Introduction to Hi-speed Design
Hi-speed design refers to the process of designing electronic systems and printed circuit boards (PCBs) to operate at high frequencies and data rates. As digital systems continue to increase in speed and complexity, understanding the principles of hi-speed design becomes increasingly critical for engineers.
This seminar will cover the fundamental concepts and techniques used in hi-speed digital design. Attendees will gain an understanding of signal integrity, power integrity, electromagnetic compatibility (EMC), and other key aspects of designing high-performance electronic systems.
Seminar Objectives
By the end of this hi-speed design seminar, attendees will be able to:
- Understand the challenges and considerations in hi-speed digital design
- Apply signal integrity analysis techniques to ensure reliable data transmission
- Design power delivery networks to maintain power integrity
- Implement EMC best practices to minimize electromagnetic interference
- Select appropriate components and materials for hi-speed applications
- Effectively simulate, prototype, and test hi-speed designs
Who Should Attend?
This hi-speed design seminar is intended for:
- Electrical engineers
- PCB designers
- Signal integrity engineers
- Hardware Engineers
- EMC engineers
- Engineering managers
- Anyone involved in the design of high-speed digital systems
Signal Integrity in Hi-speed Design
Signal integrity (SI) is a crucial aspect of hi-speed digital design. It refers to the ability of an electrical signal to propagate through an interconnect while maintaining its quality and timing characteristics. Poor signal integrity can lead to data errors, reduced system performance, and even complete system failure.
Sources of Signal Integrity Problems
There are several sources of signal integrity issues in hi-speed designs:
Source | Description |
---|---|
Reflections | Caused by impedance mismatches, leading to signal distortion |
Crosstalk | Interference between adjacent signals due to electromagnetic coupling |
Attenuation | Loss of signal strength due to conductor and dielectric losses |
Jitter | Timing variations that can cause data errors |
Simultaneous Switching | Noise generated when multiple outputs switch simultaneously |
Analyzing Signal Integrity
To ensure good signal integrity, designers must carefully analyze and simulate the behavior of signals in their designs. Some common analysis techniques include:
- Time-domain reflectometry (TDR)
- Frequency-domain analysis (S-parameters)
- Eye diagrams
- Bit error rate testing (BERT)
These techniques help designers identify and mitigate signal integrity issues early in the design process, reducing the risk of costly redesigns and production delays.
Best Practices for Signal Integrity
Some best practices for maintaining good signal integrity in hi-speed designs include:
- Match impedances of drivers, receivers, and interconnects
- Minimize trace lengths and avoid unnecessary vias
- Use appropriate termination techniques
- Provide adequate spacing between signals to minimize crosstalk
- Use differential signaling for improved noise immunity
- Simulate and verify signal integrity throughout the design process
Power Integrity in Hi-speed Design
Power integrity (PI) is another critical aspect of hi-speed digital design. It refers to the quality and stability of the power supply voltages delivered to the active components in a system. Poor power integrity can lead to signal integrity issues, EMI, and reduced system reliability.
Power Distribution Networks (PDNs)
The power distribution network is responsible for delivering clean, stable power to all the components in a hi-speed design. A well-designed PDN should have:
- Low impedance across the required frequency range
- Minimal voltage ripple and noise
- Adequate current-carrying capacity
- Proper decoupling and bypass capacitors
Designing for Power Integrity
To ensure good power integrity, designers should follow these guidelines:
- Use appropriate Decoupling capacitors close to power pins
- Minimize inductance in the power delivery path
- Use wide, low-impedance power and ground planes
- Simulate and analyze the PDN impedance profile
- Consider the effects of simultaneous switching noise (SSN)
- Use Voltage Regulator modules (VRMs) for stable power supply
Power Integrity Analysis Techniques
Some common techniques for analyzing power integrity include:
- Impedance analysis
- Frequency-domain analysis (Z-parameters)
- Time-domain analysis (SPICE simulations)
- Measurement techniques (VNA, TDR, spectrum analyzers)
By carefully designing and analyzing the power distribution network, designers can ensure reliable operation of their hi-speed systems.
