Overview of 24 Layer HDI PCBs
High density interconnect (HDI) printed circuit boards (PCBs) are advanced PCBs that enable the use of microvias and tight trace/spacing to interconnect chips and components. 24 layer HDI PCBs take this a step further with even higher wiring densities by stacking 24 conductive layers separated by insulating dielectric layers.
24 layer HDI PCBs provide the following key benefits:
- Extremely high component density and interconnectivity
- Support for advanced packaging methods like chip scale packaging
- Miniaturization of PCB footprint area and thickness
- Ideal for complex, high speed designs like network switches, computer servers, medical devices etc.
However, manufacturing these boards requires specialized expertise and equipment. In this article, we’ll look at what to consider when picking the right PCB manufacturer for your 24 layer HDI board.
Key Factors to Consider
HDI PCB Manufacturing Experience
Given the complexity involved, it’s crucial to choose a manufacturer with extensive experience in building high layer count HDI boards. They should have a strong track record of working on projects with 16+ conductive layers and producing quality boards on time.
Ideally, they should have over a decade of experience manufacturing 10+ layer HDI PCBs using the latest fabrication processes. Verify their expertise by checking project samples/case studies on their website.
Manufacturing Capabilities
The PCB fabricator should have advanced manufacturing capabilities including:
- Lamination presses – To laminate the 24 conductive and dielectric layers together precisely. Auto-alignment and pressure uniformity is key.
- Laser direct imaging (LDI) – To pattern tight traces and microvias accurately on each layer. LDI offers higher precision versus traditional printing methods.
- Automated optical inspection (AOI) – For inspecting each layer to catch any defects early. Helps improve overall yield.
- X-Ray drilling – To drill extremely small microvias (as low as 60um) through multiple layers. Maintains hole position accuracy.
- Impedance control – To tightly control trace impedance on all 24 layers, critical for high speed signaling.
- ENIG Surface Finish – Electroless Nickel Immersion Gold finish recommended for optimal solder joint reliability.
The manufacturer should have advanced SMT assembly lines as well to support component mounting.
Quality Certifications
Reputable 24 layer HDI PCB makers should have quality management certifications like ISO 9001, ISO 13485, AS9100 etc. This ensures they follow standardized fabrication and inspection procedures.
Key certs to look for include:
- IPC 6012 Class 3 certification – Confirms capabilities to build high density interconnects
- IPC CE marking – Certifies conformity to EU standards for PCB quality and reliability
Engineering Support
The PCB manufacturer should provide engineering support during design, fabrication and assembly. This includes:
- DFM analysis – Design for Manufacturability checks to catch any issues early
- Stackup design – Help finalize optimal 24 layer stackup based on your specific requirements
- CAM file generation – Ensure Gerber files are compatible with their processes
- Prototype builds – Assemble initial prototypes to validate design before full production
- AOI review – Share AOI data to collaborate on resolving any defects
This helps mitigate risks and improves overall quality.
Competitive Pricing
Given the complexity, 24 layer HDI PCBs can be cost prohibitive if the manufacturer’s pricing is too high. Work with the PCB company to optimize the design to reduce layers or stackup if possible.
Compare pricing between a few shortlisted vendors to find one that offers a good balance of quality and affordability. Be wary of vendors with abnormally low pricing as that may indicate lack of experience or capabilities.
Finding the Right 24 Layer HDI PCB Partner
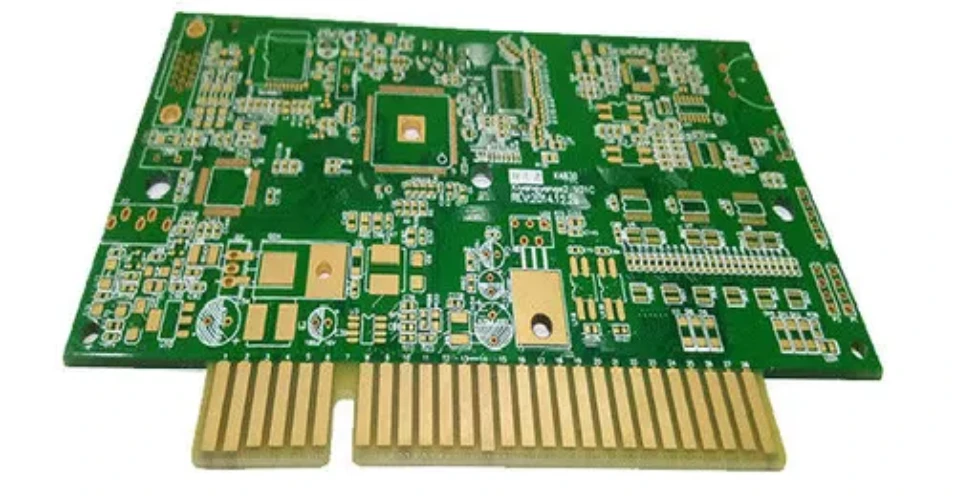
With the key factors above in mind, here are some steps to selecting the right 24 layer HDI PCB manufacturer:
1. Research Industry Leaders
Researched reputed PCB manufacturers with strong expertise in building very high layer count HDI boards. Good places to start include industry association directories like JPCA for Japanese companies.
