What is BGA Assembly?
BGA (Ball Grid Array) assembly is a process of attaching electronic components to a printed circuit board (PCB) using a grid of solder balls underneath the component. This advanced packaging technology allows for high-density interconnections between the component and the PCB, making it ideal for complex, high-performance electronic devices. BGA assembly has become increasingly popular in recent years due to its numerous advantages over traditional through-hole and surface-mount technologies.
Advantages of BGA Assembly
- Increased Packaging Density: BGA packages offer a higher density of interconnections compared to other packaging technologies, allowing for more compact and efficient PCB designs.
- Improved Electrical Performance: The shorter lead lengths in BGA packages reduce inductance and improve signal integrity, resulting in better electrical performance.
- Enhanced Thermal Management: BGA packages provide better thermal dissipation due to the large surface area of the solder balls, which helps to distribute heat more evenly across the PCB.
- Reduced PCB Size: The high-density interconnections of BGA packages enable designers to create smaller PCBs, leading to more compact electronic devices.
- Cost-Effective: Although the initial setup costs for BGA assembly may be higher, the overall cost-effectiveness improves with higher production volumes due to the reduced PCB size and improved manufacturing efficiency.
BGA Assembly Process
The BGA assembly process involves several key steps to ensure proper attachment of the BGA component to the PCB. These steps include:
1. PCB Preparation
Before the BGA component can be attached, the PCB must be prepared with the appropriate solder paste stencil. The stencil is designed to apply solder paste to the specific areas where the BGA component will be placed.
2. Solder Paste Application
Solder paste is applied to the PCB using the stencil. The stencil is aligned with the PCB, and the solder paste is spread across the surface using a squeegee. The stencil is then removed, leaving precisely deposited solder paste on the PCB pads.
3. BGA Component Placement
The BGA component is carefully aligned and placed onto the PCB using a pick-and-place machine. The machine uses vision systems and precise positioning mechanisms to ensure accurate placement of the component.
4. Reflow Soldering
After the BGA component is placed, the PCB undergoes a reflow soldering process. The PCB is heated in a reflow oven, causing the solder paste to melt and form a connection between the BGA component and the PCB pads. The reflow profile is carefully controlled to ensure proper solder joint formation and to minimize thermal stress on the components.
5. Inspection and Testing
Once the reflow soldering process is complete, the PCB undergoes inspection and testing to verify the quality of the BGA solder joints. This may include visual inspection, X-ray inspection, and electrical testing to ensure proper functionality and reliability of the assembled PCB.
Challenges in BGA Assembly
While BGA assembly offers numerous benefits, it also presents some challenges that must be addressed to ensure successful implementation.
1. Thermal Management
BGA packages generate significant amounts of heat due to their high density and power consumption. Proper thermal management is essential to prevent overheating and ensure reliable operation of the electronic device. This may involve the use of heat sinks, thermal interface materials, and optimized PCB layouts to dissipate heat effectively.
2. Solder Joint Reliability
The reliability of BGA solder joints is critical to the overall performance and longevity of the electronic device. Factors such as thermal cycling, mechanical stress, and moisture can impact the integrity of the solder joints over time. Proper design, material selection, and process control are necessary to ensure reliable solder joint formation and long-term performance.
3. Rework and Repair
Reworking or repairing BGA assemblies can be challenging due to the high density of interconnections and the difficulty in accessing individual solder joints. Specialized equipment and techniques, such as hot air rework stations and BGA reballing, are required to perform successful rework and repair operations.
4. Process Control
Maintaining tight process control is essential for successful BGA assembly. This includes controlling factors such as solder paste deposition, component placement accuracy, reflow profile, and cleanliness. Implementing statistical process control (SPC) and regular process audits can help to ensure consistent and reliable BGA assembly.
