Introduction
As electronics become more complex and packed into ever-smaller spaces, high density interconnect (HDI) PCBs with 24 or more layers are increasingly needed. These multilayer boards allow for denser component mounting and routing, minimizing space requirements. However, manufacturing these intricate PCBs requires specialized expertise and equipment. Choosing the right 24 layer HDI PCB manufacturer is crucial to getting boards fabricated correctly and on time. This article provides guidance on selecting the best partner for your 24+ layer HDI PCB needs.
Key Considerations When Selecting a 24 Layer HDI PCB Manufacturer
Selecting a manufacturer able to reliably produce multilayer HDI PCBs requires evaluating several key factors:
HDI Technology Capabilities
The manufacturer must have advanced HDI capabilities including:
- Laser microvia drilling down to 25μm or less
- Microvia filling and planarization
- Fine line patterning of traces/spaces down to 15μm or below
- Layer alignment accuracy better than 5μm
- Use of thinner dielectrics (25-50μm)
They should also be able to incorporate embedded passives and high-density interconnects like microvias or stacked vias.
Experience with High Layer Count PCBs
Look for proven experience manufacturing boards with 24-32 layers. They should have expertise with lamination, drilling, and handling such thin multilayer boards.
Rigorous Quality Control
Stringent quality control is essential, including:
- Automated optical inspection (AOI)
- Ionic contamination testing
- Impedance, continuity, and hipot testing
- Cross-section analysis
This helps catch defects and ensure reliable HDI boards.
Staff Engineering Expertise
The manufacturer should have engineers on staff knowledgeable in HDI design and manufacturing. They can provide design for manufacturing (DFM) guidance and help resolve any issues.
Strong Customer Service
They should assign dedicated account managers for direct customer support and communication. This facilitates feedback and quick resolution of any production issues.
Production Capabilities
- They should have sufficient HDI PCB production capacity with minimal lead times.
- Mass lamination equipment is needed for multilayer boards along with advanced drilling and imaging equipment.
- Flexible and scalable production capabilities are preferable.
Comparing Potential 24 Layer HDI PCB Manufacturers
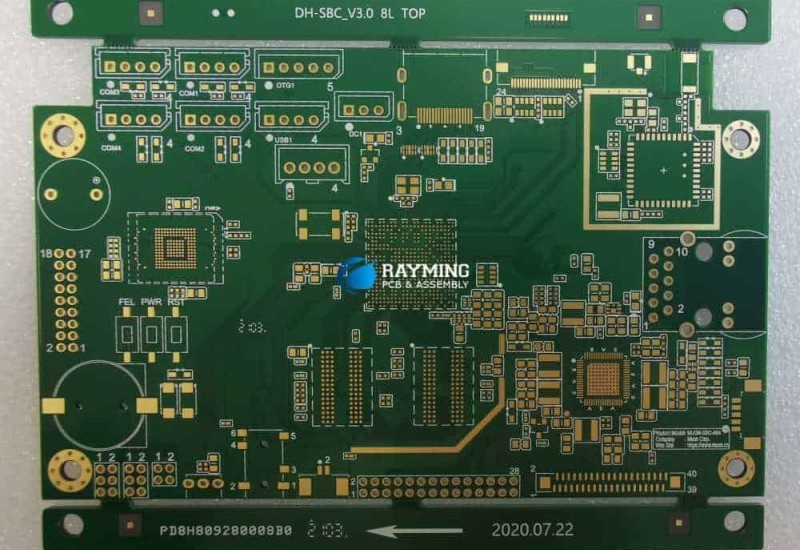
With an understanding of key selection criteria, you can now evaluate manufacturers. Here is an example comparison of three potential partners:
Table 1: Comparison of Potential 24 Layer HDI PCB Manufacturers
Manufacturer 1 | Manufacturer 2 | Manufacturer 3 | |
---|---|---|---|
Location | China | USA | Taiwan |
HDI Experience | 10+ years | 5+ years | 15+ years |
HDI Capabilities | Microvias to 20μm, line/space to 10μm | Microvias to 30μm, line/space to 15μm | Microvias to 25μm, line/space to 12μm |
Max Layers | 32 | 28 | 30 |
Quality Certs | ISO 9001, UL | ISO 9001 | ISO 9001, IPC |
Volume Capabilities | 10,000 boards/month | 3,000 boards/month | 7,000 boards/month |
Lead Times | 15 days | 25 days | 20 days |
DFM Assistance | Standard | Limited | Comprehensive |
Customer Support | Direct account manager | Limited contact | Account manager |
Prices | $$ | $$$ | $$ |
This comparison shows that Manufacturer 3 may be the best fit with strong HDI capabilities, quality systems, capacity, and customer support. Manufacturer 1 also looks capable but has slightly lower specs. Manufacturer 2 lags in several areas critical for advanced HDI boards.