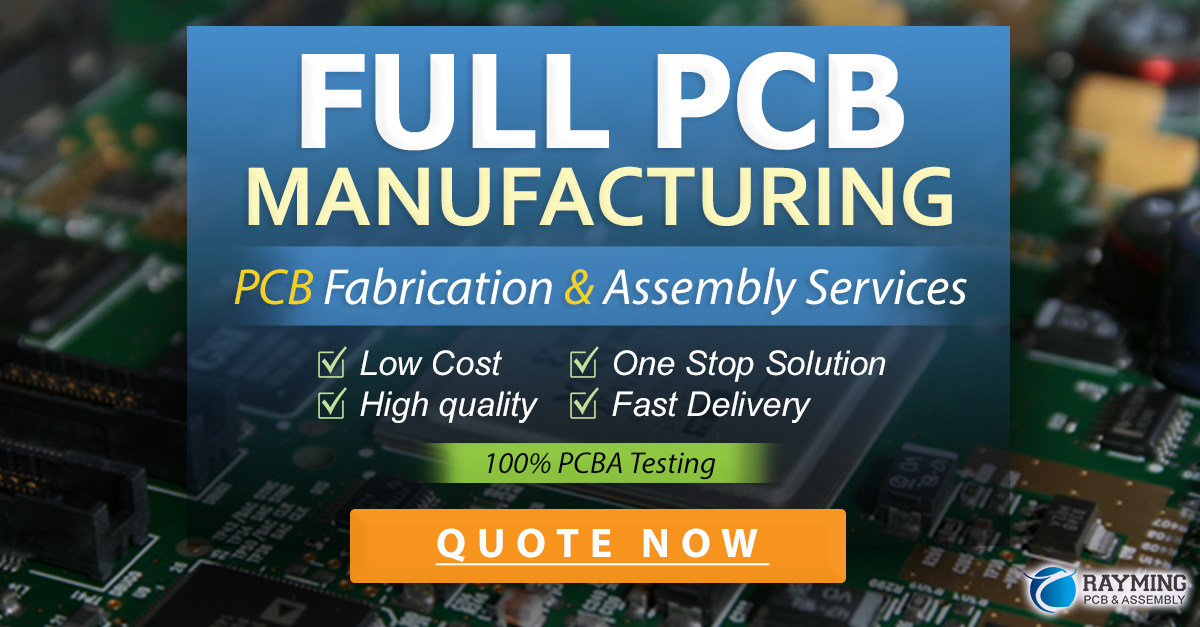
Electromagnetic Compatibility (EMC) in Hi-speed Design
Electromagnetic compatibility (EMC) is the ability of an electronic system to function properly in its electromagnetic environment without causing or being susceptible to electromagnetic interference (EMI). Hi-speed designs are particularly vulnerable to EMC issues due to their high frequencies and fast edge rates.
Sources of EMI
There are two main sources of EMI in hi-speed designs:
- Conducted EMI: Propagates through power lines, signal lines, and ground planes
- Radiated EMI: Propagates through the air as electromagnetic waves
Designing for EMC
To minimize EMI and ensure good EMC performance, designers should follow these best practices:
- Minimize loop areas in signal and power paths
- Use proper grounding and shielding techniques
- Implement appropriate filtering and suppression methods
- Follow layout guidelines for minimizing crosstalk and radiation
- Use EMI-resistant components and packaging
- Comply with relevant EMC standards and regulations
EMC Testing and Certification
Hi-speed designs must often undergo EMC testing and certification to ensure compliance with industry standards and regulations. Some common EMC tests include:
- Radiated emissions testing
- Conducted emissions testing
- Electromagnetic susceptibility (EMS) testing
- Electrostatic discharge (ESD) testing
By designing for EMC and passing the required tests, hi-speed designs can reliably function in their intended electromagnetic environments.
Component and Material Selection for Hi-speed Design
Selecting the right components and materials is crucial for the success of hi-speed designs. The choice of components and materials can significantly impact signal integrity, power integrity, and EMC performance.
