Introduction to Gold-Plated Edge Connectors
Gold-plated edge connectors are a type of electrical connector commonly used in various electronic devices, such as computers, telecommunications equipment, and industrial machinery. These connectors are designed to provide a reliable and efficient means of connecting printed circuit boards (PCBs) to other components or systems. The gold plating on the surface of the connector ensures excellent conductivity, corrosion resistance, and durability, making them ideal for applications that require high performance and reliability.
What are Edge Connectors?
Edge connectors are a type of electrical connector that is used to connect a printed circuit board (PCB) to another PCB, a backplane, or a motherboard. They are called “edge” connectors because they are designed to mate with the edge of a PCB, which has exposed copper traces that serve as the electrical contacts. Edge connectors come in various sizes, shapes, and pin configurations to accommodate different PCB designs and applications.
Advantages of Gold Plating
Gold plating is a process where a thin layer of gold is deposited onto the surface of the connector contacts. Gold is an excellent choice for plating because it offers several advantages:
- High conductivity: Gold is one of the most conductive metals, which ensures efficient and reliable electrical connections.
- Corrosion resistance: Gold does not oxidize or tarnish, making it resistant to corrosion and degradation over time.
- Durability: Gold-plated contacts can withstand repeated mating cycles and maintain their integrity, even in harsh environments.
- Low contact resistance: Gold-plated contacts exhibit low electrical resistance, which minimizes signal loss and improves overall system performance.
Types of Gold-Plated Edge Connectors
There are several types of gold-plated edge connectors available, each designed for specific applications and requirements.
Card Edge Connectors
Card edge connectors are the most common type of edge connector. They are designed to mate directly with the exposed copper traces on the edge of a PCB. These connectors are typically used in computers, telecommunications equipment, and consumer electronics.
Connector Type | Pitch (mm) | Number of Pins | Applications |
---|---|---|---|
PCI Express | 1.0 | 36 – 164 | Computers |
DDR DIMM | 2.54 | 240 – 288 | Computers |
CompactPCI | 2.0 | 110 – 440 | Industrial |
Backplane Connectors
Backplane connectors are used to connect multiple PCBs or modules to a common backplane in a system. These connectors are typically more robust and have higher pin counts compared to card edge connectors. They are commonly used in industrial, military, and aerospace applications.
Connector Type | Pitch (mm) | Number of Pins | Applications |
---|---|---|---|
DIN 41612 | 2.54 | 32 – 160 | Industrial |
VME64x | 2.0 | 160 – 320 | Military |
FMC | 1.27 | 160 – 400 | Aerospace |
Mezzanine Connectors
Mezzanine connectors are used to stack PCBs vertically, allowing for high-density interconnects in a small footprint. These connectors are often used in high-speed digital applications, such as telecommunications and data centers.
Connector Type | Pitch (mm) | Number of Pins | Applications |
---|---|---|---|
PCIe Mezzanine | 1.0 | 60 – 184 | Telecom |
FMC+ | 0.8 | 400 – 800 | Data Centers |
XMC | 1.27 | 114 – 320 | Military |
Manufacturing Process of Gold-Plated Edge Connectors
The manufacturing process of gold-plated edge connectors involves several steps to ensure high quality and reliability.
Base Material Selection
The base material for the connector contacts is typically a copper alloy, such as brass or phosphor bronze. These materials are chosen for their excellent electrical conductivity, mechanical strength, and formability.
Stamping and Forming
The connector contacts are stamped and formed from the base material using high-precision tools and dies. This process creates the desired shape and size of the contacts, as well as any features such as retention barbs or alignment guides.
Plating Process
After stamping and forming, the connector contacts undergo a multi-step plating process to create the gold surface finish.
- Pre-treatment: The contacts are cleaned and prepared for plating to ensure proper adhesion of the subsequent layers.
- Nickel plating: A layer of nickel is plated onto the contacts to provide a barrier between the base material and the gold layer. Nickel also improves the wear resistance and durability of the contacts.
- Gold plating: A thin layer of gold, typically 0.5 to 2.0 micrometers thick, is plated onto the nickel layer. The gold plating can be either hard gold or soft gold, depending on the application requirements.
Assembly and Testing
Once the contacts are plated, they are assembled into the connector housing along with any other components, such as retention clips or alignment pins. The assembled connectors are then tested for electrical continuity, signal integrity, and mechanical reliability to ensure they meet the required specifications.