Key Questions to Ask Potential Manufacturers
Once you’ve identified a few potential 24 layer HDI PCB partners, you’ll want to contact them with specific questions before making a decision. Here are some suggested questions:
- What is your experience manufacturing multilayer boards over 20 layers? Can you share examples?
- What are your minimum microvia size and line/space capabilities?
- What HDI materials and stackups do you commonly work with?
- How do you ensure layer-to-layer registration accuracy?
- What test capabilities do you have for verifying HDI boards?
- What quality certifications do you hold?
- What is your process for DFM analysis and feedback?
- How do you monitor and control impedance on HDI boards?
- What are your lead times for quotations and production?
- What IT infrastructure do you have for data security and confidentiality?
- How do you ensure on-time delivery for quick-turn prototypes?
- How can you accommodate variable production volumes or rapid ramp-up?
Their responses will help reveal their experience, expertise, and capabilities for your project. Be sure to get references to contact on past HDI and multilayer PCB projects as well.
Handling the Design and Documentation Process
To smooth the design and manufacturing process with your selected vendor:
- Have your designer collaborate directly with the manufacturer’s engineers to incorporate DFM feedback into the layout from the start.
- Ensure your data is compatible with the manufacturer’s CAD/CAM software and adhere to their design rules. Get their libraries.
- Have your designer thoroughly complete the fabrication drawing with all needed details specified. Missing information will delay the process.
- For quick-turn prototypes, mark non-critical tolerances to optimize cycle time.
- Share native CAM data including signal integrity properties for precise modeling.
- To confirm manufacturability, submit design files for upfront review before final data release.
- For complex boards, consider paying for an initial trial build or sample before full production.
Thorough communications and information sharing is key to avoiding delays and getting your 24+ layer HDI boards produced correctly the first time.
Quality Assurance Considerations
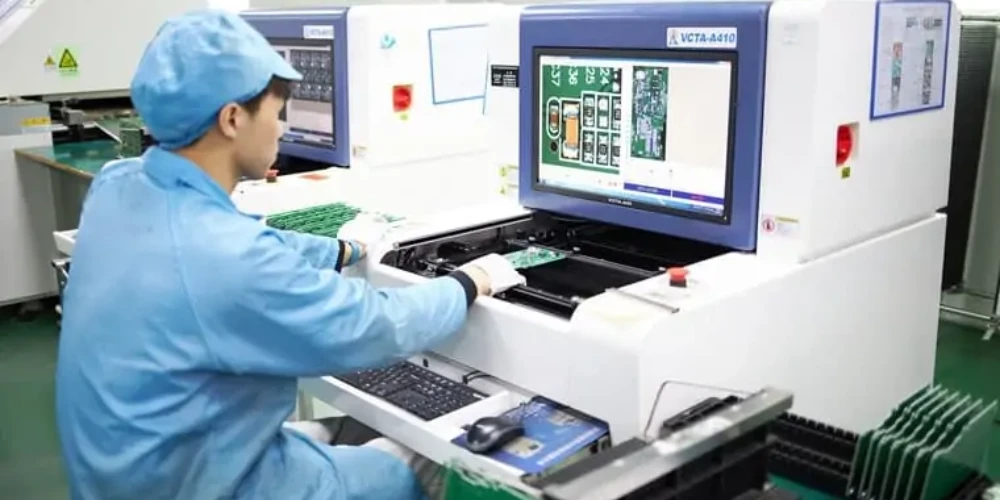
To ensure you receive boards without defects, qualify the manufacturer’s inspection process and consider:
- Requesting AOI test reports for your boards showing 100% inspection.
- Having an independent quality audit performed if needed for high reliability requirements.
- Requiring cross-section analyses on sample boards from initial builds.
- Doing sample functional testing of boards through a test fixture to catch any manufacturing issues.
- Performing a thorough incoming inspection of boards including x-ray, AOI, and net list testing.
- Having the manufacturer environmentally stress test boards through temperature cycling, vibration, etc.
Build time into your schedule in case reworking or re-spins are required. Work closely with the manufacturer to implement process controls and feedback loops.
Key Takeaways on Selecting a Great 24 Layer HDI PCB Manufacturing Partner
- Rigorous HDI capabilities and proven multilayer experience are mandatory – ask for proof.
- Quality systems and certifications provide assurance of process controls.
- Direct engineering support and DFM assistance are invaluable.
- Look for outstanding customer service and communication.
- Validate capabilities meet your technical requirements and production volumes.
- Design collaboration and information sharing are vital for optimizing the development process.
- Allow time and budget for quality assurance measures and potential issues requiring reworking.
With careful partner selection and close cooperation, you can get advanced 24+ layer HDI boards fabricated to your most demanding specifications, on schedule, and with confidence.
Frequently Asked Questions
What are the main difficulties in manufacturing 24 layer HDI PCBs?
Some of the main challenges include:
- Achieving extremely tight layer-to-layer registration and alignment tolerances.
- Drilling high densities of small microvias consistently and reliably.
- Eliminating voids and blemishes during lamination and plating.
- Preventing warpage of thin multilayer boards.
- Handling boards without damage, scratches or contamination.
- Achieving acceptable yields given the complexity.
It requires tremendous precision and process controls.
How long does it typically take to manufacture 24 layer HDI PCBs?
For prototype quantities, allow 3-4 weeks from design completion to receipt of finished boards. For production runs, expect roughly 2-3 week lead times once the fabrication documentation is finalized. The time is dominated by the advanced preparation and lamination processes required.
How much more expensive are 24 layer boards versus standard MLBs?
In general, expect 24 layer HDI PCBs to cost roughly 5-10x as much as comparable 6-8 layer standard MLB designs. The specialized materials and intensive processes required contribute greatly to the costs.
What design considerations are important for 24 layer HDI boards?
Critical factors include:
- Minimizing unwanted capacitance through careful stackup design.
- Managing heat dissipation given the denser designs.
- Controlling impedances through inclusion of ground planes.
- Incorporating thermal relief connections for tightly spaced components.
- Allowing sufficient spacing around microvias.
- Adding fiducials for layer alignment.
Work closely on DFM with your PCB manufacturer.
How large can 24 layer HDI boards be manufactured?
While fabrication size depends on the manufacturer’s capabilities, generally 24 layer boards can be made up to 20” x 16” (500mm x 400mm) or potentially larger. Very large boards will have higher risks of warpage or damage though. Discuss your specific size requirements with prospective manufacturers.
Conclusion
Specifying the ideal 24 layer HDI PCB manufacturer requires a careful balance of technical capabilities, expertise, quality systems, and customer service. Validate that potential partners meet your requirements and can manufacture these complex boards reliably. Collaborate closely with their engineering team and implement robust quality assurance measures. Stay involved throughout the fabrication process. With the right manufacturer and an optimized development approach, you can successfully produce advanced 24+ layer HDI PCBs to meet your needs.
Leave a Reply