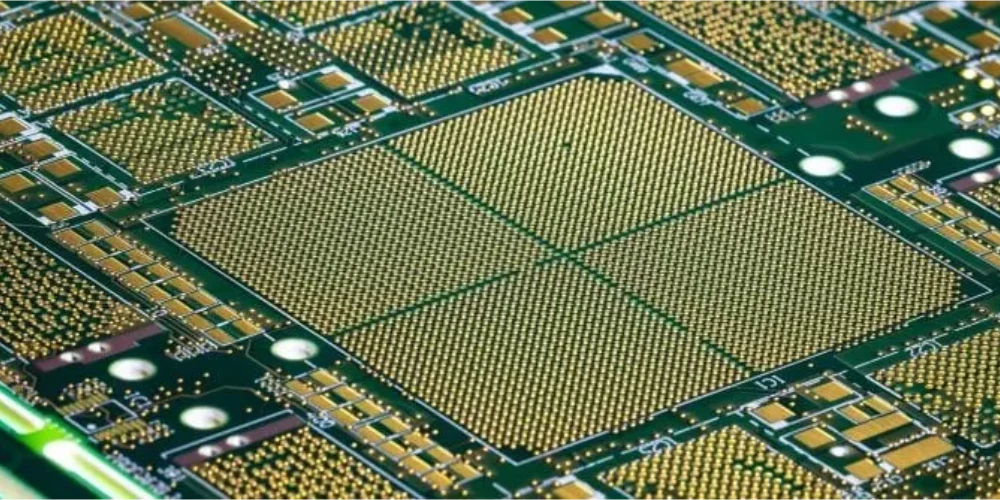
There are several reasons why a blind hole may be preferred over a through hole in certain applications:
- Weight savings – Creating a blind hole rather than a through hole removes material and decreases weight. This is advantageous in applications where lighter weight is desired such as aircraft parts.
- Enclosing features – Blind holes allow enclosing or capturing items that need to be embedded within a part and not pass fully through it. For example, a bearing race would require a blind hole.
- Structural integrity – Through holes can sometimes compromise the strength of a part more than a blind hole. The remaining solid material around a blind hole better retains structural integrity.
- Resisting wear and failure – Blind holes are closed at the bottom which can help trap lubricants. The closed end also resists wear and damage better than an open through hole.
- Simplified manufacturing – Drilling a blind hole is often easier and faster than creating a through hole, especially in thick materials. It avoids the extra step of breaking through the second side.
So in deciding between specifying a blind or through hole, engineers must consider the functional requirements of the application. But in general, blind holes will be used whenever the advantages they offer are needed.
How are blind holes created?
There are several techniques that can be used to create blind holes in metal parts depending on the capabilities of the machining equipment:
- Drilling – On manual milling machines, drill bits are used to create blind holes. The depth is controlled by setting a stop to limit the travel of the drill feed.
- Boring – Boring head attachments on manual or CNC milling machines can create very precise and accurate blind holes with excellent finish quality.
- CNC machining – CNC milling programs can machine blind hole depths based on specified coordinates and tool paths. No stop is required.
- EDM (Electrical discharge machining) – For difficult to machine specialty metals, EDM uses electrical sparks to erode very accurate blind holes of any desired depth.
- Laser drilling – Laser beams focused on a metal surface can instantly vaporize material to “drill” very small, clean blind holes without contact forces.
- Punching/stamping – Punches and dies can stamp out metal blanks with preformed blind holes for high volume production.
Machining Method | Hole Size Capability | Depth Accuracy | Surface Finish |
---|---|---|---|
Drilling | Small to medium holes | Moderate | Good |
Boring | Medium to large holes | Very high | Excellent |
CNC Milling | Small to large holes | High | Very good |
EDM | Small to very small holes | Extremely high | Excellent |
Laser Drilling | Micro holes | High | Excellent |
Punching/Stamping | Small holes | Low | Rough |
Table: Comparison of blind hole machining methods
As you can see, modern machining methods offer a wide range of options for creating blind holes to meet the needs of the application. Correct selection of the machining process is important for optimizing hole attributes.
What are some typical applications of blind holes?
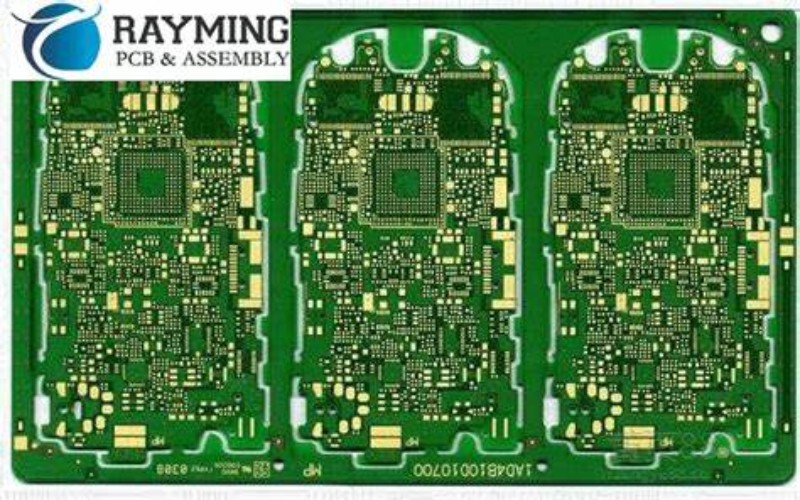
Blind holes are useful across many different industries and engineering disciplines. Here are some common examples of where blind holes are utilized:
- Bearing fits and mounts – Blind holes precisely fit bearings and allow mounting without going through the full material thickness.