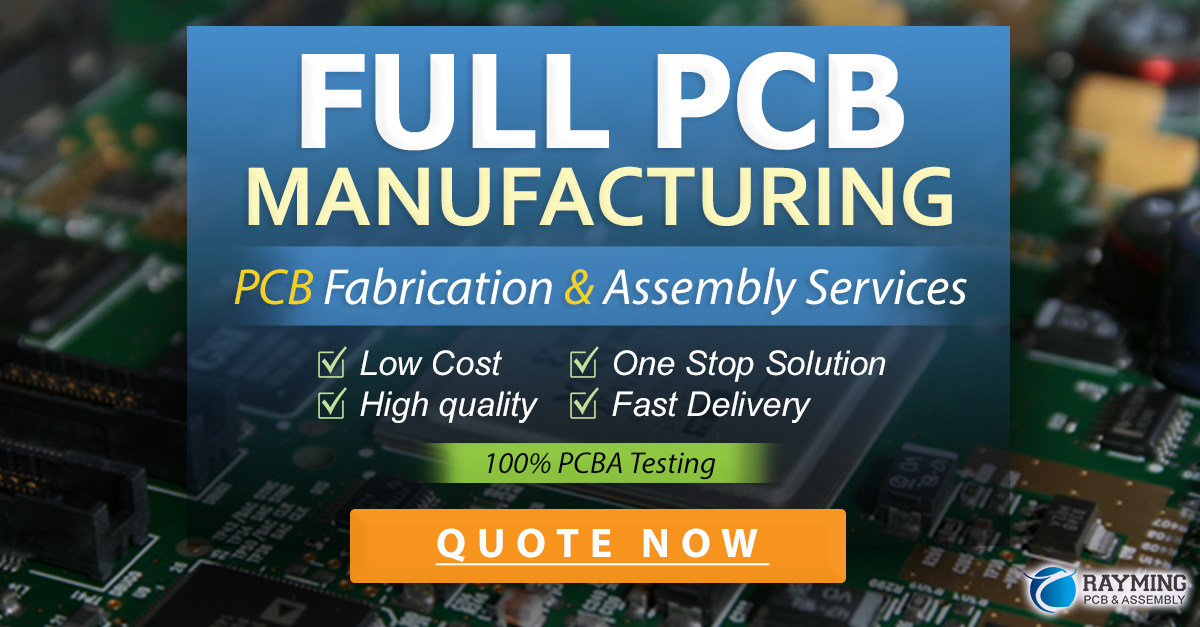
Applications of Gold-Plated Edge Connectors
Gold-plated edge connectors are used in a wide range of industries and applications where high performance, reliability, and durability are critical.
Computers and Consumer Electronics
In computers and consumer electronics, gold-plated edge connectors are used for various interfaces, such as:
- PCI Express (PCIe) slots for graphics cards, sound cards, and other expansion cards
- DDR DIMM slots for computer memory modules
- SATA and IDE connectors for hard drives and optical drives
- USB and HDMI connectors for external devices
Telecommunications
In the telecommunications industry, gold-plated edge connectors are used in:
- Backplane systems for routers, switches, and other networking equipment
- Mezzanine connectors for high-speed interconnects between boards
- Fiber optic transceivers and modules
Industrial and Automotive
Gold-plated edge connectors are used in industrial and automotive applications for their reliability and resistance to harsh environments. Examples include:
- Industrial control systems and PLCs
- Automotive electronics, such as engine control units and infotainment systems
- Medical devices and equipment
- Aerospace and military systems
High-Speed Digital Applications
Gold-plated edge connectors are essential for high-speed digital applications, where signal integrity and low contact resistance are critical. Some examples include:
- High-performance computing and data centers
- Test and measurement equipment
- High-definition video and audio systems
Advantages of Using Gold-Plated Edge Connectors
Gold-plated edge connectors offer several advantages over other connector types and surface finishes:
- Excellent electrical conductivity: Gold’s high conductivity ensures efficient and reliable electrical connections, minimizing signal loss and improving system performance.
- Superior corrosion resistance: Gold does not oxidize or tarnish, providing long-term protection against corrosion and degradation, even in harsh environments.
- Durability and reliability: Gold-plated contacts can withstand repeated mating cycles and maintain their integrity, reducing the need for maintenance and replacement.
- Low contact resistance: The low electrical resistance of gold-plated contacts minimizes signal loss and improves overall system efficiency.