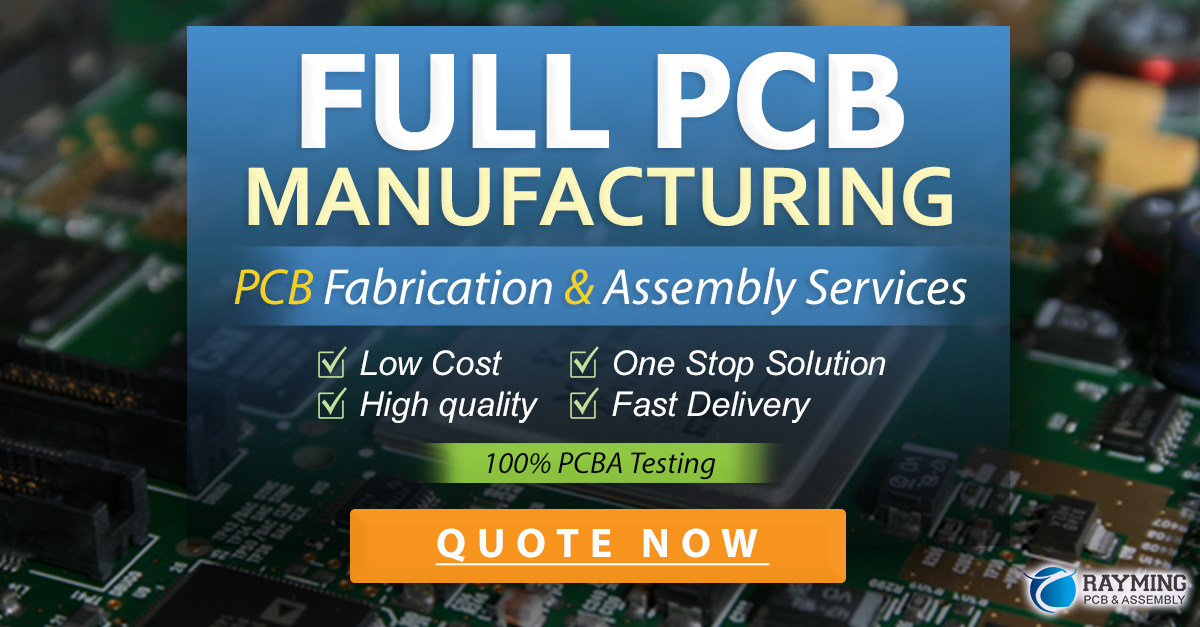
BGA Assembly Equipment and Technologies
To support the growing demand for BGA assembly, various equipment and technologies have been developed to streamline the process and improve quality.
Pick-and-Place Machines
Advanced pick-and-place machines are used to accurately place BGA components onto the PCB. These machines feature high-speed placement heads, vision systems for alignment, and precise motion control to ensure accurate and repeatable component placement.
Machine Type | Placement Speed (cph) | Placement Accuracy (μm) | Vision System | Features |
---|---|---|---|---|
High-Speed | Up to 200,000 | ±30 | High-resolution camera | Multi-nozzle heads, linear motors, advanced software |
Mid-Range | Up to 100,000 | ±50 | Camera-based | Flexible feeder options, user-friendly interface |
Entry-Level | Up to 50,000 | ±100 | Basic camera | Compact design, suitable for low-volume production |
Reflow Ovens
Reflow ovens are used to melt the solder paste and form a connection between the BGA component and the PCB pads. Modern reflow ovens offer precise temperature control, multi-zone heating, and nitrogen atmosphere capabilities to optimize the reflow process and minimize defects.
Oven Type | Heating Zones | Max. Temperature (°C) | Conveyor Speed (cm/min) | Features |
---|---|---|---|---|
Convection | 8-12 | 350 | 30-200 | Forced air convection, good thermal uniformity |
Infrared | 6-10 | 400 | 30-200 | Rapid heating, energy-efficient, suitable for lead-free soldering |
Vapor Phase | 2-4 | 260 | 30-200 | Oxygen-free environment, minimal thermal stress, consistent heating |
Inspection Systems
Automated inspection systems are used to verify the quality of BGA solder joints and detect any defects or anomalies. These systems employ various technologies, such as automated optical inspection (AOI), X-ray inspection, and 3D solder paste inspection (SPI), to provide comprehensive quality control.
Inspection Type | Technology | Detection Capabilities | Features |
---|---|---|---|
AOI | Optical | Surface defects, component placement, solder joint shape | High-speed, non-contact, color imaging |
X-ray | X-ray | Internal defects, voids, bridging, solder joint quality | 2D and 3D imaging, real-time analysis |
SPI | 3D optical | Solder paste volume, height, alignment | Identifies paste deposition issues, prevents downstream defects |
Best Practices for BGA Assembly
To ensure successful BGA assembly, it is essential to follow best practices throughout the design, manufacturing, and testing processes.
1. Design for Manufacturability (DFM)
Incorporate DFM principles during the PCB design stage to optimize the layout for BGA assembly. This includes considering factors such as pad size, pitch, and solder mask design to facilitate proper solder joint formation and minimize defects.
2. Material Selection
Choose appropriate materials, such as PCB substrates, solder paste, and BGA components, that are compatible with the assembly process and meet the performance requirements of the electronic device. Consider factors such as thermal stability, moisture sensitivity, and lead-free compatibility.
3. Process Optimization
Optimize the BGA assembly process parameters, including Solder paste printing, component placement, and reflow soldering, to achieve consistent and reliable results. Regularly monitor and adjust the process based on statistical process control data and quality metrics.
4. Inspection and Testing
Implement a comprehensive inspection and testing strategy to verify the quality of BGA solder joints and detect any defects or anomalies. Utilize automated inspection systems, such as AOI and X-ray, to provide objective and repeatable quality control.
5. Training and Certification
Invest in training and certification programs for personnel involved in BGA assembly to ensure they possess the necessary skills and knowledge to perform the process effectively. This may include training on equipment operation, process control, and quality assurance.
Frequently Asked Questions (FAQ)
- What is the difference between BGA and SMT assembly?
-
BGA (Ball Grid Array) and SMT (Surface Mount Technology) are both methods of attaching electronic components to a PCB. However, BGA uses a grid of solder balls underneath the component for attachment, while SMT uses leads or pads on the sides of the component. BGA allows for higher density interconnections and improved electrical and thermal performance compared to traditional SMT.
-
Can BGA components be reworked or repaired?
-
Yes, BGA components can be reworked or repaired, but it requires specialized equipment and techniques. Hot air rework stations and BGA reballing are commonly used methods for reworking or repairing BGA assemblies. However, the process can be challenging due to the high density of interconnections and the difficulty in accessing individual solder joints.
-
What are the common defects in BGA assembly?
-
Common defects in BGA assembly include solder bridging, voids, head-in-pillow (HIP), and misalignment. Solder bridging occurs when solder inadvertently connects adjacent pads or balls. Voids are gaps or cavities within the solder joint that can affect joint strength and reliability. HIP defects happen when the BGA component fails to properly collapse onto the PCB pad during reflow. Misalignment refers to the improper positioning of the BGA component on the PCB.
-
How can thermal management be addressed in BGA assembly?
-
Thermal management is critical in BGA assembly due to the high density and power consumption of BGA packages. Effective thermal management strategies include using heat sinks, thermal interface materials, and optimized PCB layouts to dissipate heat. Designers can also consider using thermally enhanced PCB substrates, such as metal-Core PCBs or insulated metal substrates (IMS), to improve heat dissipation.
-
What are the key considerations for selecting a BGA assembly partner?
- When selecting a BGA assembly partner, consider factors such as their experience and expertise in BGA assembly, quality control processes, equipment and technology capabilities, and customer support. Look for a partner with a proven track record of successful BGA assembly projects, robust quality management systems, and the ability to meet your specific requirements and timeline. Additionally, consider their ability to provide value-added services, such as design support, prototyping, and supply chain management.
Conclusion
BGA assembly has become an essential technology for manufacturing high-performance, compact electronic devices. Its advantages, such as increased packaging density, improved electrical performance, and enhanced thermal management, make it an attractive choice for a wide range of applications. However, successful BGA assembly requires careful consideration of design, materials, processes, and quality control.
By understanding the challenges and best practices associated with BGA assembly, electronics manufacturers can optimize their processes and ensure reliable, high-quality assemblies. Investing in advanced equipment, technologies, and skilled personnel is crucial to staying competitive in the rapidly evolving electronics industry.
As electronic devices continue to become more complex and compact, the demand for BGA assembly capabilities will only continue to grow. By staying at the forefront of BGA assembly technology and best practices, electronics manufacturers can position themselves to meet the ever-increasing demands of the market and deliver innovative, reliable products to their customers.
Leave a Reply