What is PCB Solder Mask?
PCB solder mask, also known as solder resist or solder stop mask, is a thin lacquer-like layer of polymer applied to the copper traces of a printed circuit board (PCB). Its primary purpose is to prevent solder bridges from forming between closely spaced solder pads during the soldering process. Additionally, the solder mask protects the copper traces from oxidation and provides electrical insulation.
The solder mask is applied to the PCB surface, covering the entire board except for the areas where components will be soldered, such as pads, through-holes, and exposed copper features. By selectively exposing the desired areas for soldering, the mask helps to ensure precise and reliable solder connections while minimizing the risk of short circuits.
Benefits of Using PCB Solder Mask
-
Prevents solder bridges: The solder mask keeps solder from flowing between adjacent pads or traces, reducing the risk of short circuits.
-
Protects copper traces: The mask layer shields the copper traces from oxidation, scratches, and other environmental factors that could degrade their performance.
-
Provides electrical insulation: Solder mask acts as an insulating layer, preventing unwanted electrical contact between components and traces.
-
Enhances PCB aesthetics: Solder masks are available in various colors, allowing for improved visual appearance and better contrast for component labels and markings.
-
Facilitates automated assembly: A well-applied solder mask ensures that only the intended areas are exposed for soldering, enabling more efficient and accurate automated PCB assembly processes.
Types of PCB Solder Mask
There are four main types of PCB solder mask:
- Liquid Photoimageable Solder Mask (LPISM)
- Dry Film Photoimageable Solder Mask (DFISM)
- Liquid Photoimageable Solder Mask (LPI)
- Peelable Solder Mask (PSM)
Each type has its own unique characteristics, advantages, and disadvantages. Let’s explore each one in detail.
1. Liquid Photoimageable Solder Mask (LPISM)
Liquid Photoimageable Solder Mask (LPISM) is the most common type of solder mask used in PCB manufacturing. LPISM is a liquid polymer that is applied to the PCB surface using screen printing, spray coating, or curtain coating methods. The mask is then exposed to UV light through a photomask, which hardens the exposed areas while leaving the unexposed areas soluble. The unexposed areas are then removed using a developer solution, revealing the desired openings for soldering.
Advantages of LPISM
-
High resolution: LPISM can achieve fine pitch and high-density patterns, making it suitable for complex PCB designs.
-
Excellent adhesion: The liquid nature of LPISM allows for better adhesion to the PCB surface, reducing the risk of delamination.
-
Flexibility in application: LPISM can be applied using various methods, allowing for adaptability to different PCB manufacturing processes.
-
Cost-effective: LPISM is generally more cost-effective compared to other solder mask types, especially for high-volume production.
Disadvantages of LPISM
-
Longer processing time: The multi-step application process of LPISM can be time-consuming, especially for complex designs.
-
Environmental concerns: Some LPISM formulations may contain volatile organic compounds (VOCs) or other chemicals that can be harmful to the environment if not handled properly.
2. Dry Film Photoimageable Solder Mask (DFISM)
Dry Film Photoimageable Solder Mask (DFISM) is a solid photopolymer film that is laminated onto the PCB surface using heat and pressure. Like LPISM, DFISM is exposed to UV light through a photomask, and the unexposed areas are removed using a developer solution. DFISM offers several advantages over liquid solder masks, particularly in terms of processing time and environmental impact.
Advantages of DFISM
-
Faster processing: The lamination process of DFISM is generally faster than the application of liquid solder masks, reducing overall production time.
-
Consistent thickness: DFISM films have a uniform thickness, ensuring consistent solder mask coverage across the entire PCB surface.
-
Environmentally friendly: DFISM does not contain VOCs or other harmful chemicals, making it a more eco-friendly option compared to some LPISM formulations.
-
Reduced equipment maintenance: The use of solid film eliminates the need for regular cleaning and maintenance of liquid solder mask application equipment.
Disadvantages of DFISM
-
Higher material cost: DFISM films are typically more expensive than liquid solder mask materials.
-
Limited flexibility: The solid nature of DFISM may limit its ability to conform to irregular PCB surfaces or extreme contours.
-
Potential for air entrapment: If not laminated properly, air bubbles can become trapped between the DFISM and the PCB surface, leading to defects in the solder mask.
3. Liquid Photoimageable Solder Mask (LPI)
Liquid Photoimageable Solder Mask (LPI) is a type of liquid solder mask that combines the advantages of LPISM and DFISM. LPI is applied as a liquid but has the properties of a dry film once cured. This unique combination allows for improved resolution, adhesion, and processing efficiency compared to traditional liquid solder masks.
Advantages of LPI
-
High resolution: LPI can achieve fine pitch and high-density patterns, similar to LPISM.
-
Excellent adhesion: The liquid application of LPI ensures good adhesion to the PCB surface, minimizing the risk of delamination.
-
Faster processing: LPI typically requires fewer processing steps compared to LPISM, resulting in shorter production times.
-
Improved environmental profile: Many LPI formulations have reduced VOC content and are more environmentally friendly compared to traditional LPISM.
Disadvantages of LPI
-
Higher cost: LPI materials and processing equipment can be more expensive than traditional LPISM.
-
Specialized equipment: Implementing LPI in a PCB manufacturing process may require specialized application and curing equipment.
4. Peelable Solder Mask (PSM)
Peelable Solder Mask (PSM) is a temporary solder mask that is applied to the PCB surface to protect specific areas during the soldering process. PSM is typically a latex-based material that can be easily peeled off after soldering, leaving the protected areas intact. This type of solder mask is particularly useful for selective soldering applications or for protecting sensitive components during rework or repair.
Advantages of PSM
-
Temporary protection: PSM provides temporary protection for specific areas of the PCB during soldering, allowing for selective soldering or rework.
-
Easy removal: The latex-based material can be easily peeled off after soldering, without leaving residue or damaging the PCB.
-
Cost-effective for small-scale applications: PSM can be a cost-effective solution for low-volume production or rework processes.
Disadvantages of PSM
-
Limited durability: PSM is not designed for long-term protection and is not suitable as a permanent solder mask solution.
-
Manual application: Applying and removing PSM is typically a manual process, which can be time-consuming for large-scale production.
-
Potential for residue: If not removed properly, PSM can leave residue on the PCB surface, which may affect the performance of the circuit.
Choosing the Right PCB Solder Mask
When selecting the appropriate solder mask for a PCB project, several factors should be considered:
-
PCB design complexity: High-density designs with fine pitch components may require a solder mask with higher resolution capabilities, such as LPISM or LPI.
-
Production volume: For high-volume production, cost-effective solutions like LPISM may be more suitable, while low-volume or prototype projects may benefit from the faster processing of DFISM or LPI.
-
Environmental requirements: If environmental sustainability is a priority, solder masks with reduced VOC content or DFISM may be preferred.
-
Specific application needs: For selective soldering or rework applications, PSM can provide temporary protection, while permanent solder masks like LPISM, DFISM, or LPI are better suited for long-term protection.
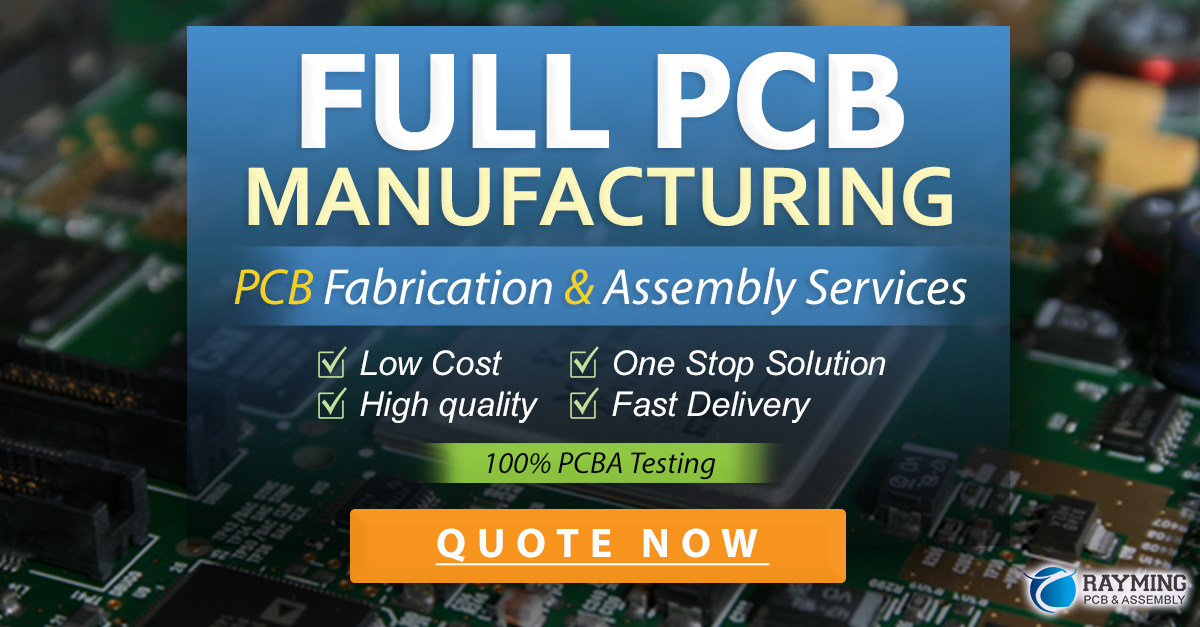
Solder Mask Colors
Solder masks are available in a variety of colors, with green being the most common. Other colors include red, blue, yellow, black, and white. The choice of color is primarily driven by aesthetic preferences and the need for contrast to improve readability of component markings and labels. Some colors, such as black or white, may also have functional benefits, such as improved heat dissipation or light reflection.
Color | Advantages | Disadvantages |
---|---|---|
Green | – Most common color – Good contrast for white silkscreen – Aesthetically pleasing |
– May not provide sufficient contrast for some components |
Red | – High visibility – Good contrast for white silkscreen |
– May be too bright for some applications |
Blue | – Good contrast for white silkscreen – Aesthetically pleasing |
– May not provide sufficient contrast for some components |
Yellow | – High visibility | – May be too bright for some applications – Limited contrast for white silkscreen |
Black | – Provides good contrast for most component colors – Improved heat dissipation |
– May make it difficult to read silkscreen markings |
White | – Provides good contrast for most component colors – Improved light reflection |
– May show dirt or stains more easily |
Solder Mask Thickness
The thickness of the solder mask plays a crucial role in its performance and the overall quality of the PCB. Solder mask thickness is typically measured in microns (μm) or mils (1 mil = 25.4 μm). The ideal thickness depends on several factors, including the PCB design, component density, and the specific solder mask material used.
Thickness Range | Advantages | Disadvantages |
---|---|---|
10-20 μm | – Suitable for very fine pitch components – Improved resolution |
– May be less durable – Potential for solder mask damage during handling |
20-30 μm | – Good balance between resolution and durability – Suitable for most PCB designs |
– May not be suitable for extremely fine pitch components |
30-50 μm | – Increased durability – Better protection against moisture and contaminants |
– Reduced resolution – May not be suitable for high-density designs |
In general, a solder mask thickness between 20-30 μm is considered optimal for most PCB applications, offering a good balance between resolution, durability, and protection. However, the final choice of thickness should be based on the specific requirements of the PCB design and the recommendations of the solder mask manufacturer.
FAQ
-
Q: What is the purpose of a solder mask on a PCB?
A: The main purposes of a solder mask on a PCB are to prevent solder bridges from forming between closely spaced pads during soldering, protect the copper traces from oxidation and damage, and provide electrical insulation between components. -
Q: What is the most common type of solder mask used in PCB manufacturing?
A: Liquid Photoimageable Solder Mask (LPISM) is the most common type of solder mask used in PCB manufacturing due to its high resolution, excellent adhesion, and cost-effectiveness for high-volume production. -
Q: Are there any environmental concerns associated with solder masks?
A: Some Liquid Photoimageable Solder Mask (LPISM) formulations may contain volatile organic compounds (VOCs) or other harmful chemicals that can be detrimental to the environment if not handled properly. However, there are more eco-friendly options available, such as Dry Film Photoimageable Solder Mask (DFISM) or Low VOC LPISMs. -
Q: What factors should I consider when choosing a solder mask for my PCB project?
A: When selecting a solder mask, consider factors such as the complexity of your PCB design, production volume, environmental requirements, and specific application needs (e.g., selective soldering or rework). These factors will help you determine the most suitable type of solder mask for your project. -
Q: Does the color of the solder mask affect the performance of the PCB?
A: The color of the solder mask is primarily chosen for aesthetic reasons and to improve the readability of component markings and labels. However, some colors, such as black or white, may offer functional benefits like improved heat dissipation or light reflection.
Leave a Reply