Component Selection Criteria
When selecting components for hi-speed designs, consider the following criteria:
- Bandwidth and rise time
- Jitter and noise performance
- Power consumption and heat dissipation
- Packaging and pin configuration
- Compatibility with the chosen signaling standards
Material Selection Criteria
The choice of PCB materials can also greatly affect hi-speed design performance. Consider the following factors when selecting materials:
- Dielectric constant (Dk) and dissipation factor (Df)
- Thermal conductivity and coefficient of thermal expansion (CTE)
- Copper foil roughness and adhesion
- Manufacturability and cost
Material | Dk | Df | Thermal Conductivity (W/mK) | CTE (ppm/°C) |
---|---|---|---|---|
FR-4 | 4.2 | 0.02 | 0.3 | 14 |
Rogers 4350B | 3.48 | 0.0037 | 0.62 | 14 |
Isola I-Tera MT | 3.45 | 0.0035 | 0.5 | 12 |
By carefully selecting components and materials based on the specific requirements of the hi-speed design, designers can optimize performance and ensure reliable operation.
Simulation, Prototyping, and Testing of Hi-speed Designs
Simulating, prototyping, and testing hi-speed designs are essential steps in the design process. These activities help designers validate their designs and identify potential issues before committing to production.
Simulation Tools and Techniques
Some common simulation tools and techniques used in hi-speed design include:
- SPICE-based circuit simulators
- Electromagnetic field solvers
- 3D full-wave simulators
- Statistical analysis tools
These tools help designers analyze signal integrity, power integrity, and EMC performance of their designs.
Prototyping and Testing
After simulation, hi-speed designs should be prototyped and tested to verify their real-world performance. Some important considerations for prototyping and testing include:
- Choosing appropriate test equipment (oscilloscopes, VNAs, spectrum analyzers)
- Designing test fixtures and boards
- Developing test plans and procedures
- Analyzing and interpreting test results
- Iterating on the design based on test findings
By thoroughly simulating, prototyping, and testing hi-speed designs, designers can ensure that their products meet performance, reliability, and compliance requirements.
Conclusion
Hi-speed digital design is a complex and challenging field that requires a deep understanding of signal integrity, power integrity, EMC, and other key concepts. By attending this hi-speed design seminar, engineers can gain the knowledge and skills needed to design reliable, high-performance electronic systems.
Key Takeaways
- Signal integrity is critical for ensuring reliable data transmission in hi-speed designs
- Power integrity is essential for maintaining stable, clean power supply voltages
- Electromagnetic compatibility is crucial for minimizing interference and ensuring regulatory compliance
- Careful component and material selection can optimize hi-speed design performance
- Simulation, prototyping, and testing are essential steps in the hi-speed design process
By applying the principles and techniques covered in this seminar, attendees can confidently tackle the challenges of hi-speed digital design and create successful, cutting-edge electronic products.
Frequently Asked Questions (FAQ)
- What are the main challenges in hi-speed digital design?
-
The main challenges in hi-speed digital design include maintaining signal integrity, ensuring power integrity, minimizing electromagnetic interference, and selecting appropriate components and materials.
-
How can I minimize crosstalk in my hi-speed design?
-
To minimize crosstalk, use appropriate spacing between signals, implement differential signaling, and follow layout guidelines for minimizing electromagnetic coupling.
-
What are the most important factors to consider when selecting PCB materials for hi-speed designs?
-
The most important factors to consider when selecting PCB materials for hi-speed designs are dielectric constant (Dk), dissipation factor (Df), thermal conductivity, and coefficient of thermal expansion (CTE).
-
What simulation tools are commonly used in hi-speed design?
-
Common simulation tools used in hi-speed design include SPICE-based circuit simulators, electromagnetic field solvers, 3D full-wave simulators, and statistical analysis tools.
-
Why is prototyping and testing important in hi-speed design?
- Prototyping and testing are important in hi-speed design to verify the real-world performance of the design, identify potential issues, and ensure that the product meets performance, reliability, and compliance requirements.
Leave a Reply