2. Evaluate Company Capabilities
Thoroughly evaluate company websites, case studies, quality certifications etc. to validate their experience and technical capabilities as discussed earlier. Create a shortlist of vendors that meet the critical criteria.
3. Request Quotes
Contact your shortlisted vendors and provide complete project requirements. Have them provide a written quotation detailing their capabilities, lead times, pricing etc.
4. Review Prototypes/Samples
If possible, request existing customer project samples or engage them to build a small prototype PCB order first. Review the quality firsthand before deciding.
5. Finalize Optimal Partner
Select the PCB manufacturer that best matches your specifications, budget, quality needs and offers the engineering support you need. Do a factory audit if needed for extra assurance.
By carefully following the above process, you can identify and work with a reliable 24 layer HDI PCB fabrication partner for your project. This helps mitigate risks and ensures high quality board production.
Now let’s look at a few leading manufacturers well suited for advanced 24 layer boards.
Recommended 24 Layer HDI PCB Manufacturers
Here are some reputed PCB fabricators with proven capabilities to produce high quality 24 layer HDI boards:
TT Electronics (Optek Technology)
- One of the leading global PCB manufacturers headquartered in the UK
- Decades of experience building 16-36+ layer HDI boards
- Specialized in aerospace, defense, industrial, medical and automotive industries
- Facilities in North America, Europe and Asia Pacific regions
- ISO 9001 and AS9100D certified
AT&S
- Europe’s largest PCB manufacturer based in Austria
- Highly specialized in building HDI boards with 16-36+ layers
- Boasts advanced manufacturing facilities across Europe and Asia
- Key supplier to automotive, industrial, medical, telecom sectors
- Has IPC 6012 Class 3 and IPC-A-600 Class 3 certifications
TTM Technologies
- One of the top PCB manufacturers worldwide with over 30 production plants
- Extensive experience with high layer count HDI boards up to 30 layers
- Specialized in aerospace, defense, medical, telecom, industrial sectors
- Facilities spread globally across North America, Europe and Asia
- Maintains ISO 13485 and AS9100D certifications
Tripod Technology
- Leading PCB and PCBA manufacturer based in Taiwan
- Known for manufacturing complex HDI boards with 16-32+ layers
- Huge customer base in computing, telecom, automotive and consumer industries
- Maintains advanced production facilities in Taiwan and China
- ISO 9001 and ISO 13485 certified
The companies above have proven expertise in fabricating advanced 24 layer HDI PCBs cost effectively. Partnering with them provides access to world class production infrastructure.
Key Takeaways
- Choose manufacturer with 10+ years experience in 16+ layer HDI PCBs
- Look for advanced capabilities like LDI, X-Ray drilling, AOI etc.
- Verify quality certifications – IPC 6012 Class 3, ISO 13485 etc.
- Get engineering support for DFM, stackup design, prototyping etc.
- Research leading vendors; evaluate capabilities thoroughly
- Build prototypes first before full production orders
By selecting the right partner, you can ensure flawless production of 24 layer HDI boards.