- Compatibility with various environments: Gold-plated connectors can operate in a wide range of temperatures and humidity levels, making them suitable for diverse applications.
Design Considerations for Gold-Plated Edge Connectors
When designing or selecting gold-plated edge connectors for a specific application, several factors should be considered to ensure optimal performance and reliability.
Mating Cycles
The number of mating cycles (insertions and removals) that a connector is expected to endure over its lifetime is a critical design consideration. Gold-plated connectors can typically withstand a higher number of mating cycles compared to other surface finishes, but the specific requirements may vary depending on the application.
Environmental Factors
The operating environment of the connector should be carefully evaluated, including factors such as temperature, humidity, and the presence of contaminants or corrosive elements. Gold-plated connectors offer excellent protection against corrosion and can operate in a wide range of environments, but additional measures such as Conformal Coatings or sealed housings may be necessary for extreme conditions.
Signal Integrity
For high-speed digital applications, signal integrity is a critical design consideration. Gold-plated connectors provide low contact resistance and minimal signal loss, but other factors such as impedance matching, crosstalk, and electromagnetic interference (EMI) should also be addressed through proper PCB layout and shielding techniques.
Cost and Availability
Gold-plated connectors typically come at a higher cost compared to other surface finishes due to the materials and processes involved. However, the long-term benefits in terms of reliability and performance often outweigh the initial cost. Availability and lead times should also be considered when selecting a specific connector for a design.
Maintenance and Troubleshooting
Proper maintenance and troubleshooting practices can help ensure the longevity and reliability of gold-plated edge connectors in a system.
Handling and Storage
Gold-plated connectors should be handled with care to avoid damage or contamination. Proper storage conditions, such as humidity control and protection from dust and debris, can help maintain the connectors’ integrity when not in use.
Inspection and Cleaning
Regular inspection of the connectors for signs of wear, damage, or contamination can help prevent issues before they cause system failures. If necessary, the connectors can be cleaned using specialized solvents and tools, following the manufacturer’s recommendations.
Troubleshooting
In case of system issues related to the connectors, a systematic troubleshooting approach should be followed. This may involve:
- Checking for proper seating and alignment of the connectors
- Inspecting the connectors for damage or contamination
- Testing the electrical continuity and signal integrity of the connections
- Isolating the issue by swapping components or testing with known-good parts
Frequently Asked Questions (FAQ)
- What is the difference between hard gold and soft gold plating?
-
Hard gold plating has a higher content of cobalt or nickel, making it more wear-resistant and suitable for applications with frequent mating cycles. Soft gold plating has a higher purity and is more ductile, making it better for applications with low mating cycles and high performance requirements.
-
How thick should the gold plating be on an edge connector?
-
The typical thickness of gold plating on edge connectors ranges from 0.5 to 2.0 micrometers (15 to 50 microinches). The specific thickness depends on the application requirements, such as the number of mating cycles and the operating environment.
-
Can gold-plated connectors be used in high-temperature environments?
-
Yes, gold-plated connectors can operate in a wide range of temperatures, typically from -55°C to +125°C, depending on the specific design and materials used. For extreme high-temperature applications, additional considerations such as the base material and housing design may be necessary.
-
How do gold-plated connectors compare to other surface finishes in terms of cost?
-
Gold-plated connectors are generally more expensive than connectors with other surface finishes, such as tin or nickel. However, the higher cost is often justified by the superior performance, reliability, and durability provided by gold plating, especially in critical applications.
-
Can gold-plated connectors be replaced with other types of connectors?
- In some cases, gold-plated connectors can be replaced with other types of connectors, such as press-fit or soldered connectors, depending on the specific application requirements. However, the unique benefits of gold plating, such as high conductivity, corrosion resistance, and low contact resistance, may be difficult to replicate with other connector types.
Conclusion
Gold-plated edge connectors are a critical component in many electronic systems, offering superior electrical conductivity, corrosion resistance, and durability. These connectors are used in a wide range of industries and applications, from consumer electronics and telecommunications to industrial and aerospace systems.
When designing or selecting gold-plated edge connectors, it is essential to consider factors such as mating cycles, environmental conditions, signal integrity, and cost. Proper handling, maintenance, and troubleshooting practices can help ensure the longevity and reliability of these connectors in a system.
As technology continues to advance, the demand for high-performance, reliable interconnects will only grow. Gold-plated edge connectors are well-positioned to meet these challenges and enable the next generation of electronic devices and systems.
Leave a Reply