- Electrical components – Blind holes provide mounting points for electrical inserts like transformers and capacitors within electrical enclosures.
- Handgrips – The mounting holes in bicycle handlebars or other handgrips are often blind holes.
- Attachment points – Blind holes allow securing brackets, stands, and other attachments at certain points on machinery without passing through the entire structure.
- Hydraulic cylinders – Blind holes at the end caps retain fluid and pressure without leakage through a full pass through hole.
- Sight glass fittings – Viewing windows in vessels and pipes use blind holes to mount while containing pressure.
- Medical implants – Blind holes provide anchoring points for screws and fixation devices in hip and knee replacements.
- Heat exchanger tubes – The tubes in heat exchangers have blind holes for retention rather than through holes.
- Aircraft engines – Blind holes extensively used in turbine and engine blocks for weight savings and containment.
These examples demonstrate the diversity of blind hole applications across many industries. Their usefulness stems from the specific advantages they provide by not passing fully through the material thickness.
Potential problems from incorrect use of blind holes
While blind holes serve many useful functions, there are some potential problems that can arise if they are used incorrectly:
- Fluid leakage – Using a blind hole where a through hole is required can result in fluid leakage since the hole does not fully penetrate the material.
- Pressure buildup – Trapped gases or fluids within a blind hole instead of a vented through hole can result in dangerous pressure increases.
- Stress concentrations – Improperly sized or shaped blind holes can create localized stress points leading to premature failure.
- Fastener bottoming – If a fastener bottoms out at the bottom of a blind hole, tightening torque is lost which can lead to loosening under vibration.
- Insufficient thread engagement – Threads in a blind hole need to account for reduced engagement area compared to a through hole to provide sufficient strength.
- Chip evacuation issues – Blind hole drilling can trap chips inside the hole leading to quality problems in tight tolerance applications.
- Difficult inspection – The closed end of blind holes makes inspection for defects more difficult compared to through holes.
Proper engineering and design practices are needed to mitigate these potential issues when using blind holes. Thorough analysis should determine if a blind or through hole is appropriate for the application.
Best practices for utilizing blind holes
To take full advantage of blind holes while avoiding problems, here are some recommended best practices:
- Clearly specify hole type, depth, diameter tolerance, and quality requirements.
- Allow minimum side clearances around blind holes for tool access.
- Account for chip evacuation from deep blind holes in drill design.
- Limit depth to diameter ratio to avoid weakening the material.
- Design threaded blind holes with at least 1.5 x diameter thread engagement.
- Break sharp internal corners at hole bottom with a radius to reduce stress points.
- Inspect blind holes using customized gauges and measurement probes.
- Test final parts under simulated operating conditions to identify any issues.
- Use gaskets, plugs, or covers to seal blind holes that contact fluids.
- Select surface finishes appropriate for the application like thread fit or bearing mount.
Careful blind hole design, machining, inspection, and testing reduces risk and helps guarantee reliable performance in the final component or assembly.
FAQ
Are blind holes weaker than through holes?
Not necessarily. The remaining material around a properly designed and manufactured blind hole will retain considerable strength. However, care must be taken with depth, diameter, side clearances and stress concentrations. Deeper and larger blind holes or tight clearance to edges can start to significantly compromise strength.
Can you tap threads into a blind hole?
Yes, tapping threads into blind holes is common. However, the depth of engagement needs consideration so that the threads at the bottom have enough strength. Generally, the threaded depth of a blind hole should be at least 1.5 times the hole diameter.
What are some alternatives to machining blind holes?
In some cases, options like weld nuts, rivet nuts, or captive nuts allow threads or fastener holes without machining the main material thickness. Press fit bushings or grommets can also create bore holes. Using separate removable covers or plates is another alternative.
How do you properly seal a blind hole?
To properly seal a blind hole that will be exposed to fluids, avoid relying solely on a fastener or fitting tightened into the hole. A pressure-rated gasket, o-ring, adhesive sealant, or threaded plug will better seal the blind hole from leakage. Match sealing methods to fluid type and pressure levels.
How can you determine if a hole is blind or not?
If the hole end is accessible, simple visual inspection or using a wire probe can help determine if it is blind or not. For blind holes that are hard to access at the closed end, techniques like ultrasonic thickness gauging or flow testing can identify if the hole fully penetrates or not.
Leave a Reply