24 Layer HDI PCBs: Frequently Asked Questions
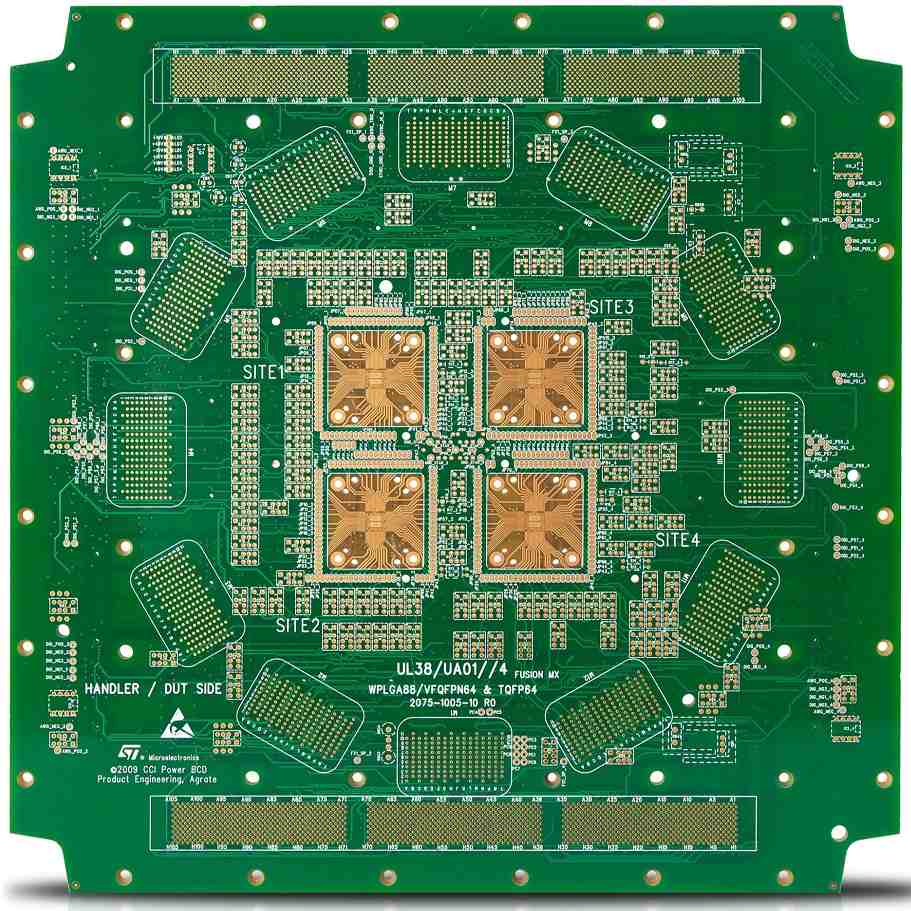
Here are some common questions about 24 layer HDI PCB manufacturing:
Q1. What are typical applications of 24 layer HDI PCBs?
Some common applications include:
- High speed switches, routers, servers
- Aerospace and defense electronics
- Advanced driver assistance systems (ADAS)
- High density medical devices
- 5G base station equipment
- Semiconductor packaging substrates
The ultra high wiring density enables miniaturization and complex circuit integration needed in these products.
Q2. What are the typical layer stackups used?
Here are some common 24 layer stackup configurations:
Layer Type | Example 1 | Example 2 |
---|---|---|
Outer Layers | L1, L24 | L1, L24 |
Signal Layers | L2-L15 | L2-L11 |
Ground Layers | L8, L16 | L4, L8, L12 |
Power Layers | L17-L23 | L16-L22 |
Total Layers | 24 | 24 |
The signal layers are interleaved between ground and power planes to control impedance and noise.
Q3. What panel sizes are available?
Maximum panel sizes for 24 layer boards can reach:
- MM600 – 584 x 620 mm
- MM700 – 620 x 730 mm
- MM800 – 730 x 810 mm
Larger panel sizes help maximize PCB layout area and improve economies of scale.
Q4. What are typical layer to layer registration tolerances?
For 24L HDI boards, typical registration tolerances are:
- Layer to layer: 40um
- Line width: +/- 10um
- Line spacing: +/- 10um
Tighter tolerances help achieve precision interconnects even at 24 layers.
Q5. What are typical lead times?
For small to medium volumes (<1000 pieces), typical lead times range from 2 to 4 weeks. For larger volumes, lead times scale to 6-8 weeks or more.
Building the manufacturing tooling like the lamination presses adds to lead time. Expedited builds can ship in 1-2 weeks for quick-turn requirements.
Conclusion
24 layer HDI PCB manufacturing requires an extremely capable partner. By selecting a vendor with proven expertise in fabricating advanced HDI boards and validating their qualifications thoroughly, you can ensure flawless execution. Partnering with the right manufacturer enables you to harness the benefits of 24 layer HDI technology and deploy highly complex designs in your products.
Leave